***Disclaimer: The following summary contains information gathered from various sources such as product descriptions, technical specifications and catalogs. While efforts have been made to provide accurate details, inaccuracies may occur. It is advised to verify all information by contacting Bosch Rexroth directly.***
The Bosch Rexroth AL A10F E 37 /52R-VCF60N002 -S1884 (R902505746) is a medium pressure motor designed for both open and closed circuit applications, offering a compact solution thanks to its space-saving construction with a recessed mounting flange. The motor is recognized for its ability to handle high speeds while maintaining a long service life and delivering high power density. Users will appreciate the low operating noise, which contributes to a more comfortable working environment.
This model is equipped with a swashplate design and is suitable for integration into mechanical gearboxes. It is built to withstand nominal pressures of up to bar and can cope with maximum pressures of bar, indicating robust performance under challenging conditions. The AL A10F E 37 /52R-VCF60N002 -S1884 motor also comes with optional features that enhance its functionality, including an integrated anticavitation valve that makes it ideal for fan drive applications where cavitation can be a concern.
Furthermore, there's an option for a speed sensor, adding to the versatility of this motor by allowing precise control over the motor's speed—a critical factor in many industrial processes. The combination of these features makes this Bosch Rexroth motor an efficient choice for those looking for reliable performance in hydraulic systems within various application contexts.
$2,555.00 USD
More are expected on May 4, 2026
Status: This product is temporarily out of stock.
Qty: Delivered as early as May 4, 2026 when ordered in
Space-saving construction due to recessed mounting flange Approved for high speeds Long service life High power density Low operating noise Optional with integrated anti-cavitation valve, e.g. for fan drives Optional with speed sensor Swashplate design
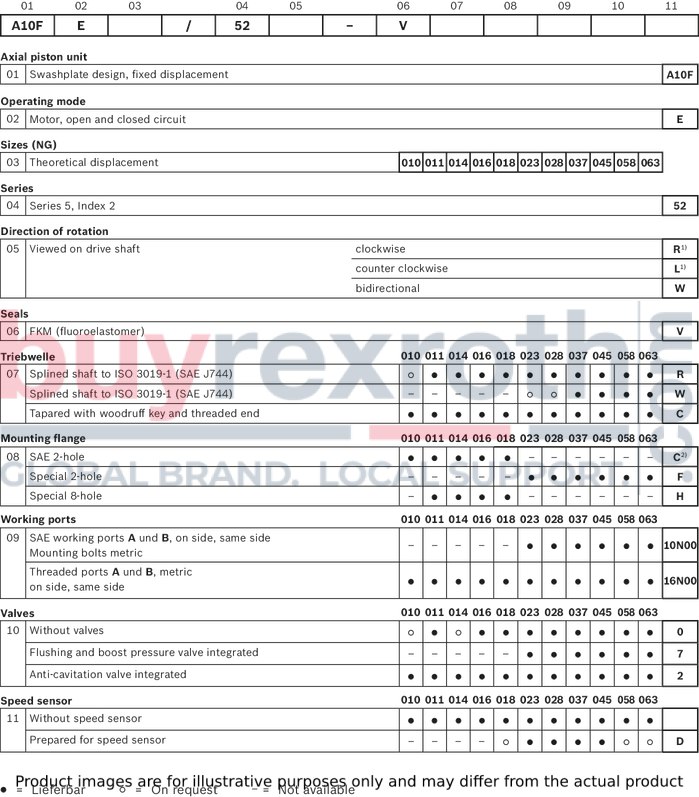
1) | Only necessary in conjunction with valve configuration "2" (integrated anti cavitation valve) |
2) | Drive shaft R with flange C on sizes 10 … 18 in preparation |
Table of values
Size |
10 | 11 | 14 | 16 | 18 | 23 | 28 | 37 | 45 | 58 | 63 | |||
Displacement |
Vg |
cm³ |
10.6 | 11.5 | 14.1 | 16.1 | 18 | 23.5 | 28.5 | 36.7 | 44.5 | 58 | 63.1 | |
Nominal pressure |
pnom |
bar |
280 | 280 | 280 | 280 | 280 | 280 | 280 | 280 | 280 | 280 | 280 | |
Maximum pressure |
pmax |
bar |
350 | 350 | 350 | 350 | 350 | 350 | 350 | 350 | 350 | 350 | 350 | |
Maximum speed 1) |
nnom |
rpm |
5000 | 4200 | 4200 | 4200 | 4200 | 4900 | 4700 | 4200 | 4000 | 3600 | 3400 | |
Inlet flow |
at nnom |
qV |
l/min |
53 | 48 | 59 | 68 | 76 | 115 | 134 | 154 | 178 | 209 | 215 |
Power |
at nnom and pnom |
P |
kW |
24.7 | 22.5 | 27.6 | 31.6 | 35.3 | 53.6 | 62.5 | 71.8 | 83.1 | 97.4 | 100.1 |
Starting torque |
at nnom and pnom |
M0 |
Nm |
37.5 | 30 | 45 | 53 | 67.5 | 75 | 105 | 125 | 170 | 205 | 230 |
Torque |
at pnom |
M |
Nm |
47 | 51 | 63 | 72 | 80 | 105 | 127 | 163 | 198 | 258 | 281 |
Rotary stiffness |
Drive shaft R |
c |
kNm/rad |
14.835 | 28.478 | 28.478 | 46.859 | 46.859 | 80.59 | 80.59 | ||||
Drive shaft W |
c |
kNm/rad |
38.489 | 34.489 | 60.907 | 60.907 | ||||||||
Drive shaft C |
c |
kNm/rad |
15.084 | 18.662 | 18.662 | 18.662 | 18.662 | 30.017 | 30.017 | 46.546 | 46.546 | 87.667 | 87.667 | |
Moment of inertia for rotary group |
JTW |
kg·m² |
0.0006 | 0.00093 | 0.00093 | 0.00093 | 0.00093 | 0.0017 | 0.0017 | 0.0033 | 0.0033 | 0.0056 | 0.0056 | |
Maximum angular acceleration |
ɑ |
rad/s² |
8000 | 6800 | 6800 | 6800 | 6800 | 5500 | 5500 | 4000 | 4000 | 3300 | 3300 | |
Case volume |
V |
l |
0.1 | 0.15 | 0.15 | 0.15 | 0.15 | 0.6 | 0.6 | 0.7 | 0.7 | 0.8 | 0.8 | |
Weight (approx.) |
m |
kg |
5 | 6.5 | 6.5 | 6.5 | 6.5 | 12 | 12 | 17 | 17 | 22 | 22 |
1) | At least 18 bar required at low pressure side |
Note
The values in the table are theoretical values, without consideration of efficiencies and tolerances. The values are rounded. Exceeding the maximum or falling below the minimum permissible values can lead to a loss of function, a reduction in operational service life or total destruction of the axial piston unit. We recommend testing the loads by means of experiment or calculation / simulation and comparison with the permissible values.
Determining the operating characteristics |
||
Inlet flow |
![]() |
[l/min] |
Rotational speed |
![]() |
[rpm] |
Torque |
![]() |
[Nm] |
Power |
![]() |
[kW] |
Key |
|
Vg |
Displacement per revolution [cm3] |
Δp |
Differential pressure [bar] |
n |
Rotational speed [rpm] |
ηv |
Volumetric efficiency |
ηhm |
Hydraulic-mechanical efficiency |
ηt |
Total efficiency (ηt = ηv • ηhm) |
Hydraulic fluids
The axial piston unit is designed for operation with mineral oil HLP according to DIN 51524.
Application instructions and requirements for hydraulic fluids should be taken from the following data sheets before the start of project planning:
90220: Hydraulic fluids based on mineral oils and related hydrocarbons 90221: Environmentally acceptable hydraulic fluids
For operation with environmentally acceptable fluids please consult us.
Viscosity and temperature of hydraulic fluids
|
Viscosity |
Shaft |
Temperature1) |
Comment |
Cold start |
νmax ≤ 1600 mm²/s |
NBR2) |
ϑSt ≥ -40 °C |
t ≤ 1 min, without load (p ≤ 30 bar), n ≤ 1000 rpm, |
FKM |
ϑSt ≥ -25 °C |
|||
Warm-up phase |
ν = 400 … 1600 mm²/s |
|
t ≤ 15 min, p ≤ 0.7 • pnom and n ≤ 0.5 • nnom |
|
Continuous operation |
ν = 10 … 400 mm²/s3) |
NBR2) |
ϑ ≤ +78 °C |
measured at port L |
FKM |
ϑ ≤ +103 °C |
|||
νopt = 16 … 36 mm²/s |
range of optimum operating viscosity and efficiency |
|||
Short-term operation |
νmin = 7 … 10 mm²/s |
NBR2) |
ϑ ≤ +78 °C |
t ≤ 3 min, p ≤ 0.3 • pnom measured at port L |
FKM |
ϑ ≤ +103 °C |
1) | If the specified temperatures cannot be maintained due to extreme operating parameters, please contact us. |
2) | Special version, please contact us. |
3) | Equates e.g. with the VG 46 a temperature range of +5 °C to +85 °C (see selection diagram) |
Explanatory note regarding the selection of hydraulic fluid
The hydraulic fluid should be selected such that the operating viscosity in the operating temperature range is within the optimum range (vopt see selection diagram).
Selection diagram
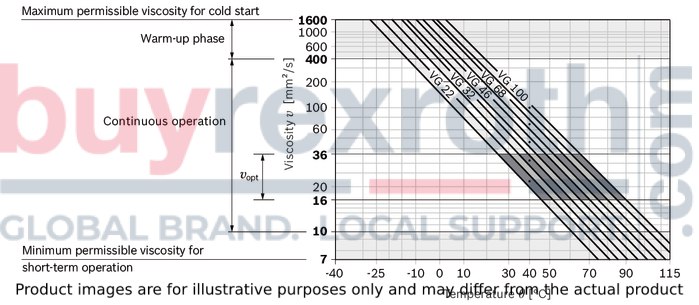
Filtration of the hydraulic fluid
Finer filtration improves the cleanliness level of the hydraulic fluid, which increases the service life of the axial piston unit.
A cleanliness level of at least 20/18/15 is to be maintained according to ISO 4406.
At a hydraulic fluid viscosity of less than 10 mm²/s (e.g. due to high temperatures in short-term operation) at the drain port, a cleanliness level of at least 19/17/14 according to ISO 4406 is required.
For example, the viscosity is 10 mm²/s at:
HLP 32 a temperature of 73°C HLP 46 a temperature of 85°COperating pressure range
Pressure at working port A or B |
Definition |
||
Nominal pressure |
pnom |
see table of values |
The nominal pressure corresponds to the maximum design pressure. |
Maximum pressure |
pmax |
see table of values |
The maximum pressure corresponds to the maximum operating pressure within the single operating period. The sum of the single operating periods must not exceed the total operating period. |
Single operating period |
2.5 s |
||
Total operating period |
300 h |
||
Minimum pressure (high-pressure side) |
pHP min |
10 bar |
Minimum pressure on high- or low-pressure side (port A or B) required to prevent damage to the axial piston unit. |
Minimum pressure (low-pressure side) |
pLP min |
see diagram "Permissible rotational speed in relation to outlet pressure" |
|
Rate of pressure change |
Definition |
||
Rate of pressure change |
RA max |
16000 bar/s |
Maximum permissible rate of pressure build-up and reduction during a pressure change over the entire pressure range. |
Case pressure at port L |
Definition |
||
Motor operation mode |
pL max |
4 bar absolute |
Maximum permissible case pressure measured at port L or L1 |
Pump operating mode |
pL max |
2 bar absolute |
Note
Working pressure range valid when using hydraulic fluids based on mineral oils. Values for other hydraulic fluids, please contact us.Permissible rotational speed in relation to outlet pressure

Pressure definition
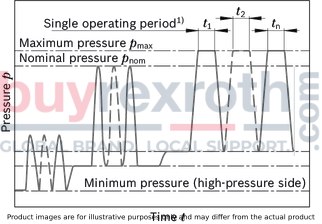
1) | Total operating period = t1 + t2 + ... + tn |
Rate of pressure change

Direction of flow
Direction of rotation, viewed on drive shaft |
|
clockwise |
counter-clockwise |
A to B |
B to A |
Permissible radial and axial forces of the drive shaft
Size |
10 | 11 | 14 | 16 | 18 | 23 | 28 | 37 | 45 | 58 | 63 | ||||
Splined shaft |
Code |
R | R | R | R | R | R, W | R, W | R, W | R, W | R, W | R, W | |||
Tapered shaft |
Code |
C | C | C | C | C | C | C | C | C | C | C | |||
Maximum radial force |
![]() |
![]() |
Fq max |
N |
250 | 350 | 350 | 350 | 350 | 1200 | 1200 | 1500 | 1500 | 1700 | 1700 |
Maximum axial force |
![]() |
± Fax max |
N |
400 | 700 | 700 | 700 | 700 | 1000 | 1000 | 1500 | 1500 | 2000 | 2000 |
Port plate 16
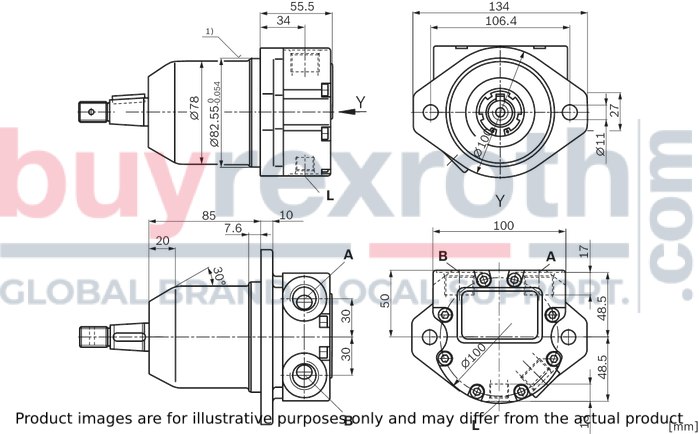
1) | Flange ISO 3019-1 |
Drive shaft

Ports
Size |
10 | ||
A, B |
Working port |
Size |
M18 × 1,5; 17 mm deep |
Standard |
DIN 3852 | ||
State on delivery |
With protective cover (must be connected) | ||
L |
Drain port |
Size |
M14 × 1,5; 13 mm deep |
Standard |
DIN 3852 | ||
State on delivery |
With protective cover (must be connected) |
Sizes 11 … 18
Mounting flange H

Mounting flange C

1) | Flange ISO 3019-1 |
Drive shafts

1) | Toothing data valid for basic number of teeth 48 |
Dimensions
Mounting flange |
N1 |
N2 |
N3 |
H |
126.6 |
144.2 |
19 |
C |
‒ |
151.8 |
24 |
Ports
Size |
11 | 14 | 16 | 18 | ||
A, B |
Working port |
Size |
M18 × 1,5; 12 mm deep | |||
Standard |
DIN 3852 | |||||
State on delivery |
With protective cover (must be connected) | |||||
L |
Drain port |
Size |
M14 × 1,5; 12 mm deep | |||
Standard |
DIN 3852 | |||||
State on delivery 1) |
With protective cover (observe installation instructions) | |||||
L1 |
Drain port |
Size |
M14 × 1,5; 12 mm deep | |||
Standard |
DIN 3852 | |||||
State on delivery 1) |
Plugged (observe installation instructions) |
1) | Unless otherwise specified. Other layouts on request. |
Sizes 23 and 28
Port plate 10

Port plate 16

Drive shafts

1) | Toothing data valid for basic number of teeth 48 |
Ports
Size |
23 | 28 | ||
A, B |
Working port |
Size |
3/4 in | |
Standard |
Dimensions according to SAE J518 | |||
Fastening thread 1) |
M10 × 1,5; 17 mm deep | |||
State on delivery |
With protective cover (must be connected) | |||
A, B |
Working port |
Size |
M27 × 2; 16 mm deep | |
Standard |
DIN 3852 | |||
State on delivery |
With protective cover (must be connected) | |||
L |
Drain port |
Size |
3/4-16 UNF-2B; 11 mm deep | |
Standard 2) |
ISO 11926 | |||
State on delivery 3) |
With protective cover (observe installation instructions) | |||
L1 |
Drain port |
Size |
3/4-16 UNF-2B; 11 mm deep | |
Standard 2) |
ISO 11926 | |||
State on delivery 3) |
Plugged (observe installation instructions) |
1) | Thread according to DIN 13 |
2) | The spot face can be deeper than specified in the appropriate standard. |
3) | Unless otherwise specified. Other layouts on request. |
Sizes 37 and 45
Port plate 10

Port plate 16

Drive shaft

1) | Toothing data valid for basic number of teeth 48 |
Drive shaft

Ports
Size |
37 | 45 | ||
A, B |
Working port |
Size |
3/4 in | |
Standard |
Dimensions according to SAE J518 | |||
Fastening thread 1) |
M10 × 1,5; 17 mm deep | |||
State on delivery |
With protective cover (must be connected) | |||
A, B |
Working port |
Size |
M27 × 2; 16 mm deep | |
Standard |
DIN 3852 | |||
State on delivery |
With protective cover (must be connected) | |||
L |
Drain port |
Size |
7/8-14 UNF-2B; 13 mm deep | |
Standard 2) |
ISO 11926 | |||
State on delivery 3) |
With protective cover (observe installation instructions) | |||
L1 |
Drain port |
Size |
7/8-14 UNF-2B; 13 mm deep | |
Standard 2) |
ISO 11926 | |||
State on delivery 3) |
Plugged (observe installation instructions) |
1) | Thread according to DIN 13 |
2) | The spot face can be deeper than specified in the appropriate standard. |
3) | Unless otherwise specified. Other layouts on request. |
Sizes 58 and 63
Port plate 10

Port plate 16

Drive shaft

1) | Toothing data valid for basic number of teeth 48 |
Drive shaft

Ports
Size |
58 | 63 | ||
A, B |
Working port |
Size |
3/4 in | |
Standard |
Dimensions according to SAE J518 | |||
Fastening thread 1) |
M10 × 1,5; 17 mm deep | |||
State on delivery |
With protective cover (must be connected) | |||
A, B |
Working port |
Size |
M27 × 2; 16 mm deep | |
Standard |
DIN 3852 | |||
State on delivery |
With protective cover (must be connected) | |||
L |
Drain port |
Size |
7/8-14 UNF-2B; 13 mm deep | |
Standard 2) |
ISO 11926 | |||
State on delivery 3) |
With protective cover (observe installation instructions) | |||
L1 |
Drain port |
Size |
7/8-14 UNF-2B; 13 mm deep | |
Standard 2) |
ISO 11926 | |||
State on delivery 3) |
Plugged (observe installation instructions) |
1) | Thread according to DIN 13 |
2) | The spot face can be deeper than specified in the appropriate standard. |
3) | Unless otherwise specified. Other layouts on request. |
Flushing and boost pressure valve
The flushing and boost pressure valve is used in closed circuits for the removal of heat and to ensure a minimum boost pressure level.
Hydraulic fluid is directed from the respective low pressure side into the motor housing. This is then fed into the reservoir, together with the leakage. The removed hydraulic fluid must be replaced by cooled hydraulic fluid from the boost pump.
The valve is integrated into the port plate.
Cracking pressure of pressure retaining valve
(observe when setting the primary valve)
Fixed setting: 16 bar
Circuit diagram
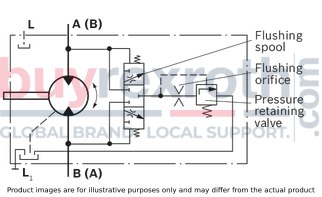
Flushing flow qv
Orifices can be used to set the flushing flows as required.
The specifications below are based on:
ΔpND = pND – pG = 20 bar and ν = 10 mm²/s
(pND = low pressure, pG = case pressure)
Standard flushing flow is 5.5 l/min with orifice ⌀1.6 mm. Other orifice diameters are available, please state in clear text when ordering.
Flushing flow qv |
Orifice-⌀ |
l/min |
mm |
3.5 |
1.2 |
5.5 |
1.6 |
9 |
2 |
Dimensions
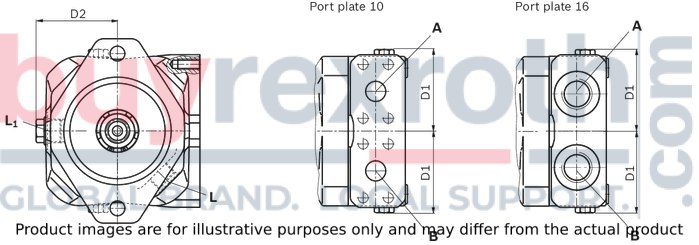
Size |
D1 |
D2 |
mm |
mm |
|
23, 28 | 72 | 72 |
37, 45 | 77 | 77 |
58, 63 | 77 | 82 |
Anti-cavitation valve
When stopping a system with a relatively large mass (i.e. fan drive) the anti-cavitation valve provides fluid to the motor inlet during the coasting time.
The valve is integrated into the port plate.
Please note:
Then direction of rotation must be fixed to clockwise or counter clockwise during project planning.
The outside dimensions of the motor with anti-cavitation valve are identical to the standard version.
(except A10FE, size 11 … 18, with 8-hole mounting flange)
Circuit diagram
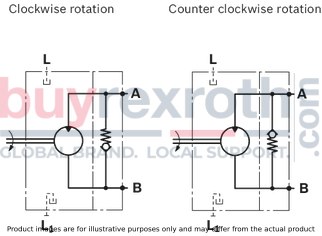
Speed sensor
The version A10F...D ("Prepared for speed sensor", i.e. without sensor) is equipped with an extra port D for installation of a suitable sensor and with a toothed ring on the rotary group. The toothing can be scanned by a sensor and a speed-proportional signal can thus be generated.
On deliveries the sensor port D is plugged with a pressure-resistant cover.
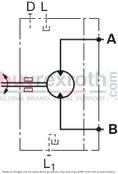
Dimensions
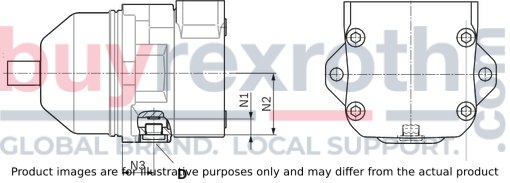
Motor |
Number of teeth |
N1 |
N2 |
N3 |
Thread |
Size |
mm |
mm |
mm |
D |
|
23, 28 | 48 | 20.7 | 65.7 | 27.7 | M18 × 1,5 |
37, 45 | 48 | 17 | 66 | 33.9 | |
58, 63 | 56 | 13.3 | 69 | 46.1 |
Installation instructions
General
During commissioning and operation, the axial piston unit must be filled with hydraulic fluid and air bled. This must also be observed following a relatively long standstill as the axial piston unit may drain back to the reservoir via the hydraulic lines. The case drain fluid in the housing must be directed to the reservoir via the highest available drain port (L, L1). If a shared drain line is used for several units, make sure that the respective case pressure is not exceeded. The shared drain line must be dimensioned to ensure that the maximum permissible case pressure of all connected units is not exceeded in any operating conditions, specifically on cold start. If this is not possible, separate reservoir lines must be laid as required. To achieve favorable noise values, all connecting lines should be decoupled by using elastic elements and above-reservoir installation is to be avoided. In all operating conditions, the drain line must flow into the reservoir below the minimum fluid level.Installation position
See the following examples 1 to 4.
Further installation positions are possible upon request. Recommended installation position: 1 and 2.
Below-tank installation (standard)
Below-tank installation is at hand if the axial piston unit is installed below the minimum liquid level outside the tank.

Installation position |
Air bleeding |
Filling |
1 |
‒ |
L1 |
2 |
‒ |
L |
Above-reservoir installation
Above-reservoir installation means that the axial piston unit is installed above the minimum fluid level of the reservoir.
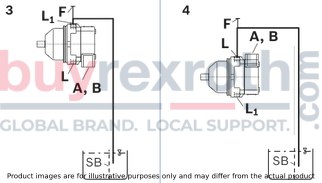
Installation position |
Air bleeding |
Filling |
3 |
F |
L1 (F) |
4 |
F |
L (F) |
Key |
|
F |
Filling / Air bleeding |
L, L2 |
Drain port |
SB |
Baffle (baffle plate) |
A, B |
Working port |
Note
Connection F is part of the external piping and must be provided on the customer side to simplify the filling and bleeding.
General project planning notes
The axial piston unit is designed to be used in open and closed circuits. The project planning, installation and commissioning of the axial piston unit require the involvement of qualified skilled personnel. Before using the axial piston unit, please read the corresponding instruction manual completely and thoroughly. If necessary, request it from Bosch Rexroth. Before finalizing your design, request a binding installation drawing. The specified datas and notes must be observed. Preservation: Our axial piston units are supplied as standard with preservative protection for a maximum of 12 months. If longer preservative protection is required (maximum 24 months), please specify this in plain text when placing your order. The preservation times are valid under optimal storage conditions. Details of these conditions can be found in the data sheet 90312 or the instruction manual. A pressure relief valve is to be provided in the hydraulic system. Observe the instructions in the instruction manual regarding tightening torques of connection threads and other threaded joints used. The notes in the instruction manual on tightening torques of the port threads and other screw joints must be observed. The ports and fastening threads are designed for the permissible maximum pressure pmax (see instruction manual). The machine or system manufacturer must ensure that the connecting elements and lines correspond to the specified operating conditions (pressure, flow, hydraulic fluid, temperature) with the necessary safety factors. The working ports and function ports are designated only to accommodate hydraulic lines.
During and shortly after operation, there is a risk of burns on the axial piston unit. Take appropriate safety measures (e.g. by wearing protective clothing).
Related Products
R902504144
$2,360.00 USD
R910918916
$6,520.00 USD
R902534861
$2,077.00 USD
R902505555
$2,521.00 USD
R902505296
$3,005.00 USD