***Disclaimer: The following summary contains information gathered from various sources such as product descriptions, technical specifications and catalogs. While efforts have been made to provide accurate details, inaccuracies may occur. It is advised to verify all information by contacting Bosch Rexroth directly.***
The Bosch Rexroth LFA32WEMA-7X/P12T12F12 (R900244087) is a sophisticated way cartridge valve designed for seamless integration into compact block systems. This valve enables precise control of hydraulic flow and pressure within a system, catering to various applications requiring pressure, directional, and throttle functions or combinations thereof. The LFA32WEMA-7X/P12T12F12 is engineered to optimize efficiency by allowing customization of flow rates according to the specific demands of each actuator path.
The construction of this valve includes a power section that fits into a standardized receiving hole in the control block and is sealed with a cover that also serves as the interface for pilot control valves. The versatility of this model is further enhanced by its ability to accommodate different pilot control valves, which dictate the overall functionality of the power section.
Additionally, this model features a control cover that houses control bores and may include options such as stroke limitation, hydraulically controlled directional seat valves, or shuttle valves depending on the required function. Electrical operation is also possible with the inclusion of directional spool or seat valves on the control cover. An installation kit comprising various components like a bushing, ring (up to NG), valve poppet (with or without damping nose), and closing spring completes the setup.
The performance of Bosch Rexroth's LFA32WEMA-7X/P12T12F12 way cartridge valve is pressure-dependent, with three distinct pressurized areas (A1, A2, A3) contributing to its functionality. These areas interact in such a way that their effective pressures determine the position and movement of the spool within the valve—either facilitating or blocking flow between ports A and B under different operating conditions.
Designed for standard series size and component series X1 and X2, this way cartridge valve can withstand maximum operating pressures up to several hundred bar while handling maximum flow rates up to several liters per minute. It offers customization through different area ratios, springs options for varying cracking pressures, ensuring adaptability for diverse hydraulic system requirements.
$638.00 USD
More are expected on January 23, 2026
Qty | Price | Savings |
---|---|---|
5-24 | $622.05 USD | $15.95 USD |
25+ | $606.10 USD | $31.90 USD |
Status: This product is temporarily out of stock.
Qty: Delivered as early as January 23, 2026 when ordered in
This product is eligible for factory repair.
2 area ratios 4 different springs 6 different cracking pressures

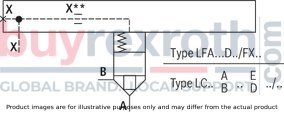
2-way cartridge valves are elements that have been designed for a compact block design. The power section with connections A and B is installed into the control block in a receiving hole standardized according to ISO 7368 and closed with a cover. In most cases, the cover is also the connection from the control side of the power section to the pilot control valves.
By control with respective pilot control valves, the power section can be applied for pressure, directional and throttle functions or a combination of these functions. Particularly efficient solutions are realized by adjustment of the size to various flows of the individual ways of an actuator. The application of power sections of elements for multiple functions is very cost-effective.
2-way cartridge valves generally consist of control cover (1) and installation kit (2). The control cover contains the control bores and optionally a stroke limitation function, a hydraulically controlled directional seat valve or a shuttle valve according to the required overall function. Additionally, electrically operated directional spool or seat valves can be installed at a control cover. The installation kit consists of a bushing (3), ring (4) (only up to NG32), valve poppet (5), optionally with damping nose (6) or without damping nose (7) as well as closing spring (8).
The function of 2-way cartridge valves is pressure-dependent. This way, three crucial pressurized areas A1, A2, A3 are realized for the function. The area at valve seat A1 is observed as 100 %. Depending on the version, the annulus area A2 realized by grading is 7 % or 50 % of area A1. The area ratio A1 : A2 is respectively either 14.3 : 1 or 2 : 1. The area A3 is identical to the sum of areas A1 + A2. Due to the different area ratios A1 : A2 and the resulting different annulus areas (A2), the area A3 is one time 107 % and another time 150 % of the area A1 at the seat, which is observed as 100 %.
In general, the following applies:
The areas A1 and A2 are effective in opening direction. The area A3 and the spring are effective in closing direction. The direction of action of the resulting force from the opening and closing forces determines the spool position of the 2-way cartridge valve.
The 2-way cartridge valves can be passed from A to B or from B to A. Pressurization of area A3 by pilot oil discharge from channel B or external pilot oil supply, channel A is blocked without leakage.
01 |
02 |
03 |
04 |
05 |
06 |
07 |
||
LFA |
WEMA |
– |
/ |
Type |
||
01 |
Control cover LFA |
LFA |
Size |
||
02 |
NG 16 |
16 |
NG 25 |
25 |
|
NG 32 |
32 |
|
NG 40 |
40 |
|
NG 50 |
50 |
|
NG 63 |
63 |
|
NG 80 |
80 |
|
NG 100 |
100 |
|
NG 125 |
125 |
|
Version |
||
03 |
Control cover version "WEMA": For set-up of a directional valve |
WEMA |
Component series |
||
04 |
Component series 70 ... 79 (70 ... 79: unchanged installation and connection dimensions) 1) |
7X |
Component series 60 … 69 (60 … 69: unchanged installation and connection dimensions) 2) |
6X |
|
Component series 20 ... 29 (20 ... 29: unchanged installation and connection dimensions) 3) |
2X |
|
Nozzle fitting |
||
05 |
Orifice in channel P 4) |
P.. |
06 |
Orifice in channel T 4) |
T.. |
07 |
Orifice in channel F 4) |
F.. |
1) Component series 7X for sizes 16...63 | |
2) Component series 6X for sizes 80 and 100 | |
3) Component series 2X for size 125 | |
4) This orifice is designed as screw-type orifice. If an orifice is to be installed, the respective code letter with the orifice Ø in 1/10 mm has to be entered in the type designation. | |
Example: P12 = Orifice with Ø1.2 mm in channel P. Additional orifice Ø see diagrams/characteristic curves. |
Orifice symbol |
Symbol in ordering code |
|||
A** |
![]() |
A** |
![]() |
This orifice is designed as screw-type orifice. If an orifice is to be installed, the respective code letter with the orifice Ø in 1/10 mm has to be entered in the type designation. Example: A12 = Orifice with Ø1.2 mm in channel A. |
Ø1,2 |
![]() |
![]() |
This orifice is designed as bore. No specifications are made in the type designation. (Orifice Ø in mm) |
|
Z12 |
![]() |
![]() |
This orifice is designed as screw-type orifice. This is a standard orifice. No specifications are made in the type designation. (Orifice Ø in 1/10 mm) |
Notices:
For ordering code of orifices, see "Accessories" Additional functions with special numbers see "Information".
general
Size |
16 | 25 | 32 | 40 | 50 | 63 | 80 | 100 | ||
Weight |
kg |
1.2 | 2.3 | 4 | 7.4 | 10.5 | 21 | 27 | 42 | |
Ambient temperature range |
NBR seals |
°C |
-30 … +60 | |||||||
FKM seals |
°C |
-20 … +60 | ||||||||
MTTFD values according to EN ISO 13849 1) |
Years |
150 |
1) | For further details, see data sheet 08012 |
hydraulic
Size |
16 | 25 | 32 | 40 | 50 | 63 | 80 | 100 | ||
Maximum operating pressure |
Port X 1) |
bar |
315 350 420 |
|||||||
Port Z1 1) |
bar |
315 350 420 |
||||||||
Port Z2 1) |
bar |
315 350 420 |
||||||||
Port Y |
depending on the maximum tank pressure of the attached directional valve | |||||||||
Maximum flow 2) |
l/min |
25000 | ||||||||
Hydraulic fluid |
see table | |||||||||
Hydraulic fluid temperature range |
NBR seals |
°C |
-30 … +80 | |||||||
FKM seals |
°C |
-20 … +80 | ||||||||
Viscosity range |
mm²/s |
2.8 … 500 | ||||||||
Maximum admissible degree of contamination of the hydraulic fluid, cleanliness class according to ISO 4406 (c) 3) |
Class 20/18/15 according to ISO 4406 (c) |
1) | dependent on the attached directional valve |
2) | NG-dependent; see characteristic curves |
3) | The cleanliness classes specified for the components must be adhered to in hydraulic systems. Effective filtration prevents faults and simultaneously increases the life cycle of the components. For the selection of the filters, see www.boschrexroth.com/filter. |
Hydraulic fluid |
Classification |
Suitable sealing materials |
Standards |
Data sheet |
|
Mineral oils |
HL, HLP, HLPD, HVLP, HVLPD |
NBR, FKM |
DIN 51524 |
90220 |
|
Bio-degradable 1) |
Insoluble in water |
HETG |
NBR, FKM |
ISO 15380 |
90221 |
HEES |
FKM |
||||
Soluble in water |
HEPG |
FKM |
ISO 15380 |
||
Flame-resistant |
Water-free |
HFDU (glycol base) |
FKM |
ISO 12922 |
90222 |
HFDU (ester base) 1) |
FKM |
||||
Containing water 1) |
HFC (Fuchs Hydrotherm 46M, Petrofer Ultra Safe 620) |
NBR |
ISO 12922 |
90223 |
|
Important information on hydraulic fluids: For more information and data on the use of other hydraulicfluids, please refer to the data sheets above or contact us. There may be limitations regarding the technical valve data (temperature, pressure range, life cycle, maintenance intervals, etc.). Flame-resistant - containing water: Life cycle as compared to operation with mineral oil HL, HLP 30 … 100%. Maximum hydraulic fluid temperature 60 °C Bio-degradable and flame-resistant – containing water: If this hydraulic fluid is used, small amounts of dissolved zinc may get into the hydraulic system. |
1) | Not recommended for corrosion-protected version "J3" (contains zinc) |
Hydraulic fluid |
Classification |
Suitable sealing materials |
Standards |
Data sheet |
|
Mineral oils |
HL, HLP, HLPD, HVLP, HVLPD |
NBR, FKM |
DIN 51524 |
90220 |
|
Bio-degradable 1) |
Insoluble in water |
HETG |
FKM |
ISO 15380 |
90221 |
HEES |
FKM |
||||
Soluble in water |
HEPG |
FKM |
ISO 15380 |
||
Flame-resistant |
Water-free |
HFDU (glycol base) |
FKM |
ISO 12922 |
90222 |
HFDU (ester base) 1) |
FKM |
||||
Containing water 1) |
HFC (Fuchs Hydrotherm 46M, Petrofer Ultra Safe 620) |
NBR |
ISO 12922 |
90223 |
|
Important information on hydraulic fluids: For further information and data on the use of other hydraulic fluids, please refer to the data sheets above or contact us. There may be limitations regarding the technical valve data (temperature, pressure range, life cycle, maintenance intervals, etc.).Flame-resistant – containing water: Life cycle as compared to operation with mineral oil HL, HLP 30 … 100% Maximum hydraulic fluid temperature 60 °CBio-degradable and flame-resistant: If this hydraulic fluid is used, small amounts of dissolved zinc may get into the hydraulic system. |
1) | Not recommended for corrosion-protected version "J3" (contains zinc) |
For applications outside these parameters, please consult us!
Orifices
Orifice Ø in mm |
Order numbers |
Material numbers |
||||||
M6 conical |
M8 x 1 conical |
G 1/8 conical |
G 1/4 conical |
G 3/8 conical |
G 1/2 conical |
G 1 conical |
||
– |
00 |
– |
– |
– |
– |
– |
– |
– |
0,5 |
05 |
R913040356 |
R913017600 |
R913030187 |
R913040456 |
– |
– |
– |
0,6 |
06 |
R913040358 |
R913017605 |
R913017606 |
R913020197 |
– |
– |
– |
0,7 |
07 |
R913040360 |
R913017609 |
R913046092 |
– |
– |
– |
– |
0,8 |
08 |
R913029447 |
R913017614 |
R913017616 |
R913017615 |
R913040481 |
R913040499 |
– |
1,0 |
10 |
R913019186 |
R913017621 |
R913024679 |
R913017622 |
R913040484 |
R913040500 |
– |
1,2 |
12 |
R913040362 |
R913017627 |
R913017629 |
R913017628 |
R913040486 |
R913040501 |
– |
1,5 |
15 |
R913028337 |
R913017637 |
R913017639 |
R913017638 |
R913040488 |
R913028317 |
– |
1,8 |
18 |
R913030186 |
R913017644 |
R913017646 |
R913017645 |
R913040489 |
R913045913 |
– |
2,0 |
20 |
R913029870 |
R913017651 |
R913040450 |
R913017652 |
R913028417 |
R913028336 |
– |
2,5 |
25 |
R913032543 |
R913035796 |
R913017656 |
R913019582 |
R913040493 |
R913040502 |
– |
3,0 |
30 |
R913040368 |
R913017661 |
R913017663 |
R913017662 |
R913018266 |
R913040503 |
R913040467 |
3,5 |
35 |
– |
R913017667 |
R913040452 |
R913040463 |
R913028318 |
R913019856 |
R913040469 |
4,0 |
40 |
– |
R913017670 |
R913027078 |
R913040464 |
R913018265 |
R913029168 |
R913040470 |
4,5 |
45 |
– |
R913046571 |
R913017671 |
R913040465 |
– |
R913040506 |
– |
5,0 |
50 |
– |
– |
R913017673 |
R913040468 |
R913023871 |
R913019857 |
R913040471 |
5,5 |
55 |
– |
– |
R913027077 |
– |
R913040495 |
R913053659 |
– |
6,0 |
60 |
– |
– |
– |
– |
R913023870 |
R913028418 |
R913020247 |
7,0 |
70 |
– |
– |
– |
R913040461 |
R913017675 |
R913040509 |
– |
7,5 |
75 |
– |
– |
– |
– |
R913023430 |
– |
R913018328 |
8,0 |
80 |
– |
– |
– |
– |
R913046570 |
R913040510 |
R913020246 |
closed |
99 |
R913019128 |
R913019129 |
R913019137 |
R913019136 |
R913019138 |
– |
R913019140 |
Other orifices upon request.
Plug screws |
|
Thread |
Tightening torque MA in Nm ±10 % |
G 1/8 |
12 |
G 1/4 |
30 |
G 3/8 |
55 |
G 1/2 |
80 |
G 3/4 |
135 |
G 1 |
225 |
G 1 1/4 |
360 |
LFA . WEMA… (NG16 … 32)

LFA . WEMA… (NG40 … 100)
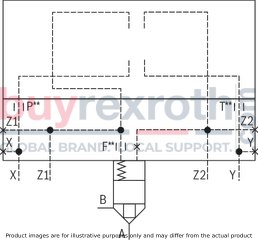
Control cover "WEMA" for set-up of a directional valve: NG16 ... 50
Dimensions in mm

1 |
Name plate at NG16, 25, 32 |
2 |
Name plate at NG40 and 50 |
3 |
Ports X, Y, Z1 and Z2 optionally as threaded ports at NG40 and 50 |
4 |
Plug screw M6 at type WEMB |
5 |
Plug screw M6 at type WEMA |
6 |
Directional spool valve type 4WE 6 D… (pilot control valve), separate order |
7 |
Directional seat valve type M-3SEW 6 … (pilot control valve), separate order |
8 |
Porting pattern according to ISO 4401-03-02-0-05 (mounting thread for version "/12" see data sheet 08936) |
NG |
D1 |
H1 |
H2 |
H3 |
H4 |
L1 |
L2 |
L3 |
L4 |
L5 |
L6 |
L7 |
mm |
mm |
mm |
mm |
mm |
mm |
mm |
mm |
mm |
mm |
mm |
||
16 | - | 65 |
- - |
15 | - | 65 | 80 | - | 17 | 47.5 | - | 4 |
25 | - | 40 |
- - |
24 | - | 85 | 85 | - | 27 | 64 | - | 4 |
32 | - | 50 |
- - |
28 | - | 100 | 100 | - | 34.5 | 71.5 | - | 4 |
40 | G1/2 | 60 |
30 - |
32 | 30 | 125 | 125 | 53 | 47 | 84 | 72 | 6 |
50 | G1/2 | 68 |
32 - |
34 | 32 | 140 | 140 | 60 | 54.5 | 91.5 | 80 | 6 |
Control cover "WEMA" for set-up of a directional valve: NG63
Dimensions in mm
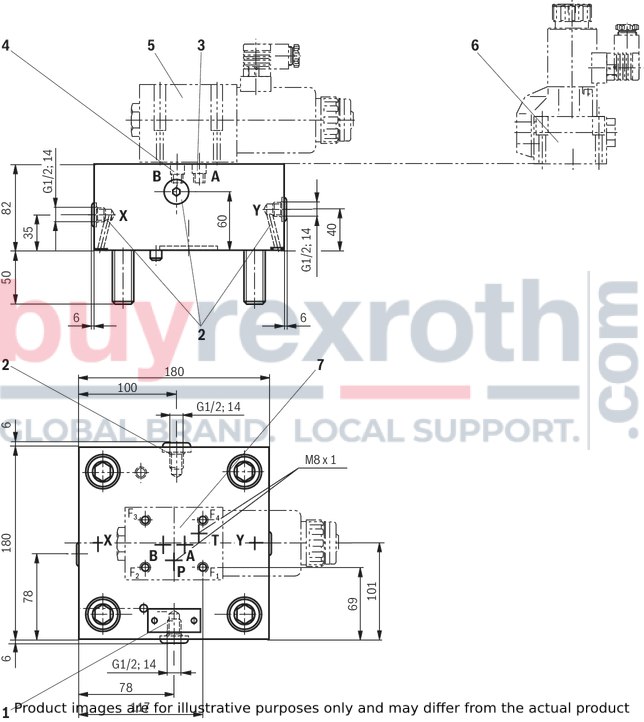
1 |
Name plate |
2 |
Ports X, Y, Z1 and Z2 optionally as threaded ports |
3 |
Plug screw M8 x 1 at type WEMB |
4 |
Plug screw M8 x 1 at type WEMA |
5 |
Directional spool valve type 4WE 10 D… (pilot control valve), separate order |
6 |
Directional seat valve type M-3SEW 10 … (pilot control valve), separate order |
7 |
Porting pattern according to ISO 4401-05-04-0-05 (mounting thread for version "/12" see data sheet 08936) |
Control cover "WEMA" for set-up of a directional valve: NG80 ... 100
Dimensions in mm

1 |
Name plate |
2 |
Ports X, Y, Z1 and Z2 optionally as threaded ports |
3 |
Plug screw M8 x 1 at type WEMB |
4 |
Plug screw M8 x 1 at type WEMA |
5 |
Directional spool valve type 4WE 10 D… (pilot control valve), separate order |
6 |
Directional seat valve type M-3SEW 10 … (pilot control valve), separate order |
7 |
Porting pattern according to ISO 4401-05-04-0-05 (mounting thread for version "/12" see data sheet 08936) |
NG |
D1 |
D2 |
H1 |
H2 |
H3 |
H4 |
L3 |
L4 |
L5 |
L6 |
mm |
mm |
mm |
mm |
mm |
mm |
mm |
mm |
mm |
||
80 | 250 | M8 x 1 | 80 | 42 | 45 | 26 | 10 | 10 | 16 | 27 |
100 | 300 | G1/8 | 100 | 55 | 52.5 | 35 | 13 | 9.5 | 27 | 26 |
1 |
Name plate |
2 |
Ports X, Y, Z1 and Z2 optionally as threaded ports |
3 |
Port F with check valve |
4 |
Directional spool valve type 4WEH 16 D... (Pilot control valve), separate order |
5 |
Directional seat valve type M-3SEW 16 ... (pilot control valve), separate order |
6 |
Porting pattern according to ISO 4401-07-07-0-05 (mounting thread for version "/12" see data sheet 08936) |
LFA control cover mounting screws |
||
Hexagon socket head cap screws ISO 4762 - 10.9-flZn/nc/480h/C 1) |
||
Size |
Quantity |
Tightening torque MA in Nm ±10 % |
16 |
4 |
30 |
25 |
4 |
100 |
32 |
4 |
240 |
40 |
4 |
480 |
50 |
4 |
480 |
63 |
4 |
1600 |
80 |
8 |
800 |
100 |
8 |
1600 |
125 |
9 |
3100 |
1) Hexagon socket head cap screws UNC, see data sheet 08936 |
Mounting screws included in the scope of delivery.
Notice:
The tightening torques stated are guidelines when using screws with the specified friction coefficients and when using a manual torque wrench (tolerance ± 10 %). The specified tightening torques were calculated with total friction coefficient μ = 0.09 … 0.14; adjust in case of modified surfaces. Supplied mounting screws are only suitable for direct assembly on a block. If an intermediate cover is used, mounting screws have to be designed accordingly longer (see dimensions).Installation bore and connection dimensions according to ISO 7368
Size 16 ... 63
Dimensions in mm

1 |
Bore for locating pin |
2 |
80 mm only at control cover for directional valve set-up NG16 (axis X–Y bore) |
Size 80 ... 100
Dimensions in mm

1 |
Bore for locating pin |
1 |
Bore for locating pin |
NG |
ØD1H7 |
ØD2 |
ØD3/(ØD3*) 2) |
ØD4H7 |
ØD5 3) |
ØD6 |
ØD7H13 |
H1 |
H2 |
H3 |
H4 |
H5 |
H6 |
H7 |
H8 |
H9 |
L1 |
L2 |
L3 |
L4 |
L5 |
W |
Ro 1) |
Ru 1) |
||||
mm |
mm |
mm |
mm |
mm |
mm |
mm |
mm |
mm |
mm |
mm |
mm |
mm |
mm |
mm |
mm |
mm |
mm |
mm |
mm |
mm |
mm |
mm |
mm |
mm |
mm |
mm |
||
16 | 32 | 16 |
16 25 |
25 | M8 | 4 | 4 | 42.5 | 56 | + 0.1 | 43 | + 0.2 | 20 | 11 | 2 | - | 20 | 2 | - | 0.5 |
65 80 |
46 - |
23 | 25 | 10.5 | 0.05 | 2 | 1 |
25 | 45 | 25 |
25 32 |
34 | M12 | 6 | 6 | 57 | 72 | + 0.1 | 58 | + 0.2 | 25 | 12 | 2.5 | - | 30 | 2.5 | - | 1 |
85 - |
58 - |
29 | 33 | 16 | 0.05 | 2 | 1 |
32 | 60 | 32 |
32 40 |
45 | M16 | 8 | 6 | 68.5 | 85 | + 0.1 | 70 | + 0.2 | 35 | 13 | 2.5 | - | 30 | 2.5 | - | 1.5 |
102 - |
70 - |
35 | 41 | 17 | 0.1 | 2 | 1 |
40 | 75 | 40 |
40 50 |
55 | M20 | 10 | 6 | 84.5 | 105 | + 0.1 | 87 | + 0.3 | 45 | 15 | 3 | - | 30 | 3 | - | 2.5 |
125 - |
85 - |
42.5 | 50 | 23 | 0.1 | 4 | 1 |
50 | 90 | 50 |
50 63 |
68 | M20 | 10 | 8 | 97.5 | 122 | + 0.1 | 100 | + 0.3 | 45 | 17 | 3 | - | 35 | 4 | - | 2.5 |
140 - |
100 - |
50 | 58 | 30 | 0.1 | 4 | 1 |
63 | 120 | 63 |
63 80 |
90 | M30 | 12 | 8 | 127 | 155 | + 0.1 | 130 | + 0.3 | 65 | 20 | 4 | - | 40 | 4 | - | 3 |
180 - |
125 - |
62.5 | 75 | 38 | 0.1 | 4 | 1 |
80 | 145 | 80 |
80 100 |
110 | M24 | 16 | 10 | 170.5 | 205 | + 0.1 | 175 | + 0.4 | 50 | 25 | 5 | - | 40 | 5 | - | 4.5 |
250 - |
200 - |
- | - | - | 0.1 | 4 | 1 |
100 | 180 | 100 |
100 125 |
135 | M30 | 20 | 10 | 205.5 | 245 | + 0.1 | 210 | + 0.4 | 63 | 29 | 5 | - | 50 | 5 | - | 4.5 |
300 - |
245 - |
- | - | - | 0.1 | 4 | 1 |
125 | 225 | 150 1) |
125 160 |
200 | - | - | - | 255 | 300 | + 0.15 | 257 | + 0.5 | - | 31 | 7 | ± 0.5 | 40 | 5.5 | ± 0.2 | 2 |
- - |
- - |
- | - | - | 0.1 | 4 | 1 |
1) | Maximum dimension |
2) | Due to the use of a bore with ØD3*, port B protrudes over the upper limit of the area intended in ISO 7368. This is, however, possible due to the sealing concept and reduces the pressure loss during flow through the valve. Thus, we recommend a bore with ØD3*. |
3) | Mounting thread for version "/12" see data sheet 08936 |
Notice:
The dimensions are nominal dimensions which are subject to tolerances.
Notices:
The specified tightening torques stated are guidelines when using screws with the specified friction coefficients and when using a manual torque wrench (tolerance ± 10%). The specified tightening torques were calculated with total friction coefficient μtotal = 0.09 ... 0.14; adjust in case of modified surfaces. Supplied mounting screws are only suitable for direct assembly on a block. If an intermediate cover is used, mounting screws have to be designed accordingly longer.Mounting screws (included in scope of delivery)
Hexagon socket head cap screws ISO 4762 - 10.9-flZn/nc/480h/C 1) |
||
Size |
Quantity |
Tightening torque MA in Nm ±10 % |
16 |
4 |
30 |
25 |
4 |
100 |
32 |
4 |
240 |
40 |
4 |
480 |
50 |
4 |
480 |
63 |
4 |
1600 |
80 |
8 |
800 |
100 |
8 |
1600 |
125 |
8 |
3100 |
160 |
12 |
5000 |
1) | Hexagon socket head cap screws UNC, see data sheet 08936 |
Additional functions with special numbers: Control cover (upon request)
Symbol |
Type |
Size |
Description / special characteristic |
![]() |
LFA . WEMA54-6X/… |
25 |
Cover for logic zero position open |
Additional functions with special numbers (upon request)
Orifice symbol
Orifice symbol |
Ordering code |
|||
A** |
![]() |
A** |
This orifice is designed as screw-type orifice. If an orifice is to be installed, the respective code letter with the orifice Ø in 1/10 mm has to be entered in the type designation. Example: A12 = Orifice with Ø1.2 mm in channel A. |
|
Ø1,2 |
![]() |
This orifice is designed as bore. No specifications are made in the type designation. (Orifice Ø in mm) |
||
Z12 |
![]() |
This orifice is designed as screw-type orifice. This is a standard orifice. No specifications are made in the type designation. (Orifice Ø in 1/10 mm) |
Orifice selection
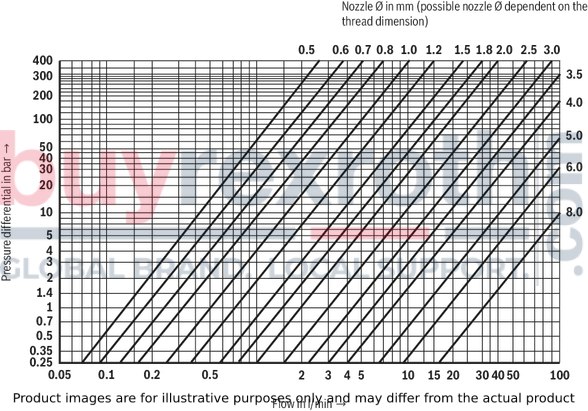
Related Products
R900720359
$1,456.00 USD
R978910384
$1,439.00 USD
R978858535
$827.00 USD
R900917736
$386.00 USD
R978895460
$536.00 USD