***Disclaimer: The following summary contains information gathered from various sources such as product descriptions, technical specifications and catalogs. While efforts have been made to provide accurate details, inaccuracies may occur. It is advised to verify all information by contacting Bosch Rexroth directly.***
The Bosch Rexroth 2WRC125K001-1X/E/V (R901420262) is a high-response stage valve designed for precise control of flow rate and direction in closed-loop control circuits. This valve features a robust design that includes a pilot control valve with a servo directional valve pilot, a dry torque motor, and a low friction jet flapper amplifier. It also incorporates mechanical feedback of the spool position to ensure accuracy and reliability. The main control spool is responsible for the flow control, while an inductive position transducer, attached to the spool of the third stage, provides precise position sensing.
The integrated control electronics within the WRCE model allow for real-time comparison of command and actual values, adjusting the pilot control valve solenoids accordingly to minimize system deviation. The main spool's stroke is controlled proportionally to the command value, though it's important to note that flow also depends on the valve pressure drop.
Valve features include bidirectional flow capability from A to B or B to A and a leak-free closure with smaller command values due to the closed loop control circuit's correction of spool position. The opening point is factory preset at 0.5 V but can be calibrated after replacing parts using an AF nut.
In terms of maintenance, only the filter element on the pilot control valve can be replaced without further adjustments needed except for zero calibration at the position controller. The spools are not pressure balanced; hence they require a recommended minimum control pressure derived from system pressure and additional reserves.
This Bosch Rexroth valve is particularly suited for applications requiring closed-loop or open-loop control of large flows such as forging manipulators, pressing cylinders, and die casting machines. It offers high response performance in block installation design and can be equipped with either external or integrated electronics depending on the specific device type. The 2WRC series operates under maximum pressures as defined by its component series designation.
$143,305.00 USD
More are expected on January 21, 2026
Status: This product is temporarily out of stock.
Qty: Delivered as early as January 21, 2026 when ordered in
This product is eligible for factory repair.
High-response valve in block installation design Control by directional servo valve Position sensing of the control spool via an inductive position transducer 2-way control element in seat design External or integrated control electronics, according to device type Closed-loop control or open-loop control of large flows:
Forging manipulators
Pressing cylinders
Die casting machines
The valve types 2WRC(E) are 3-stage high response valves.
They control the rate and direction of a flow and are primarily used in closed loop control circuits.
Design
They comprise of the following sub-assemblies:
A pilot control valve (1) as a 2-stage servo directional valve (pilot) With a dry torque motor Low friction jet / flapper amplifier and Mechanical feedback of the spool position A main control spool (2) for flow control An inductive position transducer (3) whose core (4) is attached to the spool (2) of the third stage And integrated control electronics (5) for 2WRCE orseparate electronics for the 2WRC version.Function
Within the integrated control electronics (OBE) the command and actual values are compared and the pilot control valve solenoids are controlled via a currrent proportional the closed loop control deviation.
The pilot control valve asumes a proportional control position and controls the flows into or from control chambers A (6) and B (7), that actuate the main spool (2) by means of the closed loop control valve until the system deviation is 0.
The stroke of the main spool is thus controlled in proportion to the command value. It must be noted herethat the flow also depends on the valve pressure drop.
Valve features
Flow can be passed through the valve from A to B or from B to A.
The poppet spool closes or opens with a command value of approx. 2 %. With smaller command values the valve‘s closed loop control circuit trys to correct the spool position and thereby presses the spool, with up to the full system pressure, onto its seat and closes the connection leak-free.
The stated switching times are only valid for the closed loop control range of the valve. With command value jumps from the seat to small opening values, additional delay times occur.
The 2 % opening point (= 0.2 V) is factory pre-set. When replacing the pilot control valve or control electronics the opening point can be calibrated by adjusting the position transducer (3) by using the 13A/F nut.
When carrying out an exchange no adjustments to the control electronics and pilot control valve (= closed loop controller, controller or control electronics), other than the zero calibration at the position controller may be carried out.
Only the filter element can be replaced on the pilot control valve (see data sheet „Servo directional valve“)
Due to the diameter differences in the seat area, the spools are not pressure balanced. To compensate for the force differences for spool „K001“ 6 %, and for spools „D001“ and „S001“ 22 % of the system pressure is required as the control pressure, and then by adding reserves for flow forces and dynamics, the recommended minimum control pressure can be obtained (see technical data).
Attention:
A loss of power at the pilot control valve results in the spool being in an undefined position (2).
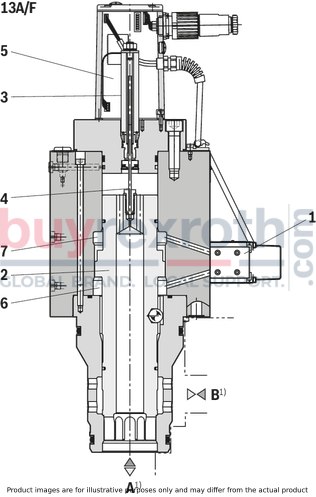
1) | Preferably, port B is to be connected to the actuator. |
01 |
02 |
03 |
04 |
05 |
06 |
07 |
08 |
09 |
10 |
|||
2 |
WRC |
‒ |
1X |
/ |
S |
/ |
* |
01 |
2/2 directional valve |
2 |
02 |
Electrically operated high-response valve for block installation |
WRC |
03 |
For external analog electronics |
no code |
With integrated electronics (OBE) |
E |
|
04 |
Size 63 |
63 |
Size 80 |
80 |
|
Size 100 |
100 |
|
Size 125 |
125 |
|
Size 160 |
160 |
|
Designation of the spool characteristic curve / 2-way function |
||
05 |
Spool with standard poppet seat (linear) |
K001 |
Spool with double cone (linear fine control range) |
D001 |
|
Spool with control window (progressive fine control range) |
S001 |
|
06 |
Component series 10 ... 19 (10 ... 19: unchanged installation and connection dimensions) |
1X |
Pilot control valve |
||
07 |
Directional servo valve |
S |
Power supply |
||
08 |
with .WRC |
|
External control electronics |
no code |
|
with .WRCE |
||
Supply voltage 24 VDC |
G24 |
|
Supply voltage ± 15 VDC |
G15 |
|
Seal material |
||
09 |
NBR seals, suitable for mineral oil HL and HLP according to DIN 51524 |
M |
FKM seals |
V |
|
10 |
Further details in the plain text |
* |
For applications outside these parameters, please consult us!
general
Type |
2WRC(E).../S | ||||||
Size |
63 | 80 | 100 | 125 | 160 | ||
Component series |
1X | ||||||
Installation position |
any, preferably horizontal | ||||||
Weight |
kg |
56 | 114 | 198 | 357 | 635 | |
Storage temperature range |
°C |
-20 … +80 | |||||
Ambient temperature range |
WRCE |
°C |
-20 … +60 | ||||
WRC |
°C |
-20 … +70 |
Hydraulic (measured with HLP32, ϑoil = 40 ±5 °C)
Type |
2WRC(E).../S | |||||||
Size |
63 | 80 | 100 | 125 | 160 | |||
Maximum operating pressure |
bar |
420 | ||||||
Maximum operating pressure |
Main stage |
Port A |
bar |
420 | ||||
Port B |
bar |
420 | ||||||
Maximum operating pressure |
Pilot control valve |
Port X |
bar |
315 | ||||
Port Y |
bar |
Pressure peaks < 100, static < 10 | ||||||
Nominal flow qVnom –10 % at Δp = 5 bar |
For spool „K001“ |
l/min |
2600 | 4100 | 6300 | 10100 | 17000 | |
For spool „D001“ |
l/min |
2300 | 3600 | 5800 | 9200 | 15000 | ||
For spool „S001“ |
l/min |
1800 | 3000 | 5200 | 7800 | 13300 | ||
Zero flow of the servo pilot stage in relationship to pressure in line X |
![]() |
![]() |
![]() |
![]() |
![]() |
|||
Control flow |
cm³ |
36.3 | 67.9 | 132.5 | 313.4 | 565.5 | ||
Min. control pressure in % of the system pressure |
For spool „K001“ |
% |
15 | |||||
For spools „D001“ and „S001“ |
% |
45 | ||||||
Maximum flow |
For spools „K001“ and „D001“ |
l/min |
5500 | 9000 | 14000 | 22000 | 35000 | |
For spool „S001“ |
l/min |
8000 | 13000 | 20000 | 30000 | 50000 | ||
Switching time |
at 200 bar |
Stroke 50% |
ms |
37 | 32 | 45 | 50 | 70 |
Stroke 100% |
ms |
70 | 50 | 75 | 90 | 120 | ||
at 315 bar |
Stroke 50% |
ms |
30 | 25 | 35 | 40 | 60 | |
Stroke 100% |
ms |
60 | 40 | 60 | 70 | 100 | ||
Pilot oil flow at X and Y with a stepped form of input signal from 0 to 100 % (315 bar) |
l/min |
42 | 135 | 165 | 320 | 430 | ||
Hydraulic fluid |
Mineral oil (HL, HLP) to DIN 51524, other pressure fluids on request | |||||||
Hydraulic fluid temperature range |
°C |
-20 … +80 | ||||||
preferably |
°C |
+40 … +50 | ||||||
Viscosity range |
mm²/s |
20 … 380 | ||||||
preferably |
mm²/s |
30 … 45 | ||||||
Maximum admissible degree of contamination of the hydraulic fluid, cleanliness class according to ISO 4406 (c) 1) |
Pilot control valve |
Class 18/16/13 according to ISO 4406 (c) | ||||||
Main valve |
Class 20/18/15 according to ISO 4406 (c) | |||||||
Hysteresis |
% |
≤ 0.5 | ||||||
Response sensitivity |
% |
≤ 0.2 | ||||||
Range of inversion |
% |
≤ 0.2 |
1) | The cleanliness classes specified for the components must be adhered to in hydraulic systems. Effective filtration prevents faults and simultaneously increases the life cycle of the components. For the selection of the filters, see www.boschrexroth.com/filter. |
electrical
Type |
2WRC(E).../S | ||
Voltage type |
Direct voltage | ||
Type of signal |
analog | ||
Valve protection to EN 60529 |
IP65 (with mating connector mounted and locked) | ||
Opening point calibration |
% |
≤ 1 | |
Zero shift upon change of |
Hydraulic fluid temperature |
%/10 K |
≤ 0.3 |
Return pressure in Y 0 to 10 % from px |
%/bar |
≤ 0.3 | |
Control pressure in X |
%/100 bar |
≤ 0.7 |
Control electronics |
2WRCE |
Integrated in the valve, see chapter Electrical connection, Block circuit diagram / pin allocation |
2WRC |
External control electronics, see data sheet 29931 |
Nominal command value range for 2WRCE:
0 ... +10 V ≙ 0 ... 100 %
In the command value range of 0 ... 0.2 V, the actual value remains constant at 0.2 V.
In case of slow command value modification from 0.2 V ... 10 V, the actual value follows the command value within ±0.1 V.
At a command value step to 10 V, the actual value can reach short-time values of up to approx. 10.5 V.
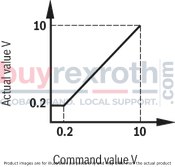
measured with HLP32, ϑOil = 40±5 °C
A Δp = 5 bar relates to a 100% flow value of the nominal flow of the associated table.
For other valve pressure differentials, the following applies:

Type 2 WRC.../...
(2/2-way function)

2-way function
Type 2WRC (Simplified: main stage with pilot control valve)
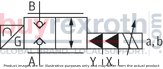
Type 2WRCE (Simplified: main stage with pilot control valve)
With integrated electronics (OBE)

Type 2WRCE (Detailed: main stage with pilot control valve)
With integrated electronics (OBE)

Component plug allocation with integrated electronics (OBE)
Component plug allocation |
Pin |
Allocation with a G24 supply voltage |
Allocation with a G15 supply voltage |
2WRCE |
2WRCE |
||
Power supply |
A |
+24 VDC |
+15 VDC |
B |
0 VDC |
-15 VDC |
|
C |
Enable (+24 V) 1) |
Reference to A, B |
|
Differential command value input |
D E |
0 ... +10 V |
0 ... +10 V |
Actual value |
F |
+0.2 ... +10 V Reference is pin B |
0 ... ±10 V Reference is pin C |
Earth |
PE |
connected to valve housing |
1) | Without enable = SO37 ( –37 attached to the type code) |
Mating connectors are included in the scope of delivery.
Do not connect PE if the valve has already been grounded via the system.
Supply voltage:
+24 VDC ±6 V; full bridge rectification with smoothing capacitor 2200 μF; Imax = 230 mA ±15 VDC ±0.45 V; stabilized and smoothened; Imax= 180 mACommand value and actual value have the same polarity
D positive against E → main spool in opening direction
Notice:
Electrical signals provided via control electronics (e.g. actual value) must not be used to switch off safety-relevant machine functions!
(See also the European standard "Safety requirements for fluid-powered systems and their components - Hydraulics", EN 982!)
Integrated electronics (OBE) type VT13037 for valve type 2WRCE
Block diagram / pin assignment
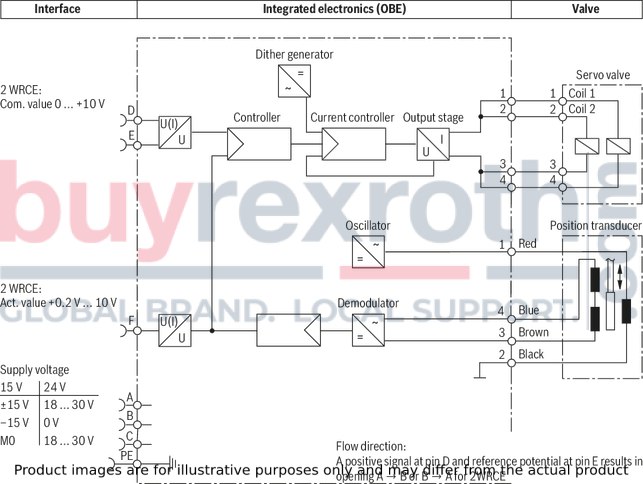
External control electronics
Pin alloction for 2WRC
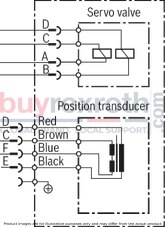
NG63
Dimensions in mm
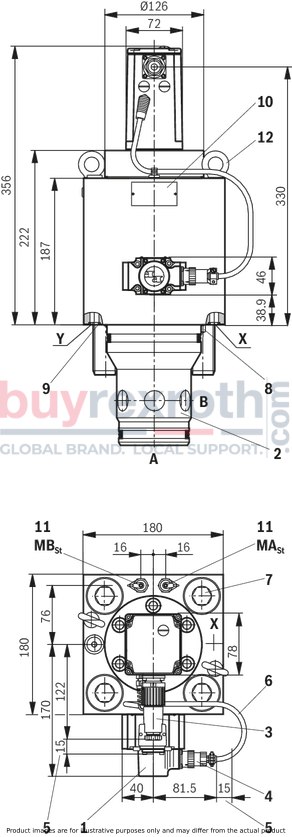
![]() |
Required surface quality of the valve contact surface |
1 |
Pilot control valve (directional servo valve NG6) |
2 |
Socket |
3 |
Mating connector (material no. R900021267) included in the scope of delivery |
4 |
Mating connector (material no. R900005414) included in the scope of delivery |
5 |
Space required to remove the mating connector |
6 |
Cabling (only with WRCE) |
7 |
Valve mounting screws (included in the scope of delivery): |
8 |
Locking pin for locating hole |
9 |
Identical seal rings for ports X and Y |
10 |
Name plate |
11 |
Measuring ports for control pressures, threaded coupling G1/4 |
12 |
Transport aid |
NG80
Dimensions in mm
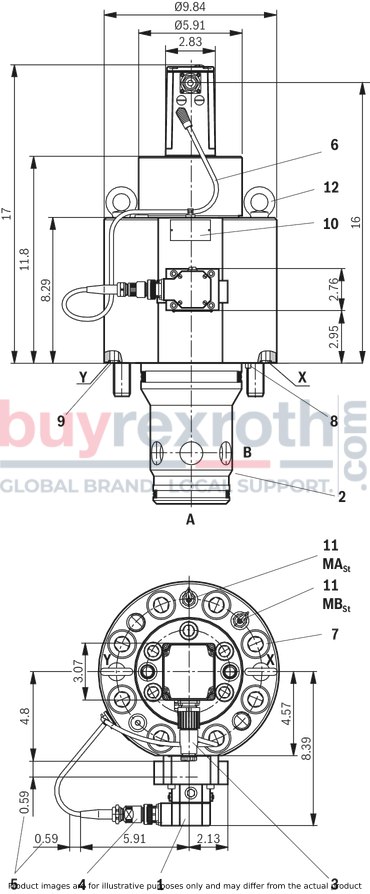
![]() |
Required surface quality of the valve contact surface |
1 |
Pilot control valve (directional servo valve NG10) |
2 |
Socket |
3 |
Mating connector (material no. R900021267) included in the scope of delivery |
4 |
Mating connector (material no. R900002460) included in the scope of delivery |
5 |
Space required to remove the mating connector |
6 |
Cabling (only with WRCE) |
7 |
Valve mounting screws (included in the scope of delivery): |
8 |
Locking pin for locating hole |
9 |
Identical seal rings for ports X and Y |
10 |
Name plate |
11 |
Measuring ports for control pressures, threaded coupling G1/4 |
12 |
Transport aid |
Size 100
Dimensions in mm
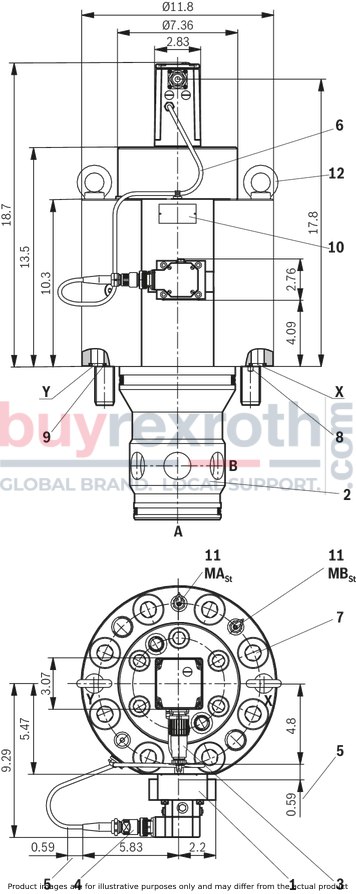
![]() |
Required surface quality of the valve contact surface |
1 |
Pilot control valve (directional servo valve NG10) |
2 |
Socket |
3 |
Mating connector (material no. R900021267) included in the scope of delivery |
4 |
Mating connector (material no. R900002460) included in the scope of delivery |
5 |
Space required to remove the mating connector |
6 |
Cabling (only with WRCE) |
7 |
Valve mounting screws (included in the scope of delivery): |
8 |
Locking pin for locating hole |
9 |
Identical seal rings for ports X and Y |
10 |
Name plate |
11 |
Measuring ports for control pressures, threaded coupling G1/4 |
12 |
Transport aid |
NG125
Nominal dimensions in mm
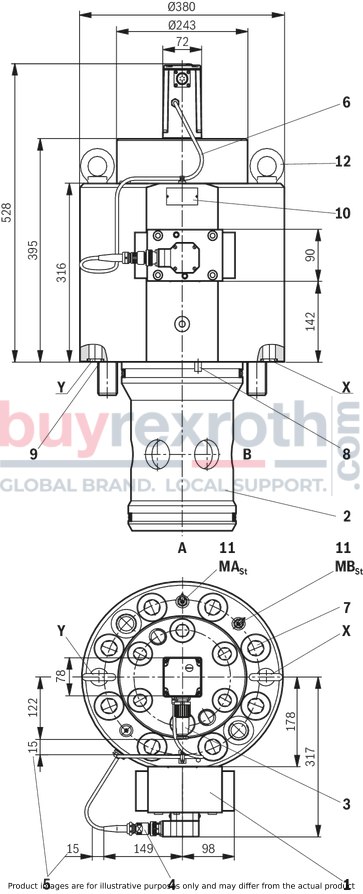
![]() |
Required surface quality of the valve contact surface |
1 |
Pilot control valve (directional servo valve NG16) |
2 |
Socket |
3 |
Mating connector (material no. R900021267) included in the scope of delivery |
4 |
Mating connector (material no. R900002460) included in the scope of delivery |
5 |
Space required to remove the mating connector |
6 |
Cabling (only with WRCE) |
7 |
Valve mounting screws (included in the scope of delivery): |
8 |
Locking pin for locating hole |
9 |
Identical seal rings for ports X and Y |
10 |
Name plate |
11 |
Measuring ports for control pressures, threaded coupling G1/4 |
12 |
Transport aid |
NG160
Nominal dimensions in mm
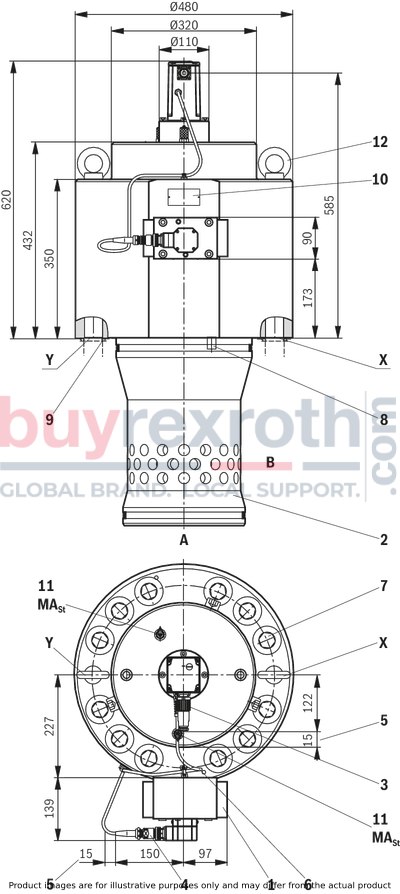
![]() |
Required surface quality of the valve contact surface |
1 |
Pilot control valve (directional servo valve NG16) |
2 |
Socket |
3 |
Mating connector (material no. R900021267) included in the scope of delivery |
4 |
Mating connector (material no. R900002460) included in the scope of delivery |
5 |
Space required to remove the mating connector |
6 |
Cabling (only with WRCE) |
7 |
Valve mounting screws (included in the scope of delivery): |
8 |
Locking pin for locating hole |
9 |
Identical seal rings for ports X and Y |
10 |
Name plate |
11 |
Measuring ports for control pressures, threaded coupling G1/4 |
12 |
Transport aid |
Installation dimensions to DIN ISO 7368 – except for NS125 and 160
NG63
Dimensions in mm

NG80 and 100
Dimensions in mm

NG125
Dimensions in mm

NG160
Dimensions in mm
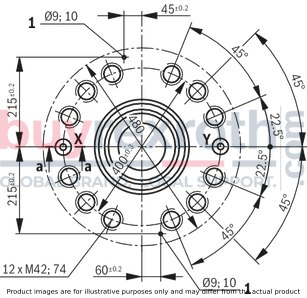
1 |
Locating hole |
Tolerances according to ISO 2768-mK |
Recess of connections X and Y in the block only for NG160
Dimensions in mm

Installation bore for type 2WRC... according to DIN ISO 7368
Dimensions in mm
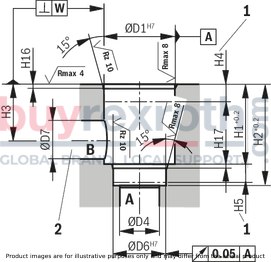
1 |
Depth of fit, minimum dimension |
2 |
The ports P, T and B can be positioned around the central axis of port A. Sufficient distance from the mounting and control bores is to be observed |
Tolerances according to ISO 2768-mK |
NG |
ØD1H7 |
ØD2H7 |
ØD3H7 |
ØD4 |
ØD5 |
ØD6H7 |
ØD7 |
D8 |
max. ØD9 |
ØD10 |
H1 |
H2 |
H3 |
H4 |
H5 |
H7 |
H8 |
H9 |
H10 |
H11 |
H12 |
H13 |
H16 |
H17 |
H18 |
L1 |
L2 |
L3 |
L4 |
L5 |
W |
mm |
mm |
mm |
mm |
mm |
mm |
mm |
mm |
mm |
mm |
mm |
mm |
mm |
mm |
mm |
mm |
mm |
mm |
mm |
mm |
mm |
mm |
mm |
mm |
mm |
mm |
mm |
mm |
mm |
mm |
||
63 | 120 | 116 | 90 | 63 | 48 | 90 | 63 | M30 | 12 | 8 | 130 | 155 | 95 | 40 | 20 | 85 | 165 | 195 | 57 | 137 | 33 | 28 | 4 | 4 | 65 | 180 | 125 | 62.5 | 75 | 38 | 0.05 |
80 | 145 | 140 | 110 | 80 | 60 | 110 | 80 | M24 | 16 | 10 | 175 | 205 | 130 | 40 | 25 | 125 | 215 | 245 | 90 | 180 | 60 | 25 | 5 | 5 | 50 | 250 | 200 | - | - | - | 0.1 |
100 | 180 | 174 | 135 | 100 | 75 | 135 | 100 | M30 | 20 | 10 | 210 | 245 | 155 | 50 | 29 | 155 | 270 | 305 | 112 | 225 | 75 | 32 | 5 | 5 | 63 | 300 | 245 | - | - | - | 0.2 |
125 | 225 | 220 | 200 | 150 | 95 | 200 | 125 | - | - | - | 257 | 300 | 192 | 40 | 31 | 195 | 335 | 380 | 140 | 280 | 93 | 37 | 5.5 | 7 | - | - | - | - | - | 0.2 | |
160 | 300 | 290 | 270 | 200 | 120 | 270 | 200 | - | - | - | 370 | 425 | 268 | 50 | 45 | 245 | 420 | 480 | 175 | 350 | 115 | 45 | 5.5 | 8 | - | - | - | - | - | 0.2 |
Mating connectors for valves with round connector, 6-pole + PE
7P Z31

Mating connectors for valves with round connector, 6-pole + PE
7P Z31
For valves with round connector according to EN 175201-804, 6-pole + PE as well as 6-pole, compatible with VG 95328Data sheet
Spare parts & repair
Related Products
R978918069
$2,787.00 USD
R900744846
$6,575.00 USD
R901396516
$5,288.00 USD
R900703117
$10,753.00 USD
R900954086
$2,855.00 USD