***Disclaimer: The following summary contains information gathered from various sources such as product descriptions, technical specifications and catalogs. While efforts have been made to provide accurate details, inaccuracies may occur. It is advised to verify all information by contacting Bosch Rexroth directly.***
The Bosch Rexroth PVV52-1X/162-055RA15DDMC (R901381680) is a high-performance hydraulic vane pump known for its durability and efficiency. This particular model features a constant displacement design, ensuring reliable and consistent operation. The PVV52-1X/162-055RA15DDMC is engineered with a double-eccentric stator ring that creates two pressure chambers opposite two suction chambers, significantly reducing the load on the shaft and only requiring it to transmit torque.
This pump is designed for easy maintenance; the pump insert – which includes the rotor, vane, stator ring, and control plates – can be quickly removed by simply taking off the cover without detaching the housing from the pump carrier. This feature greatly simplifies repair tasks and minimizes downtime.
For applications requiring higher flow rates, this model can be configured as a double pump by installing two pump kits on a single shaft. The oil inlet utilizes a joint suction port in the central housing, while each pump kit has its separate oil outlet – with the front kit's pressure port in the flange housing and the back kit's in the cover. It's important to note that only kits of different frame sizes can be combined for double pump applications.
The PVV52-1X/162-055RA15DDMC boasts several key features that enhance its performance: long bearing life due to hydraulic shaft relief, reduced wear because of hydraulically unloaded vanes, low operating noise levels, exchangeable pump cartridges for straightforward servicing, high efficiency, selectable pressure port positions, and compatibility with both clockwise or counterclockwise rotation. Drive shaft options are available in cylindrical or splined configurations to meet diverse system requirements. Additionally, this compact unit allows separate selection of pressure port positions for each kit when set up as a double pump.
$3,964.00 USD
More are expected on October 2, 2025
Qty | Price | Savings |
---|---|---|
5-24 | $3,864.90 USD | $99.10 USD |
25+ | $3,765.80 USD | $198.20 USD |
Status: This product is temporarily out of stock.
Qty: Delivered as early as October 2, 2025 when ordered in
This product is eligible for factory repair.
Fixed displacement Long bearing life through hydraulic relief of the shaft Low wear due to hydraulically unloaded vanes Low operating noise Easy to service due to exchangable pump cartridges Good efficiency Position of the pressure ports can be chosen Drive direction of rotation clockwise or counterclockwise Drive shaft optionally cylinderical or splined Double pump Very compact build Position of the pressure ports can be chosen separately
Hydraulic pumps of type PVV are vane pumps with constant displacement. The rotor (2) running in a stator ring (3) is located on the tooth profile of the drive shaft (1). The slots of the rotor accommodate the vanes (4) which are pressed against the internal surfaces of the stator ring by the centrifugal force upon rotation of the rotor. The displacer chambers are laterally sealed by the control plates (5). Due to the double-eccentric design of the stator ring, there are in each case two pressure chambers opposite of two suction chambers, which provides for hydraulic unloading of the shaft. So it only has to transmit the torque. The vanes are partially unloaded upon passage through the suction range. This unloading has a wear-reducing effect and ensures high efficiency. By simply removing the cover (6), the pump insert (consisting of rotor, vane, stator ring and control plates) can be removed without the need of removing the housing (7) from the pump carrier. This allows for fast maintenance and repair of the pump.
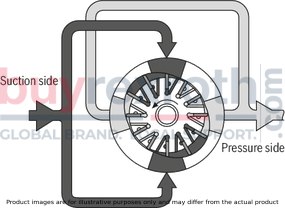
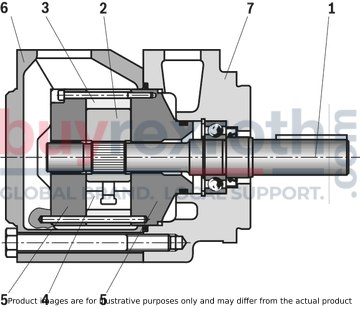
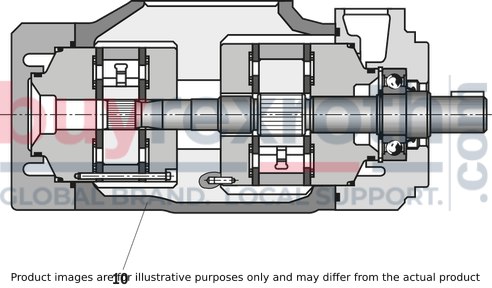
Double pumps are formed by installing two pump installation kits on one joint shaft. The oil inlet is realized by one joint suction port in the central housing (10). The oil outlet is realized separately by both pump installation kits. For the front pump installation kit, the pressure port is located in the flange housing, for the back pump installation kit in the cover. The larger pump installation kit is always located on the flange housing side. Pump installation kits of the same frame size cannot be used as double pumps.
01 |
02 |
03 |
04 |
05 |
06 |
07 |
08 |
09 |
10 |
11 |
12 |
13 |
||
PVV |
– |
1X |
/ |
15 |
* |
Pump type |
|||
01 |
Industrial version |
PVV |
|
Frame size |
|||
02 |
See selection table (e.g. single pump = 2, double pump = 52) |
||
Component series |
|||
03 |
Component series 10 ... 19 (10 ... 19: unchanged installation and connection dimensions) |
1X |
|
Displacement |
|||
04 |
See selection table (e.g. 55.2 cm3 = 055) |
||
Direction of rotation |
|||
05 |
clockwise |
R |
|
counterclockwise rotation |
L |
||
Shaft end version |
|||
06 |
Cylindrical drive shaft (standard) |
A 1) |
|
Cylindrical drive shaft (reinforced version) only BG2 to B54 |
B |
||
Multi-spline shaft |
J |
||
Line connection |
|||
07 |
Suction and pressure port: SAE flange connection, mounting thread UNC |
15 |
|
Position of the pressure connection at the flange (looking at the cover) |
|||
08 |
top (0° from the input) |
D |
|
right (90° to the right of the input) |
R |
||
counterclockwise (90° to the left of the input) |
L |
||
bottom (180° from the input) |
U |
||
Position of the pressure connection at the cover (looking at the cover), only with double pumps |
|||
09 |
BG21, 41, 42, 51, 52 |
top (45° from the input) |
D |
right (135° to the right of the input) |
R |
||
counterclockwise (45° to the left of the input) |
L |
||
bottom (135° to the left of the input) |
U |
||
BG54 |
top (0° from the input) |
D |
|
right (90° to the right of the input) |
R |
||
counterclockwise (90° to the left of the input) |
L |
||
bottom (180° from the input) |
U |
||
Seal material |
|||
10 |
NBR seals |
M |
|
FKM seals |
V |
||
Flange design |
|||
11 |
BG1, 2, 21 |
101-2 (SAE-B) |
B |
BG4, 5, 41, 42, 51, 52, 54 |
127-2 (SAE-C) |
C |
|
Through-drive |
|||
12 |
Non through-drive |
no code |
|
82-2, 16-4 (SAE-A, 9T) |
K01 |
||
101-2, 22-4 (SAE-B, 13T) |
K02 |
||
127-2, 32-4 (SAE-C, 14T) |
K07 |
||
Additional details |
|||
13 |
Further details in the plain text |
* |
1) | Not available for through-drive pumps |
Order example
Single pump: Industrial version (also as mobile version)
PVV 2-1X/055RA15DMB
Double pump: Mobile version (also as industrial version)
PVQ 52-1X/154-068RB15DDMC
Selection table
Single pump without through-drive |
|
Single pump with through-drive |
||||
Frame size |
Displacement Frame size |
Frame size |
Displacement |
|||
1 |
18 cm3 |
= 018 |
2 |
40,1 cm3 |
= 040 |
|
27,4 cm3 |
= 027 |
45,4 cm3 |
= 045 |
|||
36,4 cm3 |
= 036 |
55,2 cm3 |
= 055 |
|||
39,5 cm3 |
= 040 |
60,0 cm3 |
= 060 |
|||
45,9 cm3 |
= 046 |
67,5 cm3 |
= 068 |
|||
2 |
40,1 cm3 |
= 040 |
4 |
69,0 cm3 |
= 069 |
|
45,4 cm3 |
= 045 |
81,6 cm3 |
= 082 |
|||
55,2 cm3 |
= 055 |
97,7 cm3 |
= 098 |
|||
60,0 cm3 |
= 060 |
112,7 cm3 |
= 113 |
|||
67,5 cm3 |
= 068 |
121,6 cm3 |
= 122 |
|||
4 |
69,0 cm3 |
= 069 |
5 |
138,6 cm3 |
= 139 |
|
81,6 cm3 |
= 082 |
153,5 cm3 |
= 154 |
|||
97,7 cm3 |
= 098 |
162,2 cm3 |
= 162 |
|||
112,7 cm3 |
= 113 |
183,4 cm3 |
= 183 |
|||
121,6 cm3 |
= 122 |
193,4 cm3 |
= 193 |
|||
5 |
138,6 cm3 |
= 139 |
||||
153,5 cm3 |
= 154 |
|||||
162,2 cm3 |
= 162 |
|||||
183,4 cm3 |
= 183 |
|||||
193,4 cm3 |
= 193 |
Selection table
Double pump |
||||
Frame size |
flange-side |
cover-side |
||
Displacement |
||||
21 |
40,1 cm3 |
= 040 |
18 cm3 |
= 018 |
45,4 cm3 |
= 045 |
27,4 cm3 |
= 027 |
|
55,2 cm3 |
= 055 |
36,4 cm3 |
= 036 |
|
60,0 cm3 |
= 060 |
39,5 cm3 |
= 040 |
|
67,5 cm3 |
= 068 |
45,9 cm3 |
= 046 |
|
41 |
69,0 cm3 |
= 069 |
18 cm3 |
= 018 |
81,6 cm3 |
= 082 |
27,4 cm3 |
= 027 |
|
97,7 cm3 |
= 098 |
36,4 cm3 |
= 036 |
|
112,7 cm3 |
= 113 |
39,5 cm3 |
= 040 |
|
121,6 cm3 |
= 122 |
45,9 cm3 |
= 046 |
|
42 |
69,0 cm3 |
= 069 |
40,1 cm3 |
= 040 |
81,6 cm3 |
= 082 |
45,4 cm3 |
= 045 |
|
97,7 cm3 |
= 098 |
55,2 cm3 |
= 055 |
|
112,7 cm3 |
= 113 |
60,0 cm3 |
= 060 |
|
121,6 cm3 |
= 122 |
67,5 cm3 |
= 068 |
|
51 |
138,6 cm3 |
= 139 |
18 cm3 |
= 018 |
153,5 cm3 |
= 154 |
27,4 cm3 |
= 027 |
|
162,2 cm3 |
= 162 |
36,4 cm3 |
= 036 |
|
183,4 cm3 |
= 183 |
39,5 cm3 |
= 040 |
|
193,4 cm3 |
= 193 |
45,9 cm3 |
= 046 |
|
52 |
138,6 cm3 |
= 139 |
40,1 cm3 |
= 040 |
153,5 cm3 |
= 154 |
45,4 cm3 |
= 045 |
|
162,2 cm3 |
= 162 |
55,2 cm3 |
= 055 |
|
183,4 cm3 |
= 183 |
60,0 cm3 |
= 060 |
|
193,4 cm3 |
= 193 |
67,5 cm3 |
= 068 |
|
54 |
138,6 cm3 |
= 139 |
69,0 cm3 |
= 069 |
153,5 cm3 |
= 154 |
81,6 cm3 |
= 082 |
|
162,2 cm3 |
= 162 |
97,7 cm3 |
= 098 |
|
183,4 cm3 |
= 183 |
112,7 cm3 |
= 113 |
|
193,4 cm3 |
= 193 |
121,6 cm3 |
= 122 |
01 |
02 |
03 |
04 |
05 |
06 |
|||
INSTALLATION KIT |
PVV |
– |
1X |
/ |
Pump type |
|||
01 |
Industrial version |
PVV |
|
Frame size |
|||
02 |
Frame Size 1 |
1 |
|
Frame Size 2 |
2 |
||
Frame size 4 |
4 |
||
Frame size 5 |
5 |
||
Component series |
|||
03 |
Component series 10 ... 19 (10 ... 19: unchanged installation and connection dimensions) |
1X |
|
Size / displacement |
|||
04 |
Frame Size 1 |
18,0 cm3 |
018 |
27,4 cm3 |
027 |
||
45,4 cm3 |
036 |
||
39,5 cm3 |
040 |
||
45,9 cm3 |
046 |
||
Frame Size 2 |
40,1 cm3 |
040 |
|
45,4 cm3 |
045 |
||
55,2 cm3 |
055 |
||
60,0 cm3 |
060 |
||
67,5 cm3 |
068 |
||
Frame size 4 |
69,0 cm3 |
069 |
|
81,6 cm3 |
082 |
||
97,7 cm3 |
098 |
||
112,7 cm3 |
113 |
||
121,6 cm3 |
122 |
||
Frame size 5 |
138,6 cm3 |
139 |
|
153,5 cm3 |
154 |
||
162,2 cm3 |
162 |
||
183,4 cm3 |
183 |
||
193,4 cm3 |
193 |
||
Direction of rotation |
|||
05 |
clockwise |
R |
|
counterclockwise rotation |
L |
||
06 |
Installation kit for single pumps or flange-side for double pump |
no code |
|
Installation kit for cover-side installation in double pumps |
D |
Frame size |
|
1 | 2 | 4 | 5 | ||||||||||||||||||
Size |
|
18 | 27 | 27 | 27 | 46 | 40 | 45 | 55 | 60 | 68 | 69 | 82 | 98 | 113 | 122 | 139 | 154 | 162 | 183 | 193 | ||
Component series |
|
1X | |||||||||||||||||||||
Mounting type |
|
Flange mounting according to SAE J744 | |||||||||||||||||||||
Line connections |
|
SAE flange design (mounting thread: UNC) | |||||||||||||||||||||
Installation position |
|
Any, inlet port at top preferred | |||||||||||||||||||||
Shaft load |
|
Radial and axial forces cannot be transmitted | |||||||||||||||||||||
Direction of rotation |
|
Drive direction of rotation clockwise or counterclockwise | |||||||||||||||||||||
Drive |
|
Direct, coaxial drive | |||||||||||||||||||||
Drive speed 1) 2) |
n |
rpm |
600 ... 1,800 | ||||||||||||||||||||
Displacement |
Vg |
cm³ |
18 | 27.4 | 36.4 | 39.5 | 45.9 | 40.1 | 45.4 | 55.2 | 60 | 67.5 | 69 | 81.6 | 97.7 | 112.7 | 121.6 | 138.6 | 153.5 | 162.2 | 183.4 | 193.4 | |
Drive power 3) |
Pmax |
kW |
1.1 | 1.5 | 2.2 | 3 | 4 | 5.5 | 7.5 | 11 | |||||||||||||
Flow, max. 4) |
qV |
l/min |
26 | 39 | 53 | 59 | 70 | 59 | 66 | 80 | 89 | 100 | 101 | 120 | 141 | 167 | 177 | 203 | 223 | 234 | 267 | 285 | |
Operating pressure, absolute |
Inlet 5) 6) |
pmin-max |
bar |
0.83 ... 2.4 | |||||||||||||||||||
Outlet |
pmax |
bar |
210 | 160 | 140 | 175 | |||||||||||||||||
Pressure peak |
pmax |
|
At most 10 % over the max. permanent output pressure; not longer than 0.5 s | ||||||||||||||||||||
Mass 7) |
m |
kg |
12 | 14.8 | 23 | 34 |
1) | At 1 bar inlet pressure |
2) | If phosphoric acid esters (HFD-R) are used, adm. nmax = 1200 rpm |
3) | At Δp ≈ 0 bar, n ≈ 1450 rpm |
4) | at n = 1500 rpm, p = 0,7 bar, v = 25 mm2/s |
5) | Recommended: 1 ... 1,35 bar |
6) | If liquids containing water and phosphoric acid esters are used, at least 0,9 bar |
7) | Single pump without through-drive |
Hydraulic fluid
Permissible hydraulic fluid 1) |
Mineral oil (HLP) to DIN 51524-2 | |
Hydraulic fluid temperature range 2) |
°C |
-10 … +70 |
Viscosity range |
mm²/s |
13 … 860 |
Maximum admissible degree of contamination of the hydraulic fluid 3) |
Class 20/18/15 according to ISO 4406 (c) |
1) | For more information and data on the use of other hydraulic fluids please contact us. |
2) | Observe the admissible viscosity range! |
3) | The cleanliness classes specified for the components must be adhered to in hydraulic systems. Effective filtration prevents faults and simultaneously increases the life cycle of the components. For the selection of the filters, see www.boschrexroth.com/filter. |
For applications outside these parameters, please consult us!
The specified values for the max. drive speed apply to an absolute pressure at the input of 1 bar.
Depending on the absolute pressure at the input, the admissible max. speed must be corrected according to the following diagram.
BG1; BG2; BG4; BG21; BG41; BG42

BG5; BG51; BG52; BG54

Drive torque (measured with ν = 41 mm2/s; ϑ = 50 °C)




Sound pressure level measured in the low-noise chamber according to DIN 45635 part 26.
Distance microphone - pump = 1 m. ν = 41 mm2/s; n = 1500 and ϑ = 50 °C
BG1

BG2

BG4

BG5

The sound pressure levels for double pumps are - on the average - 1 to 3 db(A) higher than the values for single pumps.
Drive power (measured with ν = 41 mm2/s; ϑ = 50 °C)
n = 1500 min-1

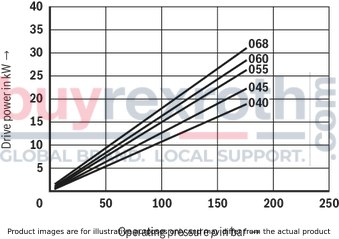


n = 1800 min-1




Displacement, speed-dependent (measured with ν = 41 mm2/s; ϑ = 50 °C; p = 7 bar)




Flow loss, pressure-dependent (measured with ν = 41 mm2/s; ϑ = 50 °C)

Double pump
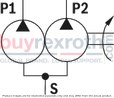
Single pump

Single pump PVV / PVQ, BG1
Dimensions in mm
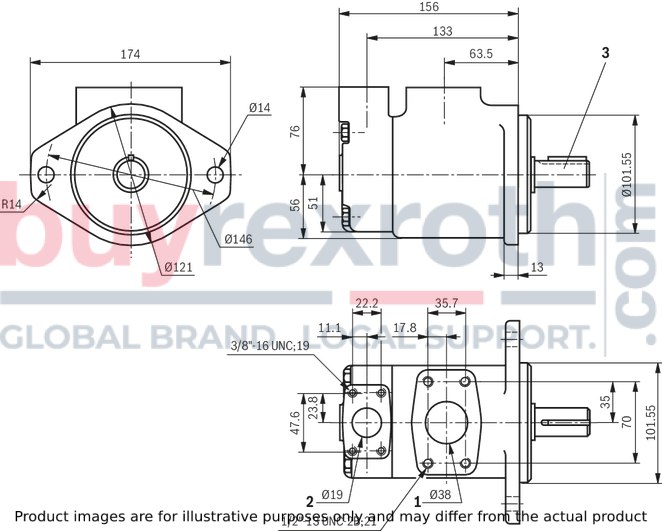
1 |
Suction port SAE 1 1/2“ |
2 |
Pressure connection SAE 3/4" |
3 |
cylindrical drive shaft |
Shaft end for BG1
Version "A"
Cylindrical drive shaft (standard)
4 fitting key ▢ 4.76 x 31.8
Admissible torque 250 Nm
Dimensions in mm

Version J
Multi-spline shaft SAE-B 7/8”
13 teeth 16/32DP
Tooth thickness t = 2.261
Admissible torque 316 Nm
Dimensions in mm

Single pump PVV / PVQ, BG2; 4; 5
Dimensions in mm

1 |
Suction port |
2 |
Pressure port |
3 |
Cylindrical drive shaft (nominal dimensions of the drive shafts see double pump PVV / PVQ, BG54) |
BG |
Suction port |
||||||
ØD5 |
D8-2B |
B3 |
L6 |
L4 |
H1 |
||
2 |
SAE 1 1/2" |
38 mm |
1/2"-13UNC; 22 mm |
69,9 mm |
35,7 mm |
120,6 mm |
76,2 mm |
4 |
SAE 2" |
50,8 mm |
1/2"-13UNC; 23,8 mm |
77,7 mm |
42,8 mm |
125,5 mm |
82,6 mm |
5 |
SAE 3" |
76,2 mm |
5/8"-13UNC; 28,6 mm |
106,3 mm |
61,9 mm |
153,2 mm |
93,6 mm |
BG |
Pressure port |
|||||
ØD6 |
D7-2B |
B4 |
L7 |
L3 |
||
2 |
SAE 1" |
25,4 mm |
3/8"-16UNC; 19 mm |
52,4 mm |
26,2 mm |
38,1 mm |
4 |
SAE 1 1/4" |
31,8 mm |
7/16"-14UNC; 22 mm |
58,7 mm |
30,1 mm |
38,1 mm |
5 |
SAE 1 1/2" |
38,1 mm |
1/2"-13UNC; 23,8 mm |
69,9 mm |
35,7 mm |
42,9 mm |
BG |
Mounting flange |
B2 |
L1 |
H2 |
|||||||
B1 |
ØD1 |
ØD2 |
ØD3 |
ØD4-0,05 mm |
L2 |
L5 |
|||||
2 |
SAE-B |
174 mm |
14 mm |
146 mm |
121 mm |
101,6 mm |
9,5 mm |
13 mm |
117 mm |
163 mm |
64 mm |
4 |
SAE-C |
212 mm |
17,5 mm |
181 mm |
148 mm |
127 mm |
9,5 mm |
16 mm |
140 mm |
186 mm |
70 mm |
5 |
SAE-C |
212 mm |
17,5 mm |
181 mm |
148 mm |
127 mm |
12,7 mm |
16 mm |
159 mm |
216 mm |
83 mm |
PVV / PVQ 2...K.. - with through-drive
Dimensions in mm

PVV / PVQ 4...K.. - with through-drive
Dimensions in mm

PVV, PVQ 5...K.. - with through-drive
Dimensions in mm

Double pump PVV / PVQ, BG21; 41; 42; 51; 52
Dimensions in mm
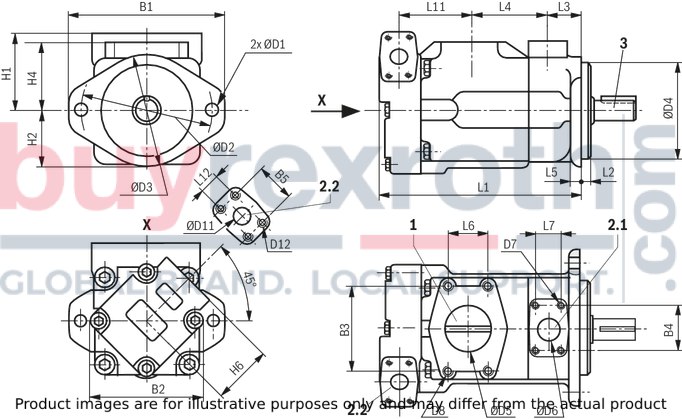
1 |
Suction port |
2.1 |
Pressure connection, flange-side |
2.2 |
Pressure connection, cover-side |
3 |
Cylindrical drive shaft (nominal dimensions of the shaft ends see shaft end for BG2 to 54) |
BG |
Mounting flange |
|||||||
B1 |
ØD1 |
ØD2 |
ØD3 |
ØD4-0,05 mm |
L2 |
L5 |
||
21 |
SAE-B |
174 mm |
14 mm |
146 mm |
121 mm |
101,6 mm |
9,5 mm |
13 mm |
41; 42 |
SAE-C |
212 mm |
17,5 mm |
181 mm |
148 mm |
127 mm |
9,5 mm |
16 mm |
51; 52 |
SAE-C |
212 mm |
17,5 mm |
181 mm |
148 mm |
127 mm |
12,7 mm |
16 mm |
BG |
Suction port |
||||||
ØD5 |
D8-2B |
B3 |
L6 |
L4 |
H1 |
||
21 |
SAE 1 1/2" |
63,5 mm |
1/2"-13UNC; 23,8 mm |
88,5 mm |
50,8 mm |
101,6 mm |
84,1 mm |
41; 42 |
SAE 3" |
76,2 mm |
5/8"-11UNC; 28,6 mm |
106,3 mm |
61,9 mm |
114,4 mm |
88,9 mm |
51; 52 |
SAE 3 1/2" |
88,9 mm |
5/8"-11UNC; 31,8 mm |
120,7 mm |
69,9 mm |
119,3 mm |
102,4 mm |
BG |
Pressure connection, flange-side |
||||||
ØD6 |
D7-2B |
B4 |
L7 |
L3 |
H4 |
||
21 |
SAE 1" |
25,4 mm |
3/8"- 16UNC; 19,1 mm |
52,4 mm |
26,2 mm |
38,1 mm |
76,2 mm |
41; 42 |
SAE 1 1/4" |
31,8 mm |
7/16"- 14UNC; 21,6 mm |
58,7 mm |
30,1 mm |
38,1 mm |
82,6 mm |
51; 52 |
SAE 1 1/2" |
38,1 mm |
1/2"- 13UNC; 23,8 mm |
69,9 mm |
35,7 mm |
42,9 mm |
93,6 mm |
BG |
Pressure connection, cover-side |
|||||||||
ØD11 |
D12-2B |
B5 |
L12 |
L11 |
H6 |
B2 |
L1 |
H2 |
||
21 |
SAE 3/4" |
19,1 mm |
3/8"-16UNC; 19,1 mm |
47,6 mm |
22,2 mm |
88 mm |
76,2 mm |
132 mm |
252 mm |
64 mm |
41 |
SAE 3/4" |
19,1 mm |
3/8"-16UNC; 19,1 mm |
47,6 mm |
22,2 mm |
99,5 mm |
74,7 mm |
140 mm |
275 mm |
70 mm |
42 |
SAE 1" |
25,4 mm |
3/8"-16UNC; 19,1 mm |
52,4 mm |
26,2 mm |
109,5 mm |
76,2 mm |
143 mm |
288 mm |
74 mm |
51 |
SAE 3/4" |
19,1 mm |
3/8"-16UNC; 19,1 mm |
47,6 mm |
22,2 mm |
119,5 mm |
74,7 mm |
162 mm |
306 mm |
85 mm |
52 |
SAE 1" |
25,4 mm |
3/8"-16UNC; 19,1 mm |
52,4 mm |
26,2 mm |
135,8 mm |
76,2 mm |
162 mm |
324 mm |
85 mm |
Double pump PVV / PVQ, BG54
Dimensions in mm
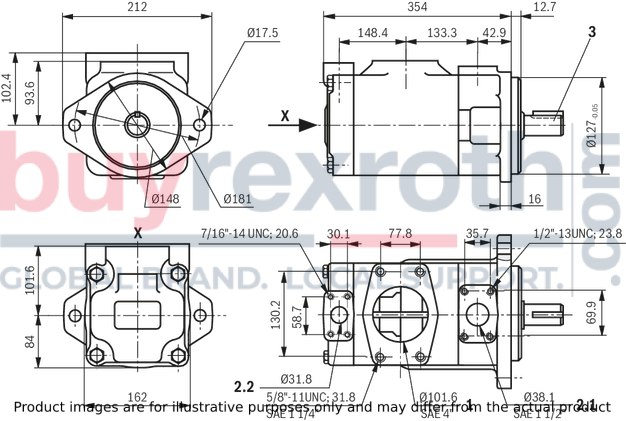
1 |
Suction port |
2.1 |
Pressure connection, flange-side |
2.2 |
Pressure connection, cover-side |
3 |
Cylindrical drive shaft (nominal dimensions of the shaft ends see tables) |
4 |
Fitting key (dimensions see table) |
Shaft end for BG2 to 54
Dimensions in mm

Shaft design A |
||||||
BG |
L8 |
L9 |
H3 |
ØD9 |
Fitting key |
Tmax in Nm |
2; 21 |
46,8 mm |
59 mm |
24,5-0,2 mm |
22,23-0,3 mm |
▢ 4,76 mm x 31,8 mm |
250 |
4; 41; 42 |
61,9 mm |
73,2 mm |
35,2-0,3 mm |
31,75-0,3 mm |
▢ 7,9 mm x 38,1 mm |
407 |
5; 51; 52; 54 |
47,8 mm |
62 mm |
35,2-0,3 mm |
31,75-0,3 mm |
▢ 7,9 mm x 28,4 mm |
610 |
Shaft design B |
||||||
BG |
L8 |
L9 |
H3 |
ØD9 |
Fitting key |
Tmax in Nm |
2; 21 |
64 mm |
78 mm |
28,3-0,2 mm |
25,37-0,02 mm |
▢ 6,36 mm x 50,8 mm |
400 |
4; 41; 42 |
74,6 mm |
86 mm |
38,6-0,3 mm |
34,9-0,03 mm |
▢ 7,9 mm x 54,6 mm |
600 |
5; 51; 52; 54 |
73 mm |
88 mm |
42,37-0,23 mm |
38,07-0,02 mm |
▢ 9,5 mm x 54,6 mm |
810 |
Shaft design J |
||||||
BG |
L8 |
L9 |
L10 |
ØD10 |
Tmax in Nm |
Gearing data |
2; 21 |
33,3 mm |
41 mm |
4 mm |
27,8 mm |
316 |
SAE-B 7/8", 13 teeth, 16/32 DP |
4; 41; 42 |
42,1 mm |
56 mm |
3,04 mm |
35,05 mm |
580 |
SAE-C 1/4", 14 teeth, 12/24 DP |
5; 51; 52; 54 |
46,6 mm |
56 mm |
9,7 mm |
41,28 mm |
818 |
SAE-C 1/4", 14 teeth, 12/24 DP |
Maximum admissible through-drive torques in Nm |
|||
BG |
Through-drive |
||
K01 (SAE-A, 9T) |
K02 (SAE-B, 13T) |
K07 (SAE-C, 14T) |
|
2 |
131 |
316 |
- |
4 |
131 |
316 |
437 |
5 |
131 |
384 |
702 |
SAE connection flanges
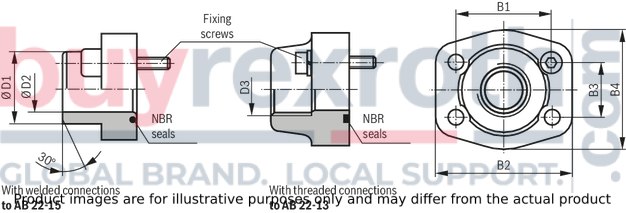
Suction port |
Pressure connection for PVV / PVQ 1) |
NG |
Seal material |
Material number for flange with |
B1 |
B2 |
B3 |
B4 |
ØD1 |
ØD2 |
D3 |
Mounting screws |
|
Welded connection |
Threaded connection |
||||||||||||
1; 21; 41; 51 |
3/4“ |
NBR |
R900211169 |
R900063050 |
47,6 mm |
65 mm |
22,2 mm |
52 mm |
25 mm |
19 mm |
G3/4 |
3/8"-16UNC |
|
2; 21; 42; 52 |
1“ |
NBR |
R900211170 |
R900211175 |
52,4 mm |
70 mm |
26,2 mm |
59 mm |
30 mm |
22 mm |
G1 |
3/8"-16UNC |
|
4; 41; 42; 54 |
1 1/4" |
NBR |
R900211363 |
R900211172 |
58,7 mm |
79 mm |
30,2 mm |
68 mm |
38 mm |
28 mm |
G1 1/4 |
7/16"-14UNC |
|
5; 51; 52; 54 |
1 1/2" |
NBR |
R900211168 |
R900211171 |
69,9 mm |
95 mm |
35,7 mm |
76 mm |
38 mm |
30 mm |
G1 1/2 |
1/2"-13UNC |
|
1; 2 |
1 1/2" |
NBR |
R900211165 |
R900211171 |
69,9 mm |
95 mm |
35,7 mm |
76 mm |
48 mm |
39 mm |
G1 1/2 |
1/2"-13UNC |
|
4 |
2" |
NBR |
R900211434 |
R900211173 |
77,8 mm |
102 mm |
42,9 mm |
90 mm |
60 mm |
49 mm |
G2 |
1/2"-13UNC |
|
21 |
2 1/2" |
NBR |
R900063063 |
R900211174 |
88,9 mm |
114 mm |
50,8 mm |
104 mm |
76 mm |
62 mm |
G2 1/2 |
1/2"-13UNC |
|
5; 41; 42 |
3" |
NBR |
R900211362 |
‒ |
106,3 mm |
135 mm |
61,9 mm |
131 mm |
76 mm |
70 mm |
‒ |
5/8"-11UNC |
|
51; 52 |
3 1/2" |
NBR |
R900211166 |
‒ |
130,7 mm |
152 mm |
69,9 mm |
140 mm |
89 mm |
82 mm |
‒ |
5/8"-11UNC |
|
54 |
4" |
NBR |
R900211167 |
‒ |
130,2 mm |
162 mm |
77,8 mm |
152 mm |
114 mm |
107 mm |
‒ |
5/8"-11UNC |
1) | Bold figure specifies the stage for which the flange (with double pumps) is intended. |
The material numbers comprise the flange, the O-ring and the mounting screws.
Pipe thread "G" according to ISO 228/1
Comprehensive information and suggestions are contained in the Hydraulics Trainer, volume 3, RE 00281, “Project planning information and design of hydraulic systems".
When using vane pumps, we recommend particularly observing the information specified below.
Technical data
All specified Technical data depend on production tolerances and are valid at certain boundary conditions.
Please note that consequently, fluctuations are possible and that with certain boundary conditions (e.g. viscosity), the Technical data may also change.
Characteristic curves
When designing the drive motor, please observe the maximum application parameters possible shown by the presented characteristic curves.
Noise
The values for sound pressure level shown on page 8 have been measured based on DIN 45635, sheet 26. That means that only the sound emission of the pump is shown.
Environmental influences (place of installation, piping, etc.) have not been considered.
These values are in each case only valid for one pump.
With unfavorable influences at the place of installation of the power unit, the sound pressure level may, however, still be 5 to 10 db(A) higher than the values of the pump itself.
Drive
Electric motor + pump carrier + coupling + pump
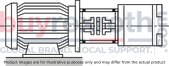
Attention!
no radial and axial forces on the pump drive shaft admissible! Motor and pump must be exactly aligned! use a torsionally flexible couplingFluid tank
Adjust useful volume of the tank to the operating conditions.Attention!
The admissible fluid temperature must not be exceeded use coolers, if necessary!Lines and connections
Cut with an inclination of 45° Remove the protective plug at the pump We recommend using seamless precision steel pipes according to DIN 2391 and releasable pipe connections. Select the inner width of the pipes according to the connections Pipelines and fittings must be carefully cleaned before assembly. – min. distance 120 mm to the tank bottom Dirt deposits are not sucked in or raised min. 50 mm immersion depth, also with lowest fluid level admissible Foam formation is avoided Leakage and return fluid must not be directly sucked in again under any circumstances! Liquid temperature remains low For the inlet pressure refer to the Technical dataRecommendation for pipe-laying

Filter
Use return flow or pressure filter if possible. (Suction filters only in connection with underpressure switch/clogging indicator).Hydraulic fluid
Please observe our provisions according to catalog sheet RE 07075. We recommend brand hydraulic fluids. Different hydraulic fluid types must not be mixed as this might result in degradation and deterioration of the lubricity. According to the operating conditions, the liquid must be renewed at certain time intervals. In this connection, it is also necessary to clean the fluid tank from residues.admissible installation positions
horizontal position preferredB3

B5
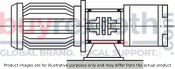
V1
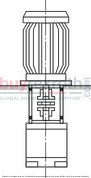
Commissioning
Check whether the system has been assembled carefully and properly. Only fill in hydraulic fluid through filters with the required minimum retention rate. Observe the arrow indicating the direction of rotation. Start up the pump without load and allow to pump at zero pressure for some seconds in order to allow for sufficient lubrication. Do not operate the pump without oil under any circumstances. If the pump does not deliver medium without bubbles after approx. 20 seconds, the system must be checked once again. After the operating values have been reached, check the pipe connections for leak-tightness. Check the operating temperature.Bleeding
Before the initial commissioning, we recommend filling the housing and the suction line of the pump with oil. This increases the operational safety and prevents wear in case of unfavorable installation conditions. During the initial commissioning, the foaming oil has to be discharged in circulation at zero pressure by carefully opening the pressure flange (provide splashguard, if necessary). Only re-tighten the fitting applying the specified torque if bubble-free oil exits.General information
The pumps delivered by us have been checked for function and performance. Changes of any kind at the pump are not admissible; otherwise, the warranty will become void! Repair works may only be carried out by the manufacturer or their authorized dealers and agencies. No warranty is accepted for independently performed repairs.Notice!
Assembly, maintenance and repair of the pump may only be carried out by authorized, trained and instructed personnel. Pump may only be operated with the admissible data (see Technical data)! The pump may only be operated if it is in an unobjectionable condition. For all works at the pump, depressurize the system! Unauthorized modifications or changes which affect the safety and function are not admissible! Apply protective devices (e. g. coupling guard) and/or do not remove existing protective devices! Always ensure tight seat of all mounting screws! (Observe the specified tightening torque) The generally valid safety and accident prevention regulations must be imperatively complied with!For limitation of the operating pressure or (and) for the solenoid-actuated unloading of the operating pressure, we recommend our pump safety blocks according to RE 25880 and RE 25890.
Related Products
R901424485
$1,772.00 USD
R901348957
$4,427.00 USD
R900948951
$2,858.00 USD
R901100678
$2,858.00 USD
R901089806
$4,167.00 USD