PUMP CONTROL SYSTEM SYDFEE-3X/071R-VRB22U00-0479-A2A0FLX
Manufacturer: Bosch Rexroth
Material #: R901135309
Model : SYDFEE-3X/071R-VRB22U00-0479-A2A0FLX
***Disclaimer: The following summary contains information gathered from various sources such as product descriptions, technical specifications and catalogs. While efforts have been made to provide accurate details, inaccuracies may occur. It is advised to verify all information by contacting Bosch Rexroth directly.***
The Bosch Rexroth SYDFEE-3X/071R-VRB22U00-0479-A2A0FLX (R901135309) is an advanced hydraulic pump system designed for precision control and efficiency in demanding applications. This pump system features a robust axial piston variable displacement pump (AVSO) with a frame size of X, capable of handling a nominal pressure of up to bar. It is engineered for maximum operating pressures, demonstrating its capability to withstand rigorous use.
Equipped with integrated electronics, the SYDFEE-3X/071R-VRB22U00-0479-A2A0FLX offers precise control over swivel angle and pressure, making it suitable for applications requiring exact hydraulic fluid management. The system's functionality includes swivel angle control, pressure control, torque limitation, and the ability to operate in Master/Slave configurations. These features underscore its versatility in various hydraulic tasks.
The pump's controls are enhanced by an analog communication interface that allows for easy configuration and monitoring. The external pilot oil system ensures reliable performance under maximum pressure conditions. Its shaft type is a geared shaft R that guarantees smooth operation, while the electrical connection utilizes a Connector pole PE according to EN Size standards.
This model operates within a speed range from min to max RPMs and can achieve a max flow rate as per its design specifications. The displacement type is variable, ensuring adaptability to different working conditions with clockwise rotation directionality. It supports a supply voltage of VDC and is compatible with HLP hydraulic fluid.
The SYDFEE-3X/071R-VRB22U00-0479-A2A0FLX also boasts durable FKM seals and offers connectivity through analog interfaces. Its construction includes essential components like swash plate, pilot control valve, counter piston, actuating piston, spring mechanism, inductive position transducer for valve position feedback, swivel angle position sensor, proportional solenoid for precise control adjustments and precompression volume PCV.
Overall, this Bosch Rexroth hydraulic pump system stands out for its sophisticated design tailored for high-performance applications requiring meticulous fluid power management and control.
$13,492.00 USD
More are expected on March 30, 2026
Qty | Price | Savings |
---|---|---|
5-24 | $13,154.70 USD | $337.30 USD |
25+ | $12,817.40 USD | $674.60 USD |
Status: This product is temporarily out of stock.
Qty: Delivered as early as March 30, 2026 when ordered in
This product is eligible for factory repair.
Pump A10VSO BR32 with analog OBE
Pump system, maximum operating pressure 280 bar, frame size 71, functionality: Swivel angle, pressure control, master/slave
Unpacked Weight: 51.000 kg
A SYDFEE-3X control system is used for the electro-hydraulic control of swivel angle, pressure and power (partially optional, see type key pilot control and preload valve and ordering code accessories) of an axial piston variable displacement pump.
The control system consists of the following components: Axial piston variable displacement pump A10VSO.../32 VT-DFPE-.2X proportional valve as pilot valve with integrated electronics including inductive position transducer for valve position sensing. Position transducer for sensing the swivel angle Pressure transducer with suitable signal level and dynamics (optionally HM 20, otherwise separate order) Preload valve with integrated pressure relief function SYDZ (optional)
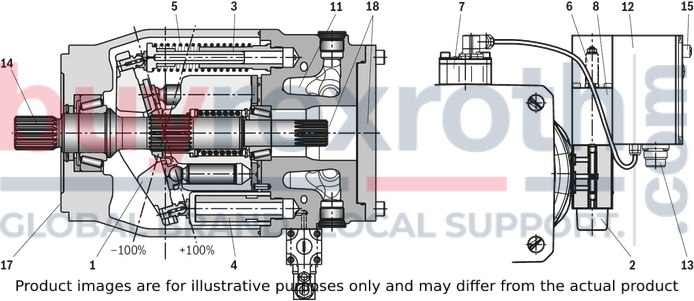
1 |
Swash plate |
2 |
Pilot control valve |
3 |
Counter piston |
4 |
Actuating piston |
5 |
Spring |
6 |
Inductive position transducer for valve position |
7 |
Swivel angle position sensor |
8 |
Proportional solenoid |
11 |
Pre-compression volume PCV |
12 |
Integral electronics |
13 |
Connector X1 |
14 |
Drive shaft |
15 |
Connector X2 for connection of the HM 20 pressure transducer cable version (only with actual pressure value input F) |
17 |
Connection flange |
18 |
Through-drive U.. closed with cover |
Pressure sensor 315 bar |
Pump A10VSO BR32 with analog OBE |
Component series 3X |
71 cm³ |
Nominal pressure 280 bar |
Communication: analog |
Ext. Pilot oil |
Maximum operating pressure 280 bar |
Size 45 … 180 |
Communication: Analog |
Function: Pressure, swivel angle control, torque limitation, master-slave |
With axial piston variable displacement pump A10VSO.../32 |
Data Sheet | Download Data Sheet |
Manual | Download Manual |
Manual | Download Manual |
Manual | Download Manual |
Manual | Download Manual |
Manual | Download Manual |
Max. pressure | 280 |
Shaft end | Geared shaft (R) |
Electrical connection description | Connector 12-pole (11 + PE) according to EN 175201-804 |
Size | 71 |
Speed min. | 250 |
Productgroup ID | 9,10,11,12,13,14 |
Controls | Integrated electronics |
Speed max. | 1800 |
Electrical connector | Connector 12-pole (11 + PE) |
Mounting flange | ISO 4-hole |
Max. flow | 128 |
Displacement type | variable |
Direction of rotation | clockwise rotation |
Supply voltage | 24 VDC |
Through-drive | with |
Weight | 51.000 |
Seals | FKM |
Connectivity | Analog |
Hydraulic fluid | HLP |
01 |
02 |
03 |
04 |
05 |
06 |
07 |
08 |
09 |
10 |
11 |
12 |
13 |
14 |
15 |
16 |
17 |
||||
SYDFEE-3X |
/ |
071 |
– |
R |
22 |
U99- |
0000 |
– |
A |
0 |
A |
0 |
F |
L |
2 |
– |
* |
Pump of the SYDFE control system |
|||||||
Series |
|||||||
01 |
Control system with internal analog electronics |
SYDFEE-3X |
|||||
Pump combinations (see order example) |
SY2DFE.-2X, SY3DFE.-2X |
||||||
Size |
045 |
071 |
100 |
140 |
180 |
||
02 |
Displacement cm³ |
45 |
71 |
100 |
140 |
180 |
|
Direction of rotation looking at the drive shaft |
|||||||
03 |
Right |
● |
● |
● |
● |
● |
R |
Hydraulic fluid |
|||||||
04 |
Mineral oil according to DIN 51524 (HL/HLP) |
● |
● |
● |
● |
● |
V |
Drive shaft variant |
|||||||
05 |
Splined shaft profile SAE J 744 1) |
– |
– |
1 1/2’’ |
1 3/4’’ |
1 3/4’’ |
S |
Splined shaft profile SAE J 744 (higher through-drive torque) |
1’’ |
1 1/4’’ |
– |
– |
– |
R |
|
Connection flange according to ISO 30319-2 (4-hole) Ø centering in mm |
|||||||
06 |
ISO 4-hole |
125 |
160 |
180 |
180 |
180 |
B |
Subplate design |
|||||||
07 |
Without shock and vibration absorption (pre-compression volume, PCV) |
● |
● |
● |
● |
– |
22 |
With shock and vibration absorption (pre-compression volume, PCV; not with base pump variant 0487 or 0541 and not as high-speed version) |
– |
● |
● |
● |
● |
32 |
|
Design/through-drive |
|||||||
08 |
Universal through-drive U99 closed operationally safe with end cover at the factory; for components for the adaptation of more pump stages, see table Accessories for through-drives |
– |
● |
● |
● |
● |
U99- |
High speed version and universal through-drive U.. closed operationally safe with end cover at the factory; not with subplate 32; for components for the adaptation of more pump stages, see table Accessories for through-drives |
– |
● |
● |
● |
– |
U99S |
|
● |
– |
– |
– |
– |
U00S |
||
Base pump variant |
|||||||
09 |
Standard (internal pilot oil) |
● |
● |
● |
● |
0000 |
|
External supply |
● |
● |
– 2) |
● |
0479 |
||
External supply + regenerative operation |
● |
● |
● |
– |
0487 |
||
Regenerative operation without external supply |
● |
● |
– 2) |
– |
0541 |
||
Pilot valve of the SYHDFEE control system |
|||||||
Spool design |
|||||||
10 |
Standard |
A |
|||||
4-groove spool |
C |
||||||
Integrated electronics, installation orientation, see note on feature 11 |
|||||||
11 |
Radially to the pump axis |
0 |
|||||
folded 90° in the direction of the subplate |
2 |
||||||
Control, additional function |
A |
B |
C |
D |
|||
12 |
Switchable pressure controller (high signal) |
● |
A |
||||
Power limitation adjustable at the OBE valve |
● |
B |
|||||
Power limitation adjustable via analog input |
● |
C |
|||||
Pressure controller that can be switched off (high signal) |
● |
D |
|||||
Electronics assembly, option |
|||||||
13 |
Standard electronics with leakage oil compensation |
● |
● |
● |
● |
0 |
|
Standard electronics without leakage oil compensation |
● |
● |
● |
● |
1 |
||
Actual pressure value input |
Plug-in connector |
C |
V |
E |
F |
||
14 |
Current input 4...20 mA |
X1 |
● |
C |
|||
Voltage input 0...10 V |
X1 |
● |
V |
||||
Voltage input 1...10 V |
X1 |
● |
E |
||||
Voltage input 0.5...5 V |
X2 |
● |
F |
||||
Pressure transducer |
|||||||
15 |
HM 20-2X/315-F-C13-0,5, measurement range 315 bar (0.5...5 V) with connection cable 0.5 m for direct connection to X2 (only in connection with actual pressure value input F) |
– |
– |
– |
● |
L |
|
Without pressure transducer |
● |
● |
● |
● |
X |
||
Preload valve with integrated pressure limitation |
|||||||
16 |
Pressure limitation 200 bar (tolerance ± 8 bar) 3) |
1 |
|||||
Pressure limitation 250 bar (tolerance ± 10 bar) 3) |
2 |
||||||
Pressure limitation 300 bar (tolerance ± 12 bar) 3) |
3 |
||||||
Without preload valve |
X |
||||||
17 |
Further details in the plain text e. g. SO variant |
* |
1) | ANSI B92.1a-1976, 30° pressure angle, flat root, side fit, tolerance class 5. |
2) | Size 140 with subplate 22 (without PCV) is always suitable for regenerative operation; thus, the option is omitted. |
3) | The pressure relief function of the preload valve is designed for a maximum speed of 1800 rpm for NG140 and for a maximum speed of 1500 rpm for NG180. Higher speeds are available on request. |
● |
available |
- |
not available |
Note on feature 11: Valve, installation orientation of the integrated electronics |
|
Clockwise direction of rotation, installation orientation 0 |
Clockwise direction of rotation, installation orientation 2 |
![]() |
![]() |
Order example for single pump:
SYDFEE-3X/100R-VSB32U99-0479-A0A0XX
Order example for pump combinations: |
|||||
Double pump: |
|||||
Material numbers and/or type designations are to be connected by means of "+". |
|||||
Double pump |
2 |
||||
Size of the main pump |
100 |
||||
Size of the attachment pump or pump abbreviation if the attachment pump is not SYDFE (e. g. PGF) |
071 |
||||
Material number without "R9" for the main pump or type designation if material number is not known |
SYDFEE-3X/100R-VSB32U99-0000-A0A1VX3 |
||||
Pump combination, mounted with accessories |
Main pump (1st pump) |
+ |
Attachment pump (2nd pump) |
||
SY2DFEE-3X/100-071/01177440 |
+ |
01177441 |
|||
Material number without "R9" for the attachment pump or type designation if material number is not known |
SYDFEE-3X/071R-VRB32U99-0000-A0A1VX3 |
||||
Triple pump: |
Main pump (1st pump) |
+ |
Attachment pump (2nd pump) |
+ |
Attachment pump (3rd pump) |
SY3DFEE-3X/01128835 |
+ |
01151805 |
+ |
01128836 |
Example of name plate of a single pump
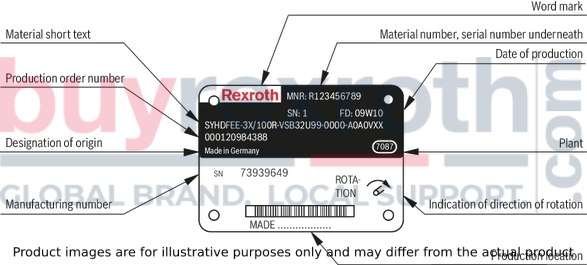
Notice:
For enquiries regarding the control system, material number, production order number, serial number, and date of production are necessary.
Accessories
Version 10/2015, enquire availability
Accessories |
Material number |
Data sheet |
Mating connector 12-pole for central connection X1 without cable (assembly kit) |
R900884671 |
08006 |
Mating connector 12-pole for central connection X1 with cable set 2 x 5 m |
R900032356 |
|
Mating connector 12-pole for central connection X1 with cable set 2 x 20 m |
R900860399 |
|
Pressure transducer HM 20-2X, measurement range 315 bar (4 ... 20 mA) |
R901342029 |
30272 |
Pressure transducer HM 20-2X, measurement range 315 bar (0.1 ... 10 V) |
R901342030 |
30272 |
Test device VT-PDFE-1-1X/V0/0 |
R900757051 |
29689-B |
Compact power supply unit VT-NE32-1X |
R90080049 |
29929 |
More accessories |
||
Accessories for through-drives |
See Accessories |
|
Torsionally flexible couplings for attachment to a standard electric motor |
See Accessories |
mechanisch und hydraulisch
Size |
45 | 71 | 100 | 140 | 180 | ||||
Displacement |
Vg max |
cm³ |
45 | 71 | 100 | 140 | 180 | ||
Max. speed |
Standard version |
no max |
rpm |
- | 1800 1) | 1800 2) | |||
High-speed version 2) |
no max |
rpm |
3000 | 2550 | 2300 | 2200 | - | ||
Minimum speed |
nmin |
rpm |
50 | ||||||
Max. flow (displacement) |
with max. speed (standard version) |
qv0 max |
l/min |
- | 128 | 180 | 252 | 324 | |
with max. speed (high-speed version) |
qv0 max |
l/min |
135 | 181 | 230 | 308 | - | ||
with nE = 1500 min-1 |
l/min |
67.5 | 106.7 | 150 | 210 | 270 | |||
Max. power (Δp = 280 bar) |
with max. speed (standard version) |
P0 max |
kW |
- | 59.7 | 84 | 118 | 151 | |
with max. speed (high-speed version) |
P0 max |
kW |
62.8 | 85 | 107 | 144 | - | ||
with nE = 1500 min-1 |
kW |
31 | 50 | 70 | 98 | 125 | |||
Max. torque (Δp = 280 bar, n0 max) |
Tmax |
Nm |
200 | 317 | 446 | 624 | 802 | ||
Maximum permissible drive torque |
Splined shaft S overall torque |
Ttotal |
Nm |
- | 1104 | 1620 | |||
Max. admissible through-drive torque |
TD |
Nm |
- | 778 | 1266 | ||||
Splined shaft R overall torque |
Ttotal |
Nm |
400 | 644 | - | ||||
Max. admissible through-drive torque |
TD |
Nm |
365 | 548 | - | ||||
Drive shaft load |
![]() |
max. admissible axial force |
Fax max |
N |
1500 | 2400 | 4000 | 4800 | 800 |
max. admissible radial force |
Fq |
N 3) |
1500 | 1900 | 2300 | 2800 | 2300 | ||
Mass |
Pump without through-drive incl. pilot valve |
m |
kg |
32 | 49 | 71 | 75 | 80 | |
in addition, preload valve |
m |
kg |
3.3 | 6.3 | |||||
in addition, in case of external supply |
m |
kg |
2 | ||||||
Moment of inertia around drive axis |
JTW |
kg·m² |
0.0035 | 0.0087 | 0.0185 | 0.0276 | 0.033 | ||
Filling quantity of the housing |
V |
l |
1 | 1.6 | 2.2 | 3 | 2.7 | ||
Nominal pressure |
pnenn |
bar |
280 | ||||||
Maximum admissible operating pressure 4) |
pmax |
bar |
350 | ||||||
Operating pressure, min. (without load) |
with preload valve |
pmin |
bar |
≥ 1 | |||||
without preload valve |
pmin |
bar |
≥ 20 | ||||||
in case of external supply (20 bar) 5) |
pmin |
bar |
> 10 | ||||||
Admissible inlet pressure |
p |
bar |
1 ... 10 | 0.8 ... 10 | 1 ... 10 | ||||
bar |
- | 1 ... 10 | - | ||||||
Hydraulic fluid |
Mineral oil (HL, HLP) to DIN 51524 | ||||||||
Hydraulic fluid temperature range |
ϑ |
°C |
+70 | -20 … +70 | |||||
Maximum admissible degree of contamination of the hydraulic fluid according to ISO 4406 |
Class 18/16/13 (for particle size ≤ 4/6/14 μm) |
1) | The values are applicable at an absolute pressure of 0.8 bar at suction opening S. |
2) | The value is applicable at an absolute pressure of 1.0 bar at suction opening S. |
3) | In case of higher radial forces, please consult us |
4) | See also data sheet 92714 |
5) | In continuous operation; in case of operation below 10 bar, observe the notes |
elektrisch
Size |
45 | 71 | 100 | 140 | 180 | |||
Operating voltage |
UB |
24 +40 % –5 % | ||||||
Operating range (short-time operation) |
Upper limit value |
UB(t)max |
V |
35 | ||||
Lower limit value |
UB(t)min |
V |
21 | |||||
Current consumption (in static control operation) |
Rated current |
Inom |
A |
0.6 | ||||
Maximum current |
Imax |
A |
1.25 | |||||
Inputs |
Actual pressure value input X1; |
U or I |
Determination by means of ordering code | |||||
Analog current inputs, load 1) |
RB |
100 Ω | ||||||
Analog voltage inputs |
RE |
≥ 50 kΩ | ||||||
Digital inputs |
Logic 0 |
≤ 0,6 V | ||||||
Logic 1 |
≥ 21 V | |||||||
Outputs |
pactual / UOUT1 |
UO |
0 … 10 V | |||||
Imax |
1,5 mA | |||||||
αactual / UOUT2 |
UO |
± 10 V | ||||||
Imax |
1,5 mA | |||||||
Digital outputs |
Logic 0 |
Ua < 1 V | ||||||
Logic 1 |
Ua ≥ UB – 5 V; 10 mA (short-circuit-proof) | |||||||
Ambient temperature range at the pump |
ϑ |
°C |
0 … 60 | |||||
Storage temperature range (pump + electronics) |
ϑ |
°C |
0 … 70 | |||||
Electronics design |
Integrated in the pilot valve (OBE) | |||||||
Type of protection according to EN 60529 |
Pump incl. pilot valve |
IP65 with mounted and locked plug-in connectors |
1) | With configuration on current input: Maximum admissible input current 30 mA |
2) | With SYDFEC, SYDFEn and SYDFED, the outputs are parameterizable, for the condition as supplied, see electrical connection. |
Notice:
For information on the environment simulation testing for the areas EMC (electro-magnetic compatibility), climate and mechanical load, see data sheet 30630-U.
Control loop quality
Notes:
The specified values are only valid when using the system-related components specified in this data sheet. At pressures < 20 bar, higher tolerances have to be anticipated due to lower actuating forces.
Swivel angle control |
Pressure control 1) |
|
Linearity tolerance |
≤ 1,0 % |
≤ 1,5 % (≤ 1,0 %) |
Temperature error |
≤ 0,5 % / 10 K |
≤ 0,5 % / 10 K |
Hysteresis |
≤ 0,2 % |
≤ 0,2 % |
Repetition accuracy |
≤ 0,2 % |
≤ 0,2 % |
1) | Without considering the pump pulsation. |
For applications outside these parameters, please consult us!
Transition function with pressure command value step with spool design "A"
The specified curve shapes and control times refer to a drive speed of 1500 rpm and are only reached with an optimization of the pressure controller.
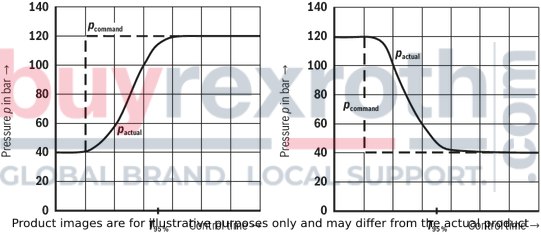
T95% in ms with a connected hydraulic fluid volume (lines and actuators)
Hydraulic fluid volume in l |
T95% in ms |
< 5 |
150 |
5 – 10 |
200 |
15 ... 25 |
250 |
For pressures up to 40 bar, the values of the response times are greater.
Transition function with swivel angle command value step with spool design "A"
NG45, 71 p = 50 bar

Size 100 p = 50 bar

Size 140 p = 50 bar

NG180 p = 50 bar

Schematic diagram: Actuating system supplied internally

1) |
When using the pressure transducer HM 20 cable version: Installation in P (pump) or MP1 (preload valve) in connection with electronic version "Actual pressure value input F". When using an external pressure transducer: Installation in the P1 line (preferably close to the actuator) and electrical connection via the central connector. When using a preload valve, the pressure transducer is to be connected to P1 or MP1. |
Schematic diagram: Actuating system supplied externally
The representation shows an example with integrated electronics.
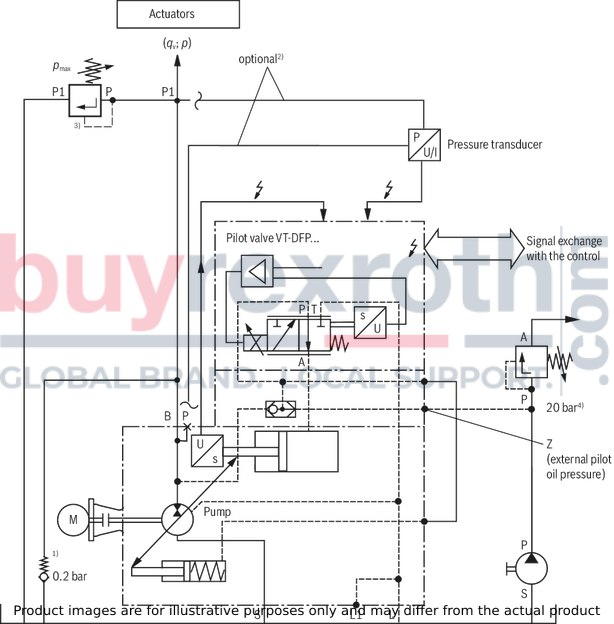
1) | The use of an anti-cavitation valve (check valve with 0.2 bar spring) is essential in order to prevent dry-running in the error case. |
2) |
Pressure transducer |
Mounting options |
Comment |
HM 20-2X/315-F-C13-0.5 (cable version) |
P |
Only in connection with actual pressure value input "F" |
|
HM 20-2X/...-.-K35 (connector version) |
P1 |
Preferably close to the actuator |
3) Maximum pressure limitation must be provided by the customer! | |
4) Observe upper limit for external pilot oil pressure! (see operating instructions), recommendation: 20 bar absolute. |
Important notes on external supply:
In the case of an actuating system with external supply, the pump adjustment will - in case of voltage failure - not switch to zero stroke but to the negative stop (displacement of 100 % flow from the system to the tank). With an active fault message, it is imperative that the machine control reacts (e. g. switching off the drive motor of the pump, interrupting the external supply of the actuating system). The command values for pressure and flow must always be greater than zero (pcommand ≥ 3 bar, αcommand ≥ 5 %) as due to drift or tolerances, there is no exact "zero" pressure or "zero" swivel angle. Under unfavorable conditions, smaller command value presettings can lead to cavitation. The actual pressure value must not be less than 10 bar for more than 10 minutes (lubrication).
Allocation of connector or mating connector and cable set
Pin |
Signal |
Description |
Signal direction |
Type of signal |
Allocation in the cable set (accessories) |
|
1 |
+ UB |
Voltage supply |
IN |
24 V DC |
1 |
Supply line 3 x 1.0 mm2 |
2 |
0 V = L0 |
Reference potential for the voltage supply |
– |
2 |
||
PE |
Earth |
Earthing connection for the electronics |
– |
green/yellow |
||
3 |
Fault |
Signals faults, e.g. cable break command / actual values, controller monitoring (logic 0 = error) |
OUT |
logic 24 V |
white |
Supply line 10 x 0.14 mm2 shielded (one end of the shield must be connected to the control!) |
4 |
M0 |
Reference potential for analog signals |
– |
yellow |
||
5 |
αCommand |
Swivel angle command value |
IN |
analog ±10 V |
green |
|
6 |
αActual |
Actual swivel angle value, normalized |
OUT |
analog ±10 V |
Violet |
|
7 |
pCommand |
Pressure command value |
IN |
analog 0...10 V |
pink |
|
8 |
pActual |
Actual pressure value, normalized |
OUT |
analog 0...10 V 1) |
red |
|
9 |
Function dependent on electronic type and additional function, see table Functions at pin 9 |
brown |
||||
10 |
Actual pressure value H |
Actual pressure value input: Signal level dependent on feature 14 of the ordering codes Reserved with type "F" (0.5...5 V) |
IN |
analog |
black |
|
11 |
Actual pressure value L |
– |
analog |
blue |
||
n.c. |
gray |
Functions at pin 9
Pin |
Additional function |
Function dependent on feature 12 of the ordering codes (see page type key pilot and preload valve) |
Signal direction |
Type of signal |
9 |
-..A… |
Selecting a different oil volume adjustment (switch TD) |
IN |
logic 24 V |
-..B… |
Power limitation active |
OUT |
logic 24 V |
|
-..C… |
Command value of power limitation |
IN |
analog 0...10 V |
|
-..D… |
Switch off pressure controller |
IN |
logic 24 V |
1) | When using a pressure transducer with raised zero point (e. g. 4 ... 20 mA), a voltage of –1 ... –2.5 V will be output in case of a cable break. |
X2: Connection of pressure transducer HM 20
HM 20-2X/315-F-C13-0,5 (cable version) (mating connector M12)
Pin |
Signal HM 20 |
Pin |
|
1 |
OUT, +UB |
2 |
n.c. |
3 |
Reference L0 |
||
4 |
IN, analog, 0.5 to 5 V DC |
5 |
n.c. |
Integrated electronics with installation orientation 0
The dimensions of the base pump (axial piston variable displacement pump A10VSO.../32) are contained in data sheet 92714.
NG45 … 180
(Valve mounting direction "0"; shaft design "S" or "R" with universal through-drive “U..")
Dimensions in mm
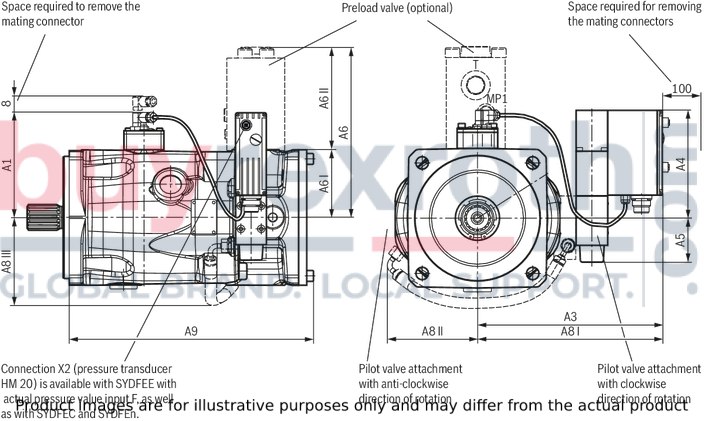
(representation size 100)
Size |
Dimensions with base pump variant "0479" or "0487" |
Max. length |
|||||||||
A1 |
A3 1) |
A4 |
A5 |
A6 |
A6 I |
A6 II |
A8 I |
A8 II |
A8 III |
A9 |
|
mm |
mm |
mm |
mm |
mm |
mm |
mm |
mm |
mm |
mm |
mm |
|
45 | 134 | 218 | 158 | 63 | 206 | 91 | 115 | 253 | 145 | 125 | 266 |
71 | 146 | 226 | 158 | 63 | 254 | 104 | 150 | 261 | 159 | 150 | 301 |
100 | 151 | 237 | 158 | 63 | 247 | 100 | 147 | 272 | 164 | 150 | 360 |
140 | 162 | 250 | 158 | 63 | 257 | 110 | 147 | 285 | 182 | 150 | 377 |
180 | 162 | 250 | 158 | 63 | 257 | 110 | 147 | 285 | 182 | 150 | 387 |
1) | Dimension with base pump variant 0000 or 0541 |
Integrated electronics with installation orientation 2
The dimensions of the base pump (axial piston variable displacement pump A10VSO.../32) are contained in data sheet 92714.
NG45 … 180
(Valve mounting direction “2"; shaft design "S" or "R" with universal through-drive “U..”)
Dimensions in mm
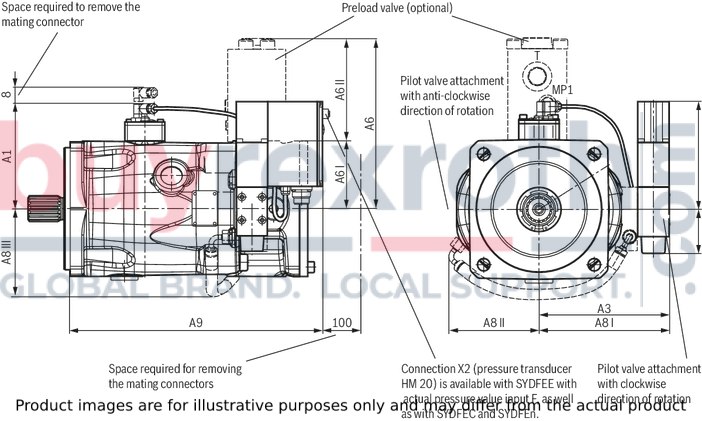
(representation size 100)
Size |
Dimensions with base pump variant "0479" or "0487" |
Max. length |
|||||||||
A1 |
A3 1) |
A4 |
A5 |
A6 |
A6 I |
A6 II |
A8 I |
A8 II |
A8 III |
A9 |
|
mm |
mm |
mm |
mm |
mm |
mm |
mm |
mm |
mm |
mm |
mm |
|
45 | 134 | 138 | 158 | 63 | 206 | 91 | 115 | 173 | 145 | 125 | 287 |
71 | 146 | 146 | 158 | 63 | 254 | 104 | 150 | 181 | 159 | 150 | 316 |
100 | 151 | 157 | 158 | 63 | 247 | 100 | 147 | 192 | 164 | 150 | 372 |
140 | 162 | 170 | 158 | 63 | 257 | 110 | 147 | 205 | 182 | 150 | 382 |
180 | 162 | 170 | 158 | 63 | 257 | 110 | 147 | 205 | 182 | 150 | 392 |
1) | Dimension with base pump variant 0000 or 0541 |
Combination pumps BR32

Attachment pump |
Main pump |
|||||||||||||||||||
A10VSO 45 |
A10VSO 71 |
A10VSO 100 |
A10VSO 140 |
A10VSO 180 |
||||||||||||||||
A1 |
A2 |
A3 |
A4 |
A1 |
A2 |
A3 |
A4 |
A1 |
A2 |
A3 |
A4 |
A1 |
A2 |
A3 |
A4 |
A1 |
A2 |
A3 |
A4 |
|
A10VSO 18 BR31 |
184 |
264 |
409 |
459 |
217 |
299 |
444 |
494 |
275 |
360 |
505 |
555 |
275 |
377 |
522 |
572 |
285 |
387 |
532 |
582 |
A10VSO 28 BR31 |
184 |
264 |
428 |
470 |
217 |
299 |
463 |
505 |
275 |
360 |
524 |
566 |
275 |
377 |
541 |
583 |
285 |
387 |
551 |
593 |
A10VSO 45 BR31 |
217 |
299 |
483 |
523 |
275 |
360 |
544 |
584 |
275 |
377 |
561 |
601 |
285 |
387 |
571 |
611 |
||||
A10VSO 45 BR32 |
184 |
264 |
448 |
530 |
217 |
299 |
483 |
565 |
275 |
360 |
544 |
626 |
275 |
377 |
561 |
643 |
285 |
387 |
571 |
653 |
A10VSO 71 BR32 |
217 |
299 |
516 |
600 |
275 |
360 |
577 |
661 |
275 |
377 |
594 |
678 |
285 |
387 |
604 |
688 |
||||
A10VSO 100 BR32 |
275 |
360 |
635 |
720 |
275 |
377 |
652 |
737 |
285 |
387 |
662 |
747 |
||||||||
A10VSO 140 BR32 |
275 |
377 |
652 |
754 |
285 |
387 |
662 |
764 |
||||||||||||
A10VSO 180 BR32 |
285 |
387 |
672 |
774 |
Ports
Size |
45 |
71 |
100 |
140 |
180 |
||
B: |
Working line (SAE J518) 1) |
||||||
Size |
1″ |
1″ |
1 1/4″ |
1 1/4″ |
1 1/4″ |
||
Mounting thread (DIN 13) |
M10 x 1.5; 17 deep |
M14 x 2; 19 deep |
|||||
Peak pressure 2) |
bar |
350 |
|||||
S: |
Suction line (SAE J518) 1) |
||||||
Size |
1 1/2″ |
2″ |
2 1/2″ |
2 1/2″ |
2 1/2″ |
||
Mounting thread (DIN 13) |
M12 x 1.75; 20 deep |
M12 x 1.75; 17 deep |
|||||
Peak pressure 2) |
bar |
10 |
1) | Dimensions according to SAE J518 only, metric mounting thread deviating from the standard. |
2) | Application-specific short-time pressure peaks may occur. Please observe when selecting measuring devices and fittings. Specified pressures are in bar absolute. |
Notes regarding size 71:
With pressure connection “B” of size 71, two SAE mounting connections rotated by 90° are available. SAE 1 1/4″ standard pressure series, 3000 psi , for pressures up to 250 bar or SAE 1″ standard pressure series, 5000 psi, for pressures up to 350 bar. For operating pressures exceeding 250 bar, the pressure flange SAE 1” must be used.Dimensions in mm

Before determining your design, please request a binding installation drawing.
U52
Flange ISO 3019-1-82-2
Hub for splined shaft according to ANSI B92.1a-1996
3/4″ 11T 16/32DP 1)
(SAE J744 - 19-4 (A-B))
Dimensions in mm
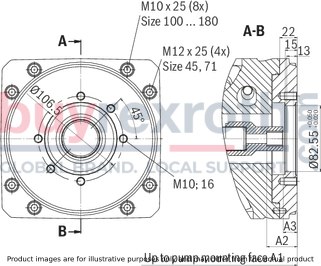
NG |
A1 |
A2 |
A3 |
mm |
mm |
mm |
|
45 | 264 | 38.7 | 18.5 |
71 | 299 | 38 | 17.5 |
100 | 360 | 38 | 17.5 |
140 | 377 | 38 | 17.5 |
180 | 387 | 38 | 17.5 |
UB3
Flange ISO 3019-2 - 100B2HW
Hub for splined shaft according to ANSI B92.1a-1996
7/8″ 13T 16/32DP 1)
(SAE J744 - 22-4 (B))
Dimensions in mm
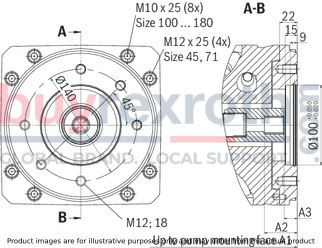
NG |
A1 |
A2 |
A3 |
mm |
mm |
mm |
|
45 | 264 | 41.6 | 18 |
71 | 299 | 41 | 16.5 |
100 | 360 | 41 | 16.5 |
140 | 377 | 41 | 16.5 |
180 | 387 | 41 | 16.5 |
UB4
Flange ISO 3019-2 - 100B2HW
Hub for splined shaft according to ANSI B92.1a-1996
1″ 15T 16/32DP 1)
(SAE J744 - 25-4 (B-B))
Dimensions in mm
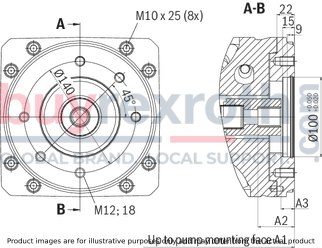
NG |
A1 |
A2 |
A3 |
||
mm |
mm |
mm |
|||
45 | 264 | - | Upon request | - | Upon request |
71 | 299 | 45.9 | - | 16.9 | - |
100 | 360 | 45.9 | - | 16.9 | - |
140 | 377 | 45.9 | - | 16.9 | - |
180 | 387 | 45.9 | - | 16.9 | - |
UE1
Flange ISO 3019-2 - 125 4-hole
Hub for splined shaft according to ANSI B92.1a-1996
1″ 15T 16/32DP 1)
(SAE J744 - 25-4 (B-B))
Dimensions in mm

NG |
A1 |
A2 |
A3 |
||
mm |
mm |
mm |
|||
45 | 264 | - | Upon request | - | Upon request |
71 | 299 | 45.9 | - | 16.9 | - |
100 | 360 | 45.9 | - | 16.9 | - |
140 | 377 | 45.9 | - | 16.9 | - |
180 | 387 | 45.9 | - | 16.9 | - |
UB8
Flange ISO 3019-2 - 160B4HW
Hub for splined shaft according to ANSI B92.1a-1996
1 1/4″ 14T 12/24DP 1)
(SAE J744 - 32-4 (C))
Dimensions in mm
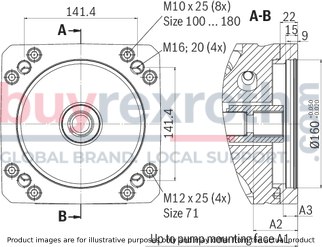
NG |
A1 |
A2 |
A3 |
mm |
mm |
mm |
|
71 | 299 | 55.4 | 17.9 |
100 | 360 | 55.4 | 17.9 |
140 | 377 | 55.4 | 17.9 |
180 | 387 | 55.4 | 17.9 |
UB9
Flange ISO 3019-2 - 180B4HW
Hub for splined shaft according to ANSI B92.1a-1996
1 1/2″ 17T 12/24DP 1)
(SAE J744 - 38-4 (C-C))
Dimensions in mm
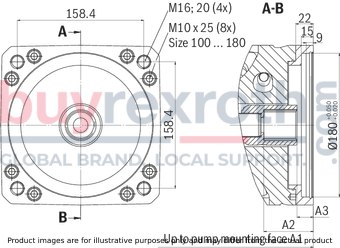
NG |
A1 |
A2 |
A3 |
mm |
mm |
mm |
|
100 | 360 | 61.9 | 20.4 |
140 | 377 | 61.9 | 20.4 |
180 | 387 | 61.9 | 20.4 |
UB7
Flange ISO 3019-2 - 180B4HW
Hub for splined shaft according to ANSI B92.1a-1996
1 3/4″ 13T 8/16DP 1)
(SAE J744 - 44-4 (D))
Dimensions in mm
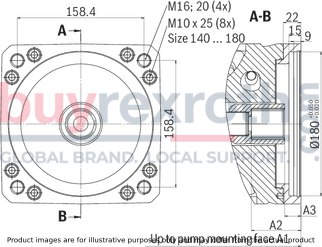
NG |
A1 |
A2 |
A3 |
mm |
mm |
||
140 | 377 | 75 | Upon request |
180 | 387 | 75 | Upon request |
U01
Flange ISO 3019-1-82-2
Hub for splined shaft according to ANSI B92.1a-1996
5/8″ 9T 16/32DP 1)
(SAE J744 - 16-4 (A))
Dimensions in mm
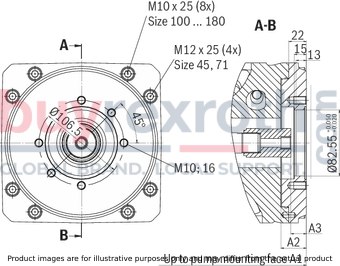
NG |
A1 |
A2 |
A3 |
||
mm |
mm |
mm |
|||
45 | 264 | - | Upon request | - | Upon request |
71 | 299 | 31.8 | - | 19.3 | - |
100 | 360 | 31.8 | - | - | Upon request |
140 | 377 | 31.8 | - | - | Upon request |
180 | 387 | 31.8 | - | - | Upon request |
U68
Flange ISO 3019-1-101-2
Hub for splined shaft according to ANSI B92.1a-1996
7/8″ 13T 16/32DP 1)
(SAE J744 - 22-4 (B))
Dimensions in mm
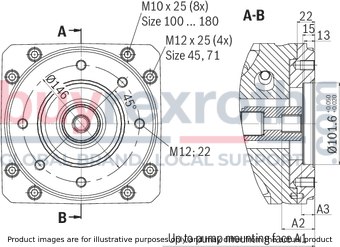
NG |
A1 |
A2 |
A3 |
mm |
mm |
mm |
|
45 | 264 | 41.5 | 18.2 |
71 | 299 | 41 | 16.5 |
100 | 360 | 41 | 16.5 |
140 | 377 | 41 | 16.5 |
180 | 387 | 41 | 16.5 |
U04
Flange ISO 3019-1-101-2
Hub for splined shaft according to ANSI B92.1a-1996
1″ 15T 16/32DP 1)
(SAE J744 - 25-4 (B-B))
Dimensions in mm
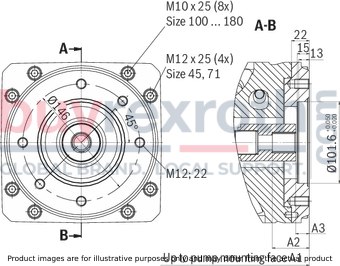
NG |
A1 |
A2 |
A3 |
||
mm |
mm |
mm |
|||
45 | 264 | - | Upon request | - | Upon request |
71 | 299 | 45.9 | - | 16.9 | - |
100 | 360 | 45.9 | - | 16.9 | - |
140 | 377 | 45.9 | - | 16.9 | - |
180 | 387 | 45.9 | - | 16.9 | - |
U24
Flange ISO 3019-1-127-2
Hub for splined shaft according to ANSI B92.1a-1976
1 1/2″ 17T 12/24DP 1)
(SAE J744 - 38-4 (C-C))
Dimensions in mm
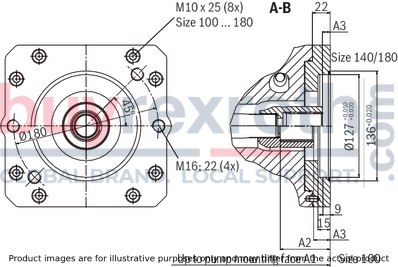
NG |
A1 |
A2 |
A3 |
mm |
mm |
mm |
|
100 | 360 | 61.9 | 20.4 |
140 | 377 | 70.5 | 10.5 |
180 | 387 | 70.5 | 10.5 |
Always shield command and actual value cables. The distance to aerial lines or radios must be at least 1 m. Do not lay signal lines close to power lines. For amending notes on the SYDFE control system, see the operating instructions (see section "More information about this control system").
Accessories for through-drives
With the introduction of A10VSO, series 32, a so-called universal through-drive for combining several pump stages is used. The required components can be seen from the following table and are to be ordered separately. Flange kit and hub are included in the mounting kit.
The following conditions apply to the attachment pumps listed in the table:
SYDFE and A10VSO with shaft S or R PGH with shaft R, flange U2, see data sheet 10223 PGF3 with shaft J, flange U2, see data sheet 10213 AZPF with shaft R, front cover R, see data sheet 10089Also note that the flange and the through-drive (see type key pump) are identical. Check in the current data sheet of the gear pump whether the shaft ends have the specified dimensions.
Components universal through-drive |
Main pump SYDFE..-3X/..U.. |
Attachment pump |
||||||
NG45 |
NG71 |
NG100 |
NG140 |
Size and type |
Through-drive Centering Hub |
Flange designation |
||
Mounting kit |
R902496472 |
R902447036 |
R902447038 |
R902447039 |
NG18 |
SYDFE..-2X/ |
U52 |
ISO 3019-1-82-2 |
Flange kit |
R902514629 |
R902446836 |
R902446850 |
R902446850 |
||||
Hub |
R902436100 |
R902436200 |
R902436201 |
R902436202 |
||||
Mounting kit |
R902492531 |
R902446997 |
R902446999 |
R902447000 |
NG28 |
UB3 |
ISO 3019-2 |
|
Flange kit |
R902492530 |
R902446808 |
R902446809 |
R902446809 |
||||
Hub |
R902436084 |
R902436083 |
R902436101 |
R902436102 |
||||
Mounting kit |
R902447002 |
R902447004 |
R902447005 |
NG45 |
UB4 |
ISO 3019-2 |
||
Flange kit |
R902446808 |
R902446809 |
R902446809 |
|||||
Hub |
R902436104 |
R902436105 |
R902436204 |
|||||
Mounting kit |
R902510125 |
R902492823 |
R902488254 |
R902491915 |
NG45 |
SYDFE..-3X/..U.. |
UE1 |
ISO 3019-2 |
Flange kit |
R902511813 |
R902492824 |
R902446813 |
R902446813 |
||||
Hub |
R902436103 |
R902436104 |
R902436105 |
R902436204 |
||||
Mounting kit |
R902447015 |
R902447017 |
R902447018 |
NG71 |
UB8 |
ISO 3019-2 |
||
Flange kit |
R902446816 |
R902446817 |
R902446817 |
|||||
Hub |
R902436085 |
R902436086 |
R902436106 |
|||||
Mounting kit |
R902447023 |
R902447024 |
NG100 |
UB9 |
ISO 3019-2 |
|||
Flange kit |
R902446820 |
R902446820 |
||||||
Hub |
R910943565 |
R910943555 |
||||||
Mounting kit |
R902447027 |
NG140 |
UB7 |
ISO 3019-2 |
||||
Flange kit |
R902446820 |
|||||||
Hub |
R910932172 |
|||||||
Mounting kit |
R902496467 |
R902447031 |
R902447033 |
R902447034 |
PGF2, PGH2, PGH3, AZPF |
U01 |
ISO 3019-1-82-2 |
|
Flange kit |
R902514629 |
R902446836 |
R902446850 |
R902446850 |
||||
Hub |
R902435448 |
R910943545 |
R910943560 |
R910943551 |
||||
Mounting kit |
R902496477 |
R902447041 |
R902447043 |
R902447044 |
PGF3 |
U68 |
ISO 3019-1-101-2 |
|
Flange kit |
R902511150 |
R902446837 |
R902446851 |
R902446851 |
||||
Hub |
R902436084 |
R902436083 |
R902436101 |
R902436102 |
||||
Mounting kit |
R902496482 |
R902447046 |
R902447048 |
R902447049 |
PGH4 |
U04 |
ISO 3019-1-101-2 |
|
Flange kit |
R902446837 |
R902446851 |
R902446851 |
|||||
Hub |
R902436104 |
R902436105 |
R902436204 |
|||||
Mounting kit |
R902479709 |
R902463283 |
PGH5 |
U24 |
ISO 3019-1-127-2 |
|||
Flange kit |
R902446852 |
R902446852 |
||||||
Hub |
R902436369 |
R910943555 |
1) | ANSI B92.1a-1976, 30° pressure angle, flat root, side fit, tolerance class 5. A mounting kit includes the flange kit and hub; a flange kit includes the flange, seals and mounting materials. |
Combinations are only possible with shaft ends according to SAE J744
Torsionally flexible couplings for attachment to a standard electric motor
Motor |
SYDFE.-3X |
||||
Frame size/characteristic |
Shaft diameter in mm |
NG45 Shaft R, 1" |
NG71 Shaft S or R, 1 1/4" |
NG100 Shaft S, 1 1/2" |
NG140/180 Shaft S, 1 3/4" |
100/0 |
28 |
R901038017 |
|||
132/0 |
38 |
R900772898 |
|||
160/0 |
42 |
R900994283 |
R900228413 |
||
180/0 |
48 |
R900062159 |
R900240468 |
R900242567 |
|
200/0 |
55 |
R901038025 |
R901038021 |
R901104689 |
R901038048 |
225/0 |
60 |
R901066409 |
R900228375 |
R901050508 |
R900988121 |
250/0 |
65 |
R900988348 |
R900986404 |
R901046864 |
R900708084 |
280/0 |
75 |
R900218487 |
R901055216 |
R901052451 |
|
315/0 |
80 |
R901046894 1) |
R901041730 1) |
||
315/1 |
80 |
R901046885 |
1) | Up to 40 °C |
Mating connectors for valves with round connector, 11-pole + PE
12P N11
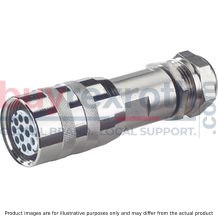
Mating connectors for valves with round connector, 11-pole + PE
12P N11
For valves with round connector according to EN 175201-804, 11-pole + PEData sheet
Spare parts & repair
Mating connectors for valves with round connector, 11-pole + PE, shielded, with assembled connection line
12P N11 +
Mating connectors for valves with round connector, 11-pole + PE, shielded, with assembled connection line
12P N11 +
For valves with round connector according to EN 175201-804, 11-pole + PEData sheet
Spare parts & repair
Related Products
R987054519
$11,702.00 USD
R987096147
$9,869.00 USD
R987054852
$10,543.00 USD
R901099775
$549.00 USD
R961009670
$148.07 USD