LOGIC CARTRIDGE VALVE LC80B10E6X/
Manufacturer: Bosch Rexroth
Material #: R900563206
Model : LC80B10E6X/
***Disclaimer: The following summary contains information gathered from various sources such as product descriptions, technical specifications and catalogs. While efforts have been made to provide accurate details, inaccuracies may occur. It is advised to verify all information by contacting Bosch Rexroth directly.***
The Bosch Rexroth LC80B10E6X/ (R900563206) is a robust industrial hydraulic valve designed for efficient and reliable control of oil flow direction in hydraulic systems. This unidirectional, hydraulically actuated spool type BE valve is part of Bosch Rexroth's high-performance range and is suitable for compact block design applications. It features a maximum pressure capacity that ensures it can handle demanding operational conditions, and it operates with hydraulic actuation to ensure precise control.
The LC80B10E6X/ valve is engineered to be integrated into a control block via a standardized receiving hole according to ISO norms, which is then sealed with a cover that also serves as the connection point for pilot control valves. This design allows the valve to perform pressure, directional, and throttle functions or combinations thereof. The scalability of the valve size to different flow rates enhances its efficiency, making it an economical choice for controlling multiple functions within a system.
Moreover, the LC80B10E6X/ incorporates a modular design comprising a control cover with control bores and installation kit components such as bushing, ring (only up to NG), valve poppet (with or without damping nose), and closing spring. The functionality of this 3-way cartridge valve is pressure-dependent, creating three essential pressurized areas for operation (A1, A2, A3) with varying area ratios ensuring versatile performance.
The direction of fluid flow can be altered from A to B or vice versa by pressurizing area A1 through pilot oil discharge from channel B or an external pilot oil supply. This results in channel A being sealed without leakage when necessary. The poppet design can include damping nose options and different area ratios to achieve various cracking pressures.
This standard series valve comes in size 80 with component series X options available. It has been designed to withstand maximum operating pressures up to several hundred bar and can accommodate maximum flow rates measured in liters per minute as specified by its product group ID. The LC80B10E6X/ employs NBR seals compatible with various hydraulic fluids like HL, HLP, HLPD, HVLP, HVLPD, HFC ensuring versatility across different system requirements.
$4,501.00 USD
More are expected on January 26, 2026
Status: This product is temporarily out of stock.
Qty: Delivered as early as January 26, 2026 when ordered in
This product is eligible for factory repair.
Size 80, unidirectional (A → B), hydraulically actuated, spool type BE
Industrial hydraulic valve in a high performance range. Reliable switching of the oil flow direction according to hydraulic symbol
Unpacked Weight: 11.570 kg
Valve poppet with or without damping nose 2 area ratios 6 different cracking pressures
2-way cartridge valves are elements that have been designed for a compact block design. The power section with connections A and B is installed into the control block in a receiving hole standardized according to ISO 7368 and closed with a cover. In most cases, the cover is also the connection from the control side of the power section to the pilot control valves.
By control with respective pilot control valves, the power section can be applied for pressure, directional and throttle functions or a combination of these functions. Particularly efficient solutions are realized by adjustment of the size to various flows of the individual ways of an actuator. The application of power sections of elements for multiple functions is very cost-effective.
2-way cartridge valves generally consist of control cover (1) and installation kit (2). The control cover contains the control bores and optionally a stroke limitation function, a hydraulically controlled directional seat valve or a shuttle valve according to the required overall function. Additionally, electrically operated directional spool or seat valves can be installed at a control cover. The installation kit consists of a bushing (3), ring (4) (only up to NG32), valve poppet (5), optionally with damping nose (6) or without damping nose (7) as well as closing spring (8).
The function of 2-way cartridge valves is pressure-dependent. This way, three crucial pressurized areas are realized for the function. A1, A2, A3. The area at valve seat A1 is observed as 100 %. Depending on the version, the annulus area A2 realized by grading is 7 % or 50 % of area A1. The area ratio A1 : A2 is respectively either 14.3 : 1 or 2 : 1. The area A3 is identical to the sum of areas A1 + A2. Due to the different area ratios A1 : A2 and the resulting different annulus areas (A2), the area A3 is one time 107 % and another time 150 % of the area A1 at the seat, which is observed as 100 %.
In general, the following applies:
The areas A1 and A2 are effective in opening direction. The area A3 and the spring are effective in closing direction. The direction of action of the resulting force from the opening and closing forces determines the spool position of the 2-way cartridge valve.
The 2-way cartridge valves can be passed from A to B or from B to A. Pressurization of area A3 by pilot oil discharge from channel B or external pilot oil supply, channel A is blocked without leakage.

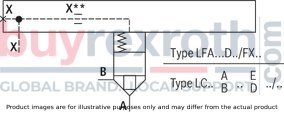
Industrial hydraulic valve in a high performance range |
Reliable switching of the oil flow direction according to hydraulic symbol |
Without overlap |
Annulus area B=7 % |
Standard series |
Component series 6X, 2X, 7X |
Maximum flow 25000 l/min |
Size 16 … 160 |
Maximum operating pressure 420 bar |
Data Sheet | Download Data Sheet |
Manual | Download Manual |
Manual | Download Manual |
Manual | Download Manual |
Manual | Download Manual |
Manual | Download Manual |
Spool symbol | Symbol B10E |
Max. pressure | 420 |
Productgroup ID | 9,10,11,12,13,14 |
Type of actuation | with hydraulic actuation |
Size | 80 |
Max. flow | 8500 |
Type of connection | Cartridge valve |
Connection diagram | ISO 7368 |
Number of switching positions | 2 |
Weight | 11.570 |
Seals | NBR |
Hydraulic fluid | HL,HLP,HLPD,HVLP,HVLPD,HFC |
01 |
02 |
03 |
04 |
05 |
06 |
07 |
|
LC |
/ |
Type |
||
01 |
Cartridge valve |
LC |
Size |
||
02 |
Size 16 |
16 |
Size 25 |
25 |
|
Size 32 |
32 |
|
Size 40 |
40 |
|
Size 50 |
50 |
|
Size 63 |
63 |
|
Size 80 |
80 |
|
Size 100 |
100 |
|
Size 125 |
125 |
|
Size 160 |
160 |
|
Spool design 1) |
||
03 |
A1 : A2 = 2 : 1 (A2 = 50 %) |
A |
A1 : A2 = 14.3 : 1 (A2 = 7 %) |
B |
|
Cracking pressure |
||
04 |
0 bar (without spring) |
00 |
approx. 0.5 bar |
05 |
|
approx. 1 bar |
10 |
|
approx. 2 bar |
20 |
|
approx. 3 bar (NG125 only) |
30 |
|
approx. 4 bar (not NG125) |
40 |
|
Damping |
||
05 |
Valve poppet without damping nose |
E |
Valve poppet with damping nose |
D |
|
Component series |
||
06 |
Component series 70 ... 79 (70 ... 79: unchanged installation and connection dimensions) 2) |
7X |
Component series 60 … 69 (60 … 69: unchanged installation and connection dimensions) 3) |
6X |
|
Component series 20 ... 29 (20 ... 29: unchanged installation and connection dimensions) 4) |
2X |
|
Seal material |
||
07 |
NBR seals |
no code |
FKM seals |
V |
|
Observe compatibility of seals with hydraulic fluid used. (Other seals upon request) |
1) | See "Product description" |
2) | Size 16 ... 63 |
3) | Size 80 ... 100 |
4) | Size 125 ... 160 |
general
Size |
16 | 25 | 32 | 40 | 50 | 63 | 80 | 100 | 125 | 160 | ||
Weight |
kg |
0.25 | 0.5 | 1.1 | 1.9 | 3.9 | 7.2 | 13 | 27 | 44 | 75 | |
Ambient temperature range |
NBR seals |
°C |
-30 … +60 | |||||||||
FKM seals |
°C |
-20 … +60 | ||||||||||
MTTFD values according to EN ISO 13849 1) |
Years |
150 |
1) | For further details, see data sheet 08012 |
hydraulic
Size |
16 | 25 | 32 | 40 | 50 | 63 | 80 | 100 | 125 | 160 | ||
Maximum operating pressure 1) |
Port A |
bar |
315 350 420 |
|||||||||
Port B |
bar |
315 350 420 |
||||||||||
Maximum flow 2) |
l/min |
25000 | ||||||||||
Hydraulic fluid |
see table "Hydraulic fluid" | |||||||||||
Hydraulic fluid temperature range |
NBR seals |
°C |
-30 … +80 | |||||||||
FKM seals |
°C |
-20 … +80 | ||||||||||
Viscosity range |
mm²/s |
2.8 … 500 | ||||||||||
Maximum admissible degree of contamination of the hydraulic fluid, cleanliness class according to ISO 4406 (c) 3) |
Class 20/18/15 |
1) | dependent on the attached directional valve |
2) | NG-dependent; see characteristic curves |
3) | The cleanliness classes specified for the components must be adhered to in hydraulic systems. Effective filtration prevents faults and simultaneously increases the life cycle of the components. For the selection of the filters, see www.boschrexroth.com/filter. |
Hydraulic fluid |
Classification |
Suitable sealing materials |
Standards |
Data sheet |
|
Mineral oils |
HL, HLP, HLPD, HVLP, HVLPD |
NBR, FKM |
DIN 51524 |
90220 |
|
Bio-degradable 1) |
Insoluble in water |
HETG |
NBR, FKM |
ISO 15380 |
90221 |
HEES |
FKM |
||||
Soluble in water |
HEPG |
FKM |
ISO 15380 |
||
Flame-resistant |
Water-free |
HFDU (glycol base) |
FKM |
ISO 12922 |
90222 |
HFDU (ester base) 1) |
FKM |
||||
Containing water 1) |
HFC (Fuchs Hydrotherm 46M, Petrofer Ultra Safe 620) |
NBR |
ISO 12922 |
90223 |
|
Important information on hydraulic fluids: For more information and data on the use of other hydraulicfluids, please refer to the data sheets above or contact us. There may be limitations regarding the technical valve data (temperature, pressure range, life cycle, maintenance intervals, etc.). Flame-resistant - containing water: Life cycle as compared to operation with mineral oil HL, HLP 30 … 100%. Maximum hydraulic fluid temperature 60 °C Bio-degradable and flame-resistant: If this hydraulic fluid is used, small amounts of dissolved zinc may get into the hydraulic system. |
1) | Not recommended for corrosion-protected version "J3" (contains zinc) |
Size of the annulus area
Surface in cm2 |
Version |
Size |
|||||||||
16 |
25 |
32 |
40 |
50 |
63 |
80 |
100 |
125 |
160 |
||
A1 |
LC..A.. |
1,89 |
4,26 |
6,79 |
11,1 |
19,63 |
30,02 |
37,9 |
63,6 |
95 |
160,6 |
LC..B.. |
2,66 |
5,73 |
9,51 |
15,55 |
26,42 |
41,28 |
52,8 |
89,1 |
133,7 |
224,8 |
|
A2 |
LC..A.. |
0,95 |
1,89 |
3,39 |
5,52 |
8,64 |
14,0 |
18,84 |
31,4 |
48 |
79,9 |
LC..B.. |
0,18 |
0,43 |
0,67 |
1,07 |
1,85 |
2,90 |
3,94 |
5,9 |
9,3 |
15,7 |
|
A3 |
LC..A.. |
2,84 |
6,16 |
10,18 |
16,62 |
28,27 |
44,2 |
56,74 |
95 |
143 |
240,5 |
LC..B.. |
2,84 |
6,16 |
10,18 |
16,62 |
28,27 |
44,2 |
56,74 |
95 |
143 |
240,5 |
Spool form (damping nose)
Version |
Size |
|||||||||||
16 |
25 |
32 |
40 |
50 |
63 |
80 |
100 |
125 |
160 |
|||
Stroke |
cm |
LC..E.. |
0,9 |
1,17 |
1,4 |
1,7 |
2,1 |
2,3 |
2,4 |
3,0 |
3,8 |
5,0 |
LC..D.. |
0,9 |
1,17 |
1,4 |
1,9 |
2,3 |
2,8 |
3,0 |
3,8 |
4,8 |
6,5 |
||
Pilot volume |
cm3 |
LC..E.. |
2,56 |
7,21 |
14,3 |
28,3 |
59,4 |
102 |
136 |
285 |
544 |
1203 |
LC..D.. |
2,56 |
7,21 |
14,3 |
31,6 |
65,0 |
124 |
170 |
361 |
687 |
1563 |
||
Theoretical pilot flow 1) |
l/min |
LC..E.. |
15,4 |
43,3 |
86 |
170 |
356 |
612 |
816 |
1710 |
3264 |
7218 |
LC..D.. |
15,4 |
43,3 |
86 |
190 |
390 |
744 |
1020 |
2166 |
4122 |
9378 |
1) | Theoretical pilot flow for realization of a switching time of 10 ms |
Notice:
Spools with damping nose are mainly used in applications with stroke limitation and spool position monitoring. Due to the better flow values, we recommend the spool without damping nose by default.
Cracking pressure in bar
Version |
Size |
||||||||||
16 |
25 |
32 |
40 |
50 |
63 |
80 |
100 |
125 |
160 |
||
Direction of flow A to B |
LC..A 00.. |
0,02 |
0,025 |
0,05 |
0,05 |
0,05 |
0,07 |
0,07 |
0,1 |
0,15 |
0,15 |
LC..A 05.. |
0,35 |
0,35 |
0,36 |
0,35 |
0,37 |
0,31 |
0,44 |
0,43 |
0,43 |
0,45 |
|
LC..A 10.. |
0,70 |
0,68 |
0,72 |
0,71 |
0,67 |
0,64 |
0,88 |
0,88 |
0,88 |
– |
|
LC..A 20.. |
2,03 |
2,18 |
2,12 |
2,02 |
2,01 |
2,0 |
1,75 |
1,75 |
1,76 |
1,94 |
|
LC..A 30.. |
– |
– |
– |
– |
– |
– |
– |
– |
2,05 |
– |
|
LC..A 40.. |
3,50 |
3,90 |
3,80 |
4 |
4,11 |
3,8 |
3,13 |
3,04 |
– |
4,42 |
|
LC..B 00.. |
0,014 |
0,02 |
0,035 |
0,035 |
0,035 |
0,05 |
0,05 |
0,07 |
0,1 |
0,1 |
|
LC..B 05.. |
0,25 |
0,26 |
0,26 |
0,25 |
0,28 |
0,23 |
0,31 |
0,31 |
0,31 |
0,32 |
|
LC..B 10.. |
0,49 |
0,50 |
0,51 |
0,51 |
0,48 |
0,47 |
0,63 |
0,63 |
0,62 |
– |
|
LC..B 20.. |
1,44 |
1,62 |
1,52 |
1,44 |
1,5 |
1,5 |
1,26 |
1,25 |
1,25 |
1,4 |
|
LC..B 30.. |
– |
– |
– |
– |
– |
– |
– |
– |
1,45 |
– |
|
LC..B 40.. |
2,48 |
2,90 |
2,70 |
2,86 |
3,05 |
2,8 |
2,25 |
2,17 |
– |
3,35 |
|
Direction of flow B to A |
LC..A 00.. |
0,04 |
0,05 |
0,1 |
0,1 |
0,1 |
0,14 |
0,14 |
0,2 |
0,30 |
0,33 |
LC..A 05.. |
0,69 |
0,78 |
0,72 |
0,7 |
0,84 |
0,68 |
0,88 |
0,88 |
0,86 |
0,91 |
|
LC..A 10.. |
1,38 |
1,53 |
1,42 |
1,43 |
1,47 |
1,37 |
1,77 |
1,78 |
1,73 |
– |
|
LC..A 20.. |
4,05 |
4,91 |
4,25 |
4,06 |
4,57 |
4,33 |
3,53 |
3,54 |
3,50 |
3,9 |
|
LC..A 30.. |
– |
– |
– |
– |
– |
– |
– |
– |
4,0 |
– |
|
LC..A 40.. |
6,96 |
8,74 |
7,6 |
8,05 |
9,34 |
8,15 |
6,3 |
6,2 |
– |
8,76 |
|
LC..B 00.. |
0,24 |
0,25 |
0,5 |
0,5 |
0,5 |
0,8 |
0,7 |
1,0 |
1,5 |
1,5 |
|
LC..B 05.. |
3,69 |
3,40 |
3,64 |
3,64 |
3,95 |
3,27 |
4,2 |
4,6 |
4,4 |
4,6 |
|
LC..B 10.. |
7,43 |
6,69 |
7,24 |
7,37 |
6,88 |
6,62 |
8,4 |
9,4 |
8,9 |
– |
|
LC..B 20.. |
21,3 |
21,5 |
21,6 |
20,9 |
21,4 |
20,9 |
16,9 |
18,7 |
17,9 |
20 |
|
LC..B 30.. |
– |
– |
– |
– |
– |
– |
– |
– |
20,7 |
– |
|
LC..B 40.. |
36,6 |
38,3 |
38,6 |
41,5 |
43,6 |
39,4 |
30,2 |
32,5 |
– |
44,7 |
For applications outside these parameters, please consult us!
(simulated with HLP46, ϑoil = 40±5 °C)
Without damping nose "E", A → B




Without damping nose "E", B → A




With damping nose “D”, A → B




With damping nose "D", B → A




Notice:
The specified characteristic curves were simulated with 100% spool stroke and an aligned socket (see sketch under recommended socket alignment). The simulation results were validated by measurement results. The basis was an installation geometry with ØD3* (see installation under dimensions) and a simulation model according to ISO 4411/2008-10-01.
Recommended socket alignment:
Size 16...32
Bore on bore

Size 40 ... 160
Bar on bore

Version "E" |
Version “D” |
||
![]() |
![]() |
![]() |
![]() |
Area ratio A1 : A2 = 2 : 1 Version "…A.E…" |
Area ratio A1 : A2 = 14,3 : 1 Version "…B.E…" |
Area ratio A1 : A2 = 2 : 1 Version "…A.D…" |
Area ratio A1 : A2 = 14,3 : 1 Version "…B.D…" |
Additional functions with special numbers see "Information".
Installation bore according to ISO 7368
Dimensions in mm

1 |
Depth of fit |
2 |
Port B may be positioned around the central axis of port A. However, it must be observed that the mounting bores and the control bores are not damaged. |
NG |
16 | 25 | 32 | 40 | 50 | 63 | 80 | 100 | 125 | 160 | |
ØD1H7 |
mm |
32 | 45 | 60 | 75 | 90 | 120 | 145 | 180 | 225 | 300 |
ØD2 |
mm |
16 | 25 | 32 | 40 | 50 | 63 | 80 | 100 | 150 1) | 200 1) |
ØD3 |
mm |
16 | 25 | 32 | 40 | 50 | 63 | 80 | 100 | 125 | 160 |
(ØD3*) 2) |
mm |
25 | 32 | 40 | 50 | 63 | 80 | 100 | 125 | 160 | 250 |
ØD4H7 |
mm |
25 | 34 | 45 | 55 | 68 | 90 | 110 | 135 | 200 | 270 |
H1 |
mm |
42.5 | 57 | 68.5 | 84.5 | 97.5 | 127 | 170.5 | 205.5 | 255 | 368 |
H2 |
mm |
56 | 72 | 85 | 105 | 122 | 155 | 205 | 245 | 300 | 425 |
mm |
+ 0.1 | + 0.1 | + 0.1 | + 0.1 | + 0.1 | + 0.1 | + 0.1 | + 0.1 | + 0.15 | + 0.15 | |
H3 |
mm |
43 | 58 | 70 | 87 | 100 | 130 | 175 | 210 | 257 | 370 |
mm |
+ 0.2 | + 0.2 | + 0.2 | + 0.3 | + 0.3 | + 0.3 | + 0.4 | + 0.4 | + 0.5 | + 0.5 | |
H5 |
mm |
11 | 12 | 13 | 15 | 17 | 20 | 25 | 29 | 31 | 45 |
H6 |
mm |
2 | 2.5 | 2.5 | 3 | 3 | 4 | 5 | 5 | 7 | 8 |
mm |
- | - | - | - | - | - | - | - | ± 0.5 | ± 0.5 | |
H7 |
mm |
20 | 30 | 30 | 30 | 35 | 40 | 40 | 50 | 40 | 50 |
H8 |
mm |
2 | 2.5 | 2.5 | 3 | 4 | 4 | 5 | 5 | 5.5 | 5.5 |
mm |
- | - | - | - | - | - | - | - | ± 0.2 | ± 0.2 | |
W |
mm |
0.05 | 0.05 | 0.1 | 0.1 | 0.1 | 0.1 | 0.1 | 0.1 | 0.1 | 0.1 |
Ro 1) |
mm |
2 | 2 | 2 | 4 | 4 | 4 | 4 | 4 | 4 | 6.3 |
Ru 1) |
mm |
1 | 1 | 1 | 1 | 1 | 1 | 1 | 1 | 1 | 1 |
1) | Maximum dimension |
2) | Due to the use of a bore with ØD3*, port B protrudes over the upper limit of the area intended in ISO 7368. This is, however, possible due to the sealing concept and reduces the pressure loss during flow through the valve. Thus, we recommend a bore with ØD3*. |
Additional functions with special numbers (upon request)
Symbol |
Type (examples) |
Size |
Description / special characteristic |
![]() |
LC . A..D7X/-004 |
16 ... 50 |
With piston sealing (leakage-free) Larger spring installation space Special cover or intermediate cover "D19" required NG16 … 40: only with cracking pressure approx. 4 bar NG50 and 63: cracking pressure approx. 2 bar or higher; alternatively "without spring" |
LC . A..E7X/-004 |
16 ... 50 |
||
LC . B..E7X/-004 |
16 ... 63 |
||
![]() |
LC . A..D6X/-104 |
80, 100 |
With piston sealing (leakage-free) as SO-004, however, no special cover required |
LC . A..E6X/-104 |
80, 100 |
||
LC . B..E6X/-104 |
80, 100 |
||
LC . A..D7X/-104 |
40 … 63 |
||
LC . A..E7X/-104 |
40 … 63 |
||
LC . A..E2X/-104 |
125, 160 |
||
![]() |
LC . A05D6X/-054 |
16 |
Pulling logic with open zero position Special cover (e.g. "D54") required |
LC . A20D6X/-054 |
25 ... 32 |
||
LC . A05E6X/-054 |
16 |
||
LC . A..E6X/-054 |
25 ... 80 |
||
LC ./100 A20E6X/-054 |
32, 100 |
||
LC . B05E6X/-054 |
12 |
||
LC . B20E6X/-054 |
25 |
||
LC . A20D7X/-054 |
50 |
||
LC . A40D7X/-054 |
63 |
||
LC . A20E7X/-054 |
50 |
||
LC . A..E7X/-054 |
63 |
||
![]() |
LC …7X/-135 |
16 … 40 |
Larger spool clearance |
![]() |
LC …7X/-146 |
16 … 40 |
Larger spool clearance With piston sealing (leakage-free) Larger spring installation space Special cover or intermediate cover "D19" required |
![]() |
LC . A..D7X/-R10 |
16 |
As standard, however, larger bushing outer diameter D1 and D4 1 mm |
LC . A20D7X/-R10 |
25 |
||
LC 1. A40E7X/-R10 |
16, 32 |
||
LC . A..E7X/-R10 |
25, 63 |
||
LC . A10E7X/-R10 |
40 |
||
LC . A05E7X/-R10 |
50 |
||
LC . B..D7X/-R10 |
25 |
||
LC . B10D7X/-R10 |
32 |
||
LC . B40E7X/-R10 |
25, 40 |
||
LC . B..E7X/-R10 |
50, 63 |
||
![]() |
LC . A..D7X/-R20 |
16 |
As standard, however, larger bushing outer diameter D1 and D4 2 mm |
LC . A20D7X/-R20 |
25 |
||
LC 1. A40E7X/-R20 |
16, 32 |
||
LC . A..E7X/-R20 |
25, 63 |
||
LC . A10E7X/-R20 |
40 |
||
LC . A05E7X/-R20 |
50 |
||
LC . B..D7X/-R20 |
25 |
||
LC . B10D7X/-R20 |
32 |
||
LC . B40E7X/-R20 |
25, 40 |
||
LC . B..E7X/-R20 |
50, 63 |
||
![]() |
LC . XAB00E-7X/ |
16 … 63 |
Blind element without spool Channel A - B connected For use with available LFA cover or in connection with a cover "LFA . D-7X/FX99" |
![]() |
LC . XAF00E-7X/ |
16 … 63 |
Blind element without spool Channel A - F connected Channel B closed For use with available LFA cover or in connection with a cover "LFA . D-7X/FX99" |
![]() |
LC . X00E-7X/ |
16 … 63 |
Blind element without spool All channels blocked For use with available LFA cover or in connection with a cover "LFA . D-7X/FX99" |
Related Products
R978916694
$1,529.00 USD
R901116411
$5,489.00 USD
R978859364
$835.00 USD
R978850229
$898.00 USD
R900956113
$1,668.00 USD