***Disclaimer: The following summary contains information gathered from various sources such as product descriptions, technical specifications and catalogs. While efforts have been made to provide accurate details, inaccuracies may occur. It is advised to verify all information by contacting Bosch Rexroth directly.***
The Bosch Rexroth SL10GB3-4X/M (R900447726) is a high-quality isolator valve designed for subplate mounting or threaded connection, catering to the precise control needs of hydraulic systems. This releasable check valve is engineered to provide leak-free blocking of one actuator port, ensuring reliable operation even after extended periods of inactivity. The valve's construction includes a housing, seat poppet, compression spring, and a control spool, with an optional preopening feature as a ball seat valve.
The SL10GB3-4X/M allows fluid flow from A to B without external pilot pressure and closes hydraulically tight in the reverse direction when pA is greater than pB due to the cracking pressure of the compression spring. When pilot pressure at port X is adequately high, it moves the control spool towards version A's ball seat valve, dislodging the seat poppet and permitting free flow in both directions while actively keeping the valve open.
This model comes in two versions: Version A with preopening and Version B without preopening. Version A utilizes a two-stage setup with an increased control open ratio that ensures secure unloading even under low pilot pressures and mitigates switching shocks by dampened decompression. In contrast, Version B may experience sudden unloading of included pressure volume resulting in potential switching shocks that could cause wear on components and noise.
The SL10GB3-4X/M also features an optional built-on directional valve (Version U), which allows direct control over the opening of the seat poppet against system pressure. It provides various configuration options like different cracking pressures and attachment possibilities for directional spool valves or directional seat valves. The design incorporates corrosion protection and offers individual installation sets for check valves.
For installation flexibility, this model supports subplate mounting with porting patterns according to ISO standards NG6, NG10, and NG16 as well as threaded connections. Its maximum operating pressure reaches up to bar levels while handling maximum flow rates measured in liters per minute (l/min). The Bosch Rexroth SL10GB3-4X/M ensures efficient functionality for systems requiring precise hydraulic control with its robust design and versatile feature set.
$1,119.00 USD
More are expected on November 11, 2025
Qty | Price | Savings |
---|---|---|
5+ | $1,091.02 USD | $27.98 USD |
Status: This product is temporarily out of stock.
Qty: Delivered as early as November 11, 2025 when ordered in
This product is eligible for factory repair.
For subplate mounting Porting pattern according to ISO 5781-06-07-0-00 (NG10), ISO 5781-08-10-0-00 (NG20), ISO 5781-10-13-0-00 (NG32) For threaded connection For the leakage-free blocking of one actuator port Attachment possibility for directional spool valve or directional seat valve, optional Pilot oil return, external Version with pre-opening for dampened release, optional Various cracking pressures, optional Check valve installation sets available individually Corrosion-protected design
The isolator valve type SL is a releasable check valve for subplate mounting or threaded connection. It is used for the leakage-free blocking of one actuator port, also in case of longer standstill times.
The valve basically consists of a housing (1), a seat poppet (2), a compression spring (3), a control spool (4) as well as of an optional pre-opening as ball seat valve (5).
The seat valve can be flown through from A to B without external pilot pressure. In the opposite direction, the seat valve closes hydraulically tight.
Condition: pA > pB + cracking pressure (compression spring).
A sufficiently high pilot pressure at port X moves the control spool (4) in the direction of the ball seat valve (5) (version "A") and pushes the seat poppet (2) out of its seat. This allows for a free flow in both directions (active keeping open).
In order to ensure that the seat valve actively opens, the pressure ratios on both sides of the control spool (4) are just as important as the area ratios at the control spool (4) or seat poppet (2).
This results in the versions with pre-opening "A" and without pre-opening "B” for type SL (small annulus area). A4 (9).
Version "A" (with pre-opening)
This valve is provided with an additional pre-opening. By pressurization at the X port, the control spool (4) is moved to the right. As a result, the ball (5) is pushed off the seat first and the seat poppet (2) afterwards.
Notes:
Version "A”: The two-stage set-up with an increased control open ratio means even low pilot pressure can be unloaded securely. Avoidance of switching shocks due to dampened decompression of the pressure volume on the actuator side. Version "B”: In case of valves without pre-opening, the included pressure volume may be unloaded suddenly. Resulting switching shocks may lead to premature wear on installed components, as well as noise formation.Type SL..PB.-4X/... (with pilot oil return, without pre-opening)
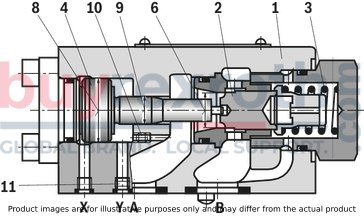
6 |
Area A1 (seat poppet) |
7 |
Area A2 (ball) |
8 |
AreaA 3 (control spool) |
9 |
Area A4 (control spool) |
Notice:
The modification of type SV to type SL is possible by exchange of plugs (10) and (11). One of the both plugs must always be installed.
NG |
Plug (10) |
Plug (11) |
10 |
M3 |
M6 |
20 |
M4 |
M6 |
30 |
M4 |
M6 |
Version "6U" (with built-on directional valve)
At direct operated, pilot operated check valves type SL with built-on directional valve, the control spool (4) may be controlled directly via the directional valve to open the seat poppet (2) against the system pressure, i.e. the blocking direction.
Notice:
When ordering the directional valve, please observe the different position of port A at versions "P" and "G" (porting pattern rotated by 180° at version "G", see "Dimensions").
Type SL..PB.-4X/6U... (with pilot oil return, without pre-opening)
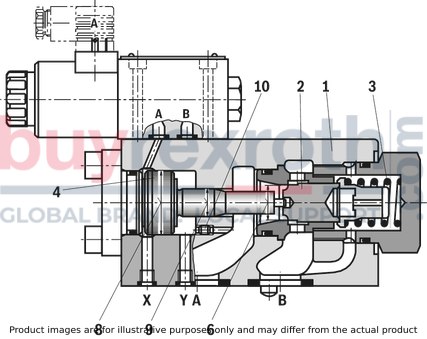
6 |
Area A1 (seat poppet) |
8 |
AreaA 3 (control spool) |
9 |
Area A4 (control spool) |
01 |
02 |
03 |
04 |
05 |
06 |
07 |
08 |
09 |
10 |
11 |
12 |
13 |
14 |
15 |
16 |
17 |
18 |
19 |
20 |
|||
S |
L |
– |
4X |
/ |
– |
* |
01 |
Check valve |
S |
02 |
Pilot oil return, external |
L |
03 |
Size 10 |
10 |
Size 20 |
20 |
|
Size 32 |
30 |
|
Type of connection |
||
04 |
Subplate mounting |
P |
Threaded connection |
G |
|
05 |
With pre-opening |
A |
Without pre-opening |
B |
|
Cracking pressure |
||
06 |
See characteristic curves (A → B) |
1 |
2 |
||
3 |
||
4 |
||
07 |
Component series 40 … 49 (40 … 49: unchanged installation and mounting dimensions) |
4X |
08 |
Without attachment possibility for directional spool or seat valve |
no code |
With attachment possibility for directional spool or seat valve (NG6) |
6U 1) |
|
Spool position monitoring |
||
09 |
Without position switch |
no code |
With position switch 2) |
QMG24 |
|
For more information see "Electrical connection" |
||
Orifice fitting channel A (version "6U" only) |
||
10 |
Orifice Ø0,8 mm in channel A (standard) |
A08 |
Orifice Ø** in channel A 3) |
A** |
|
Orifice fitting channel B (version "6U" only) |
||
11 |
Channel B closed (standard) |
B99 |
Orifice Ø** in channel B 3) |
B** |
|
Orifice fitting channel T (version "6U" only) |
||
12 |
Without orifice (standard) |
T00 |
Orifice Ø** in channel T 3) |
T** |
|
Orifice fitting channel P (version "6U" only) |
||
13 |
Without orifice (standard) |
P00 |
Orifice Ø** in channel P 3) |
P** |
|
Orifice fitting channel X (version "6U" only) |
||
14 |
Channel X closed (standard) |
X99 |
Orifice Ø** in channel X 3) |
X** |
|
Orifice fitting channel Y |
||
15 |
Channel Y open (standard) |
Y00 |
Orifice Ø** in channel Y 3) |
Y** |
|
Seal material |
||
16 |
NBR seals |
N |
FKM seals |
V |
|
Observe compatibility of seals with hydraulic fluid used. (Other seals upon request) |
||
Corrosion resistance |
||
17 |
None |
no code |
Improved corrosion protection (240 h salt spray test according to EN ISO 9227) |
J3 |
|
18 |
Standard |
no code |
Pilot pressure ppilot from channel X |
SO168 |
|
Control open spool with shaft sealing (between channel X–Y and Y–A) |
SO286 |
|
Connection thread (versions with threaded connection "G" only) |
||
19 |
Pipe thread "G" according to ISO 228-1 |
no code |
Pipe thread “UNF/UN” according to ANSI/ASME B 1.1 |
/12 |
|
20 |
Further details in the plain text |
* |
1) | Only size 20 and 32 |
2) | Only version "B3" |
3) | Order example: ** = dimension in mm x 10 – e.g. orifice Ø1,2 mm in channel Y = "Y12" |
general
Size |
10 | 20 | 32 | ||
Weight |
Subplate mounting |
kg |
1.8 | 4.7 | 7.8 |
Threaded connection |
kg |
2.1 | 5.4 | 10 | |
Installation position |
any | ||||
Ambient temperature range |
NBR seals |
°C |
-30 … +80 | ||
FKM seals |
°C |
-20 … +80 | |||
MTTFD values according to EN ISO 13849 1) |
Years |
150 | |||
Maximum storage time 2) |
Months |
12 |
1) | For further details, see data sheet 08012 |
2) | If the storage conditions are observed; refer to the operating instructions 07600-B |
hydraulic
Size |
10 | 20 | 32 | ||
Maximum operating pressure |
bar |
315 | |||
Cracking pressure |
bar |
1.5 / 3 / 6 / 10 | 2.5 / 5 / 7.5 / 10 | 2.5 / 5 / 8 / 10 | |
Minimum pilot pressure |
bar |
5 | |||
Maximum pilot pressure |
bar |
315 | |||
Maximum flow |
See characteristic curves | ||||
Direction of flow |
Free from A → B, from B → A by opening | ||||
Hydraulic fluid |
see table below | ||||
Hydraulic fluid temperature range |
NBR seals |
°C |
-30 … +80 | ||
FPM seals |
°C |
-20 … +80 | |||
Viscosity range |
mm²/s |
2.8 … 500 | |||
Maximum admissible degree of contamination of the hydraulic fluid, cleanliness class according to ISO 4406 (c) 1) |
Class 20/18/15 | ||||
Pilot volume |
Port X |
cm³ |
2.5 | 10.8 | 19.27 |
Port Y |
cm³ |
2 | 9.6 | 17.5 | |
Control area A1 2) |
cm² |
1.33 | 3.46 | 5.72 | |
Control area A2 2) |
cm² |
0.33 | 0.7 | 1.33 | |
Control area A3 2) |
cm² |
3.8 | 10.17 | 16.61 | |
Control area A4 2) |
cm² |
0.79 | 1.13 | 1.54 |
1) | The cleanliness classes specified for the components must be adhered to in hydraulic systems. Effective filtration prevents faults and simultaneously increases the life cycle of the components. For the selection of the filters, see www.boschrexroth.com/filter. |
2) | Areas according to sectional drawing, see "Product description" |
Hydraulic fluid |
Classification |
Suitable sealing materials |
Standards |
Data sheet |
|
Mineral oils |
HL, HLP, HLPD, HVLP, HVLPD |
NBR, FKM |
DIN 51524 |
90220 |
|
Bio-degradable |
Insoluble in water |
HETG 1) |
NBR, FKM |
ISO 15380 |
90221 |
HEES 1) |
FKM |
||||
Soluble in water |
HEPG 1) |
FKM |
ISO 15380 |
||
Flame-resistant |
Water-free |
HFDU (glycol base) |
FKM |
ISO 12922 |
90222 |
HFDU (ester base) 1) |
FKM |
||||
HFDR |
FKM |
||||
Containing water |
HFC (Fuchs Hydrotherm 46M, Petrofer Ultra Safe 620) 1) |
NBR |
ISO 12922 |
90223 |
|
Important information on hydraulic fluids: For more information and data on the use of other hydraulicfluids, please refer to the data sheets above or contact us. There may be limitations regarding the technical valve data (temperature, pressure range, life cycle, maintenance intervals, etc.). The ignition temperature of the hydraulic fluid used must be 50 K higher than the maximum surface temperature. Flame-resistant - containing water: Maximum pressure differential 210 bar, otherwise, increased cavitation erosion Life cycle as compared to operation with mineral oil HL, HLP 30 … 100%. Maximum hydraulic fluid temperature 60 °C Bio-degradable and flame-resistant – containing water: If this hydraulic fluid is used, small amounts of dissolved zinc may get into the hydraulic system. |
1) | Not recommended for corrosion-protected version "J3" (contains zinc) |
For applications outside these parameters, please consult us!
(measured with HLP46, ϑOil = 40 ±5 °C)
Subplate mounting
Δp-qV characteristic curves
Size 10

Δp-qV characteristic curves
Size 20
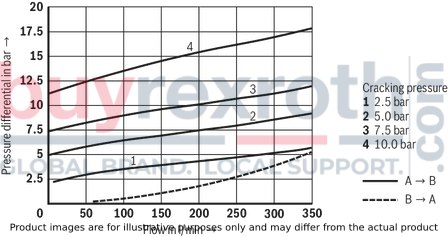
Δp-qV characteristic curves
Size 32

Pilot pressure/load pressure characteristic curves
Without pre-opening

Pilot pressure/load pressure characteristic curves
With pre-opening

Threaded connection
Δp-qV characteristic curves
Size 10

Δp-qV characteristic curves
Size 20

Δp-qV characteristic curves
Size 32

Pilot pressure/load pressure characteristic curves
Without pre-opening

Pilot pressure/load pressure characteristic curves
With pre-opening

Calculation of the pilot pressure pSt dependent on pA and pB
Version “A” (with pre-opening)
Balance of forces:


Version "B" (without pre-opening)
Balance of forces:

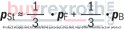
pA* |
Type-dependent (for type SL: pA* = 0) |
pSt |
Pilot pressure |
pA |
Working pressure in A |
pB |
Working pressure in B |
pF |
Cracking pressure (spring) |
A1 – A4 |
For areas see sectional drawing below "product description" and control area ratios below "technical data" |
Pilot oil return, external
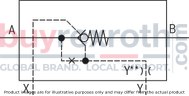
Version "SO168"
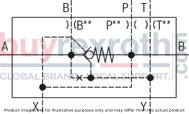
Version "SL …6U"
With directional spool valve type 4WE 6 D…
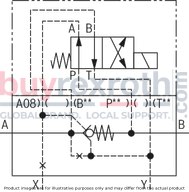
Version "SL …6U"
With directional spool valve type 4WE 6 Y…
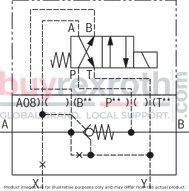
Version "SL …6U"
With directional seat valve type M-3SEW 6 C…
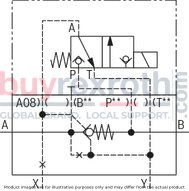
Version "SL …6U"
With directional seat valve type M-3SEW 6 U…
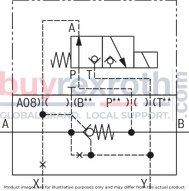
Circuit examples
Function: "Load locking"; inlet side unloading
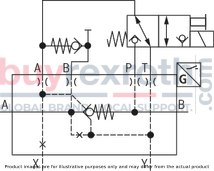
Function: Unlocking with external pilot pressure (version "SO168")

Inductive position switch type QM
The electrical connection is realized via a 4-pole mating connector (separate order, see "Accessories") with connection thread M12 x 1.
Connection voltage: |
24 V +30 %/-15 %, direct voltage |
|
Admissible residual ripple: |
≤ 10 % |
|
Load capacity: |
maximum 400 mA |
|
Switching outputs:![]() |
PNP transistor outputs, load between switching outputs and GND |
|
Pinout:![]() |
1 |
+24 V |
2 |
Switching output: 400 mA |
|
3 |
0 V, GND |
|
4 |
Switching output: 400 mA |
Switching logics
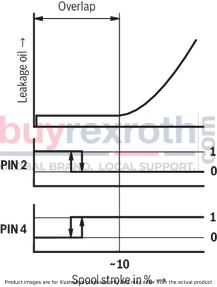
Subplate mounting

![]() |
Required surface quality of the valve contact surface |
1 |
Port Y open |
2 |
Name plate |
3 |
Locking pin |
4 |
Identical seal rings for ports A and B |
5 |
Valve with cracking pressure Version "1" and "2" (dimension L2) |
6 |
Valve with cracking pressure version "3" and "4" (dimension L3) |
7.1 |
6 valve mounting bores at NG32 |
8 |
Porting pattern according to ISO 5781 |
9 |
Version without position switch |
10 |
Version with position switch "QMG24" (circuitry see "Electrical connection") |
NG |
L1 |
L2 |
L3 |
L4 |
L5 |
L6 |
L7 |
L8 |
L9 |
L10 |
L11 |
L12 |
L13 |
L14 |
B1 |
B2 |
B3 |
B4 |
B5 |
B6 |
H1 |
H2 |
H3 |
mm |
mm |
mm |
mm |
mm |
mm |
mm |
mm |
mm |
mm |
mm |
mm |
mm |
mm |
mm |
mm |
mm |
mm |
mm |
mm |
mm |
mm |
mm |
|
10 | 100.8 | 15.5 | 15.5 | 87.8 | 13 | 42.9 | 18.5 | 7.2 | 35.8 | 21.5 | 21.5 | - | 31.8 | 105 | 84 | 66.7 | 44 | 58.8 | 7.9 | 33.3 | 51 | 29 | 36 |
20 | 135 | 17.7 | 47.7 | 117 | 18 | 60.3 | 27.5 | 11.1 | 49.2 | 39.5 | 20.6 | - | 44.5 | 96.5 | 100 | 79.4 | 67 | 73 | 6.4 | 39.7 | 81 | 45 | 55 |
32 | 156.1 | 36.1 | 46.1 | 134 | 22.1 | 84.2 | 39 | 16.7 | 67.5 | 59.5 | 24.6 | 42.1 | 62.7 | 117 | 118 | 96.8 | 75 | 92.8 | 3.8 | 48.4 | 85 | 42.5 | 70 |
Valve mounting screws (separate order)
Size |
Quantity |
Hexagon socket head cap screws |
Material number |
10 |
4 |
ISO 4762 - M10 x 50 - 10.9 Tightening torque MA = 75 Nm ±20 % |
- |
20 |
4 |
ISO 4762 - M10 x 70 - 10.9 Tightening torque MA = 75 Nm ±20 % |
- |
32 |
6 |
ISO 4762 - M10 x 85 - 10.9 Tightening torque MA = 75 Nm ±20 % |
- |
Notice:
The specified tightening torques were calculated with total friction coefficient μtotal = 0.09 ... 0.14; adjust in case of modified surfaces.
Subplates (separate order)
with porting pattern according to ISO 5781-06-07-0-00 (NG10), ISO 5781-08-10-0-00 (NG20), ISO 5781-10-13-0-00 (NG32) see data sheet 45100.
Threaded connection

1 |
Port Y open |
2 |
Name plate |
5 |
Valve with cracking pressure Version "1" and "2" (dimension L2) |
6 |
Valve with cracking pressure version "3" and "4" (dimension L3) |
7.2 |
2 valve mounting bores |
9 |
Version without position switch |
10 |
Version with position switch "QMG24" (circuitry see "Electrical connection") |
NG |
L1 |
L2 |
L3 |
L4 |
L5 |
L6 |
L7 |
L8 |
L9 |
L10 |
L11 |
B1 |
B2 |
B3 |
H1 |
H2 |
mm |
mm |
mm |
mm |
mm |
mm |
mm |
mm |
mm |
mm |
mm |
mm |
mm |
mm |
mm |
mm |
|
10 | 100.8 | 15.5 | 15.5 | 87.8 | 13 | 56.5 | 10.5 | 33.5 | 22.5 | 17.3 | 105 | 87 | 66.7 | 33.4 | 44 | 22 |
20 | 133 | 17.7 | 47.7 | 115 | 18 | 74.5 | 17 | 50.5 | 36 | 27 | 96.5 | 105 | 79.4 | 39.7 | 68 | 34 |
32 | 156.1 | 35.7 | 45.7 | 134 | 22.1 | 101 | 24 | 84 | 49 | 18 | 117 | 130 | 96.8 | 48.4 | 85 | 42.5 |
Ports
NG |
A |
B |
X |
Y |
"G" |
"UNF/UN" |
"G" |
"UNF/UN" |
|
10 | G1/2 | 3/4-16 UNF | G1/4 | 7/16-20 UN |
20 | G1 | 1 5/16-12 UN | G1/4 | 7/16-20 UN |
32 | G1 1/2 | 1 7/8-12 UN | G1/4 | 7/16-20 UN |
Valve mounting screws (separate order)
Size |
Quantity |
Hexagon socket head cap screws |
Material number |
10 |
2 |
ISO 4762 - M10 x 60 - 10.9 |
- |
20 |
2 |
ISO 4762 - M10 x 85 - 10.9 |
- |
32 |
2 |
ISO 4762 - M10 x 100 - 10.9 |
- |
Version "6U", subplate mounting
Dimensions in mm
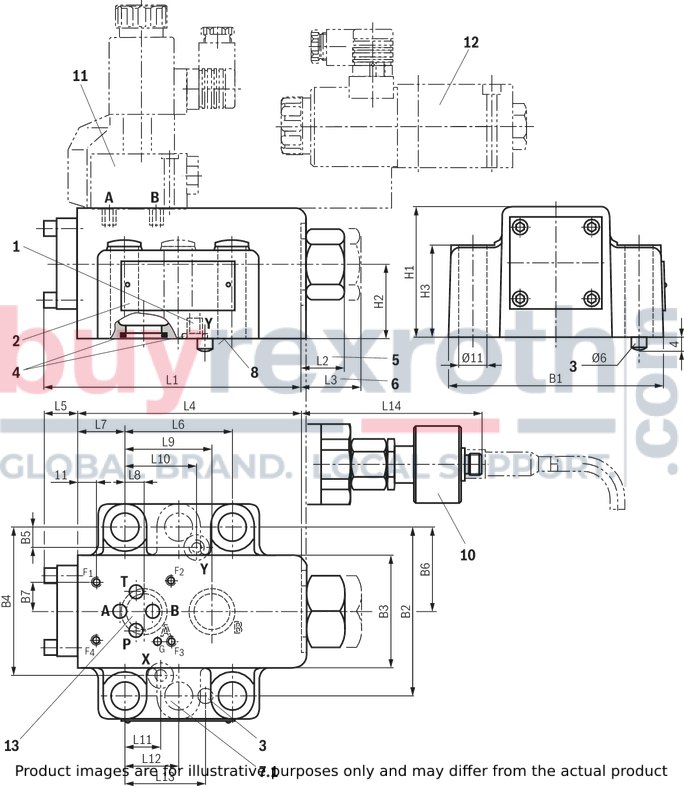
![]() |
Required surface quality of the valve contact surface |
1 |
Port Y open |
2 |
Name plate |
3 |
Locking pin |
4 |
Identical seal rings for ports A and B |
5 |
Valve with cracking pressure Version "1" and "2" (dimension L2) |
6 |
Valve with cracking pressure version "3" and "4" (dimension L3) |
7.1 |
6 valve mounting bores at NG32 |
8 |
Porting pattern according to ISO 5781 |
10 |
Version with position switch "QMG24" (circuitry see "Electrical connection") |
11 |
Directional seat valve type M-3SEW 6 ... (data sheet 22058) |
12 |
Directional spool valve type 4WE 6 ... (data sheet 23178) |
13 |
Porting pattern according to ISO 4401-03-02-0-05 |
NG |
L1 |
L2 |
L3 |
L4 |
L5 |
L6 |
L7 |
L8 |
L9 |
L10 |
L11 |
L12 |
L13 |
L14 |
B1 |
B2 |
B3 |
B4 |
B5 |
B6 |
B7 |
H1 |
H2 |
H3 |
mm |
mm |
mm |
mm |
mm |
mm |
mm |
mm |
mm |
mm |
mm |
mm |
mm |
mm |
mm |
mm |
mm |
mm |
mm |
mm |
mm |
mm |
mm |
mm |
|
20 | 135 | 17.7 | 47.7 | 117 | 18 | 60.3 | 27.5 | 11.1 | 49.2 | 39.7 | 20.6 | - | 44.5 | 96.5 | 100 | 79.4 | 61 | 73 | 6.4 | 39.7 | 11 | 81 | 45 | 55 |
32 | 156.1 | 36.1 | 46.1 | 134 | 22.1 | 84.2 | 39 | 16.7 | 67.5 | - | 24.6 | 42.1 | 62.7 | 117 | 118 | 96.8 | 75 | 92.8 | - | 48.4 | 11 | 85 | 42.5 | 70 |
Valve mounting screws (separate order)
Size |
Quantity |
Hexagon socket head cap screws |
Material number |
10 |
4 |
ISO 4762 - M10 x 50 - 10.9 Tightening torque MA = 75 Nm ±20 % |
- |
20 |
4 |
ISO 4762 - M10 x 70 - 10.9 Tightening torque MA = 75 Nm ±20 % |
- |
32 |
6 |
ISO 4762 - M10 x 85 - 10.9 Tightening torque MA = 75 Nm ±20 % |
- |
Notice:
The specified tightening torques were calculated with total friction coefficient μtotal = 0.09 ... 0.14; adjust in case of modified surfaces.
Subplates (separate order)
with porting pattern according to ISO 5781-06-07-0-00 (NG10), ISO 5781-08-10-0-00 (NG20), ISO 5781-10-13-0-00 (NG32) see data sheet 45100.
Version "6U", threaded connection
Dimensions in mm
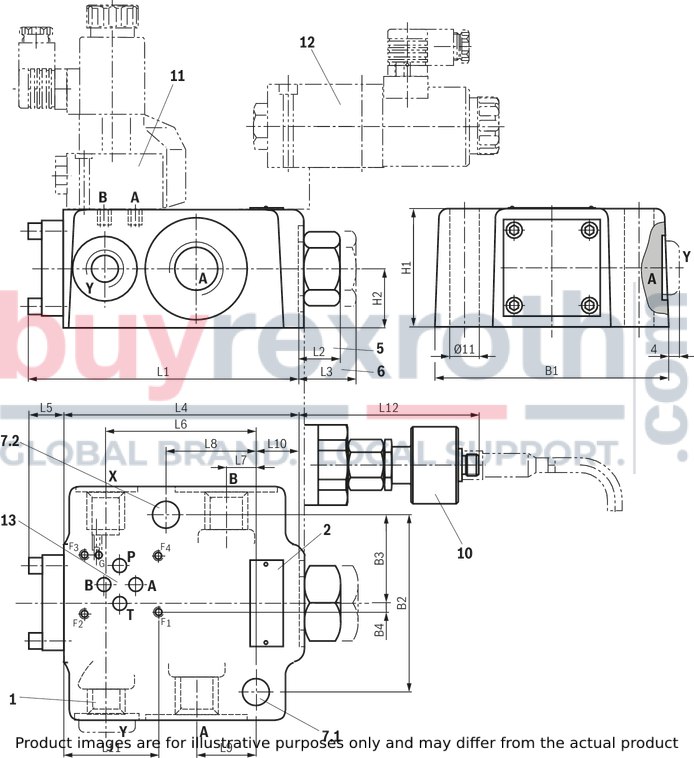
1 |
Port Y open |
2 |
Name plate |
5 |
Valve with cracking pressure Version "1" and "2" (dimension L2) |
6 |
Valve with cracking pressure version "3" and "4" (dimension L3) |
7.1 |
6 valve mounting bores at NG32 |
7.2 |
2 valve mounting bores |
10 |
Version with position switch "QMG24" (circuitry see "Electrical connection") |
11 |
Directional seat valve type M-3SEW 6 ... (data sheet 22058) |
12 |
Directional spool valve type 4WE 6 ... (data sheet 23178) |
13 |
Porting pattern according to ISO 4401-03-02-0-05 |
NG |
L1 |
L2 |
L3 |
L4 |
L5 |
L6 |
L7 |
L8 |
L9 |
L10 |
L11 |
L12 |
B1 |
B2 |
B3 |
B4 |
H1 |
H2 |
mm |
mm |
mm |
mm |
mm |
mm |
mm |
mm |
mm |
mm |
mm |
mm |
mm |
mm |
mm |
mm |
mm |
mm |
|
20 | 133 | 17.7 | 47.7 | 115 | 18 | 74.5 | 17 | 50.5 | 36 | 27 | 53 | 96.5 | 105 | 79.4 | 39.7 | 8.25 | 68 | 34 |
32 | 156.1 | 35.7 | 45.7 | 134 | 22.1 | 101 | 24 | 84 | 49 | 18 | 59 | 117 | 130 | 96.8 | 48.4 | 3.25 | 85 | 42.5 |
Ports
NG |
A |
B |
X |
Y |
"G" |
"UNF/UN" |
"G" |
"UNF/UN" |
|
20 | G1 | 1 5/16-12 UN | G1/4 | 7/16-20 UN |
32 | G1 1/2 | 1 7/8-12 UN | G1/4 | 7/16-20 UN |
Valve mounting screws (separate order)
Size |
Quantity |
Hexagon socket head cap screws |
Material number |
10 |
2 |
ISO 4762 - M10 x 60 - 10.9 |
- |
20 |
2 |
ISO 4762 - M10 x 85 - 10.9 |
- |
32 |
2 |
ISO 4762 - M10 x 100 - 10.9 |
- |
Connection adapter / reducing pieces
Material number |
Male thread |
Internal thread |
Seal (separate order) |
|
NBR |
FKM |
|||
R900173685 |
G1 |
G3/4 |
R900012475 |
R900012509 |
R900173689 |
G1 1/2 |
G1 1/4 |
R900012477 |
R900012511 |
Mating connectors for sensors and valves with connector “K24”, “K35” and “K72”, M12 x 1
4P Z24

Mating connectors for sensors and valves with connector “K24”, “K35” and “K72”, M12 x 1
4P Z24
For sensors and valves with connector “K24”, “K35” and “K72” Mating connectors M12, 4-pole, line cross-section 0.75 mm2Data sheet
Spare parts & repair
Mating connectors for sensors and valves with connector “K24”, “K35” and “K72”, M12 x 1, with assembled connection line
4P Z24 +
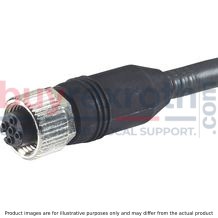
Mating connectors for sensors and valves with connector “K24”, “K35” and “K72”, M12 x 1, with assembled connection line
4P Z24 +
For sensors and valves with connector “K24”, “K35” and “K72” Mating connectors M12, 4-pole, line cross-section 0.75 mm2Data sheet
Spare parts & repair
Related Products
R900940564
$457.00 USD
R900926536
$1,882.00 USD
R900580052
$1,102.00 USD
R978018470
$379.00 USD
R978900419
$482.00 USD