***Disclaimer: The following summary contains information gathered from various sources such as product descriptions, technical specifications and catalogs. While efforts have been made to provide accurate details, inaccuracies may occur. It is advised to verify all information by contacting Bosch Rexroth directly.***
The Bosch Rexroth SYDFEN-2X/045R-PKC62KC1-0000-A0R0VXX (R978056641) is a state-of-the-art control system designed for the electrohydraulic control of axial piston variable displacement pumps. It enables precise control over swivel angle, pressure, and power, which can be partially optional depending on the type key pilot control and ordering code. The system includes a robust set of components: an axial piston variable displacement pump from the AVSO series, a VTDFPn.X proportional valve that serves as the pilot valve with integrated electronics, an inductive position transducer for accurate valve position sensing, and a swivel angle position sensor.
Furthermore, it features a pressure transducer that provides suitable signal level and dynamics for accurate pressure measurement; this may optionally be the HM version or ordered separately. The preload valve incorporated into the system has an integrated pressure relief function (SYDZ), which is optional. This version is compatible with axial piston variable displacement pumps from the AVSO series and supports various functions such as swivel angle control, pressure control, torque limitation, Master-Slave operation, and variable speed applications.
Communication with this system is versatile; it can interface through analog signals or CANopen for parameterizable options. It is engineered to work under maximum operating pressures stipulated by its design specifications. The SYDFEN-2X/045R-PKC62KC1-0000-A0R0VXX also includes integral electronics for streamlined operation and connectors for easy integration with additional sensors like the HM pressure transducer cable version only with actual pressure value input F or mating connector X for connecting to a CAN bus network available only with SYDFECSYDFEn models. The unit's drive shaft and connection flange are designed for reliability in various applications while offering options such as subplates with or without through-drive capabilities.
$10,730.00 USD
More are expected on January 21, 2026
Qty | Price | Savings |
---|---|---|
5-24 | $10,461.75 USD | $268.25 USD |
25+ | $10,193.50 USD | $536.50 USD |
Status: This product is temporarily out of stock.
Qty: Delivered as early as January 21, 2026 when ordered in
This product is eligible for factory repair.
A SYDFEn-2X control system is used for the electro-hydraulic control of swivel angle, pressure and power (partially optional, see type key pilot control and preload valve and ordering code) of an axial piston variable displacement pump.
The control system consists of the following components: Axial piston variable displacement pump A10VSO.../31 VT-DFPn-.2X proportional valve as pilot valve with integrated electronics including inductive position transducer for valve position sensing. Position transducer for sensing the swivel angle Pressure transducer with suitable signal level and dynamics (optionally HM 20, otherwise separate order) Preload valve with integrated pressure relief function SYDZ (optional)
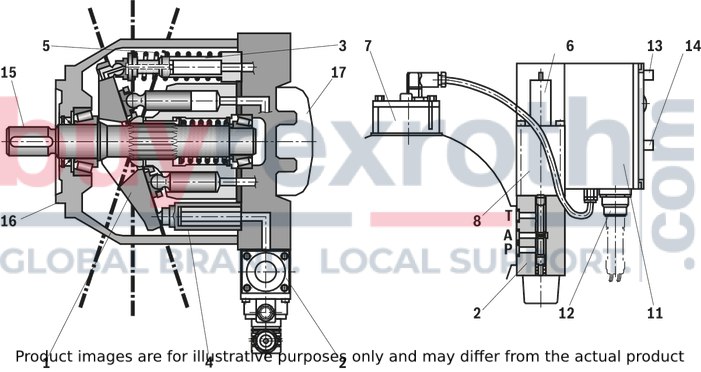
1 |
Swash plate |
2 |
Pilot valve |
3 |
Counter piston |
4 |
Actuating piston |
5 |
Spring |
6 |
Inductive position transducer for valve position |
7 |
Swivel angle position sensor |
8 |
Proportional solenoid |
11 |
Integral electronics |
12 |
Connector X1 |
13 |
Connector X2 for connection of the HM 20 pressure transducer cable version (only with actual pressure value input F) |
14 |
Mating connector X3 for connection of the CAN bus (only available with SYDFEC/SYDFEn) |
15 |
Drive shaft |
16 |
Connection flange |
17 |
Subplate, optionally with through-drive |
01 |
02 |
03 |
04 |
05 |
06 |
07 |
08 |
09 |
10 |
11 |
12 |
13 |
14 |
15 |
16 |
17 |
|||||
SYDFEn-2X |
/ |
– |
P |
12 |
– |
– |
0 |
– |
* |
Pump of the SYDFE control system |
|||||||||
Series |
|||||||||
01 |
Variable-speed control system with internal digital electronics |
SYDFEn-2X |
|||||||
Pump combinations (see order example) |
SY2DFE.-2X, |
||||||||
Size |
018 |
028 |
045 |
071 |
100 |
140 |
|||
02 |
Displacement cm³ |
18 |
28 |
45 |
71 |
100 |
140 |
||
Direction of rotation looking at the drive shaft |
|||||||||
03 |
Right |
● |
● |
● |
● |
● |
● |
R |
|
Left |
● |
● |
● |
● |
● |
● |
L |
||
Hydraulic fluid |
|||||||||
04 |
Mineral oil according to DIN 51524 (HL/HLP) |
● |
● |
● |
● |
● |
● |
P |
|
Drive shaft variant |
|||||||||
05 |
Cylindrical with fitting key DIN 6885 (not in connection with through-drive) |
Ø18 |
Ø22 |
Ø25 |
Ø32 |
Ø40 |
Ø45 |
P |
|
Splined shaft profile SAE J 744 1) |
3/4" |
– |
– |
– |
1 1/2" |
1 3/4" |
S |
||
Splined shaft profile SAE J 744 (higher torque) |
– |
7/8" |
1" |
1 1/4" |
– |
– |
R |
||
Connection flange (centering in mm) |
Ø18 |
Ø22 |
Ø25 |
Ø32 |
Ø40 |
Ø45 |
|||
06 |
ISO 2-hole |
80 |
100 |
100 |
125 |
125 |
– |
A |
|
ISO 4-hole |
– |
– |
– |
– |
– |
180 |
B |
||
SAE 2-hole |
82,55 |
101,6 |
101,6 |
127 |
127 |
– |
C |
||
SAE 4-hole |
– |
– |
– |
– |
– |
152,4 |
D |
||
Port for working lines pressure port B and suction port S |
|||||||||
07 |
SAE, laterally opposite, mounting thread metric |
● |
● |
● |
● |
● |
● |
12 |
|
Through-drive (All through-drives with single pumps come without a hub and are operationally safe, provided with an end cover) |
|||||||||
08 |
Without through-drive |
● |
● |
● |
● |
● |
● |
N00 |
|
Centering |
Attachment pump (examples) 2) |
||||||||
ISO Ø100 mm |
A10VSO..31 NG28/45 |
– |
● |
● |
● |
● |
● |
KD3 |
|
ISO Ø125 mm |
A10VSO..31 NG71/100 |
– |
– |
– |
● |
● |
● |
KD5 |
|
ISO Ø180 mm |
A10VSO..31 NG140 |
– |
– |
– |
– |
– |
● |
KD7 |
|
SAE Ø82.55 mm |
A10VSO..31 NG18, PGF2, PGH2, PGH3, AZPF |
● |
● |
● |
● |
● |
● |
KC1 |
|
SAE Ø101.6 mm |
PGH4, 1PF2G3, PGF3 |
– |
● |
● |
● |
● |
● |
KC3 |
|
SAE Ø127 mm |
PGH5 |
– |
– |
– |
● |
● |
● |
KC5 |
|
SAE Ø152.4 mm |
A10VO140 |
– |
– |
– |
– |
– |
● |
KC6 |
|
Base pump variant |
|||||||||
09 |
Standard (internal pilot oil) |
● |
● |
● |
● |
● |
● |
● |
0000 |
External supply |
– |
● |
● |
● |
● |
● |
– |
0479 |
|
External supply + regenerative operation |
– |
– |
– |
– |
● |
● |
● |
0487 |
|
Pilot and preload valve of the SYDFEn control system |
|||||||||
Spool design |
|||||||||
10 |
Standard (NG28 ... NG140) |
A |
|||||||
4-groove spool (NG18) |
C |
||||||||
Valve, installation orientation of integrated electronics, see comment on feature 11 |
|||||||||
11 |
Radially to the pump axis |
0 |
|||||||
folded 90° in the direction of the subplate |
2 |
||||||||
Additional functions |
|||||||||
12 |
Teach-in version for cyclic operation |
A |
|||||||
Real-time version (speed calculation without teach-in) |
R |
||||||||
Electronics assembly, options |
|||||||||
13 |
Standard |
0 |
|||||||
Actual pressure value input |
Plug-in connector |
C 4...20 mA |
V 0...10 V |
E 1...10 V |
F 0,5...5 V |
||||
14 |
Current input 4...20 mA |
X1 |
● |
C |
|||||
Voltage input 0...10 V |
X1 |
● |
V |
||||||
Voltage input 1...10 V |
X1 |
● |
E |
||||||
Voltage input 0.5...5 V 3) |
X2 |
● |
F |
||||||
Pressure transducer |
|||||||||
15 |
HM 20-2X/315-F-C13-0,5, measurement range 315 bar (0.5...5 V) with connection cable 0.5 m for direct connection to X2 (only in connection with actual pressure value input F) |
● |
L |
||||||
Without pressure transducer |
● |
● |
● |
● |
X |
||||
Preload valve with integrated pressure limitation |
|||||||||
16 |
Pressure limitation 200 bar (tolerance ± 8 bar) |
1 |
|||||||
Pressure limitation 250 bar (tolerance ± 10 bar) |
2 |
||||||||
Pressure limitation 300 bar (tolerance ± 12 bar) |
3 |
||||||||
Without preload valve |
X |
||||||||
17 |
Further details in the plain text e. g. SO variant |
* |
1) | ANSI B92.1a-1976, 30° pressure angle, flat root, side fit, tolerance class 5. |
2) | Also observe the conditions for the attachment pumps. |
3) | With the SYDFEn control system with the additional function (feature 12 of the ordering codes) "Teach-in version for cyclic operation" and with analog interfaces, the switching input X2 cannot always be used as an actual pressure value input. It depends on the configuration. Please observe the notices in the operating instructions 30014-b. |
Note on feature 11: Valve, installation orientation of the integrated electronics |
|||
Clockwise direction of rotation, installation orientation 0 |
Clockwise direction of rotation, installation orientation 2 |
Counterclockwise direction of rotation, installation orientation 0 |
Counterclockwise direction of rotation, installation orientation 2 |
![]() |
![]() |
![]() |
![]() |
● |
available |
- |
not available |
Ordering code pump combination SYHDFEn-2X
01 |
02 |
03 |
04 |
05 |
||||
SY2HDFEn-2X |
/ |
– |
/ |
+ |
01 |
2-fold pump |
SY2HDFEn-2X |
02 |
Size of the main pump 1) |
|
03 |
Size of the attachment pump or pump abbreviation if the attachment pump is not SYHDFE (e.g. PGF) 1) |
|
04 |
Material number without "R9" for the main pump or type designation if material number is not known |
|
05 |
Material number without "R9" for the attachment pump or type designation if material number is not known |
1) | Detailed information see type key |
01 |
02 |
03 |
04 |
|||
SY3HDFEn-2X |
/ |
+ |
+ |
01 |
3-fold pump |
SY3HDFEn-2X |
02 |
Material number without "R9" for the main pump or type designation if material number is not known |
|
03 |
Material number without "R9" for the attachment pump or type designation if material number is not known |
|
04 |
Material number without "R9" for the attachment pump or type designation if material number is not known |
Example of name plate of a pump combination
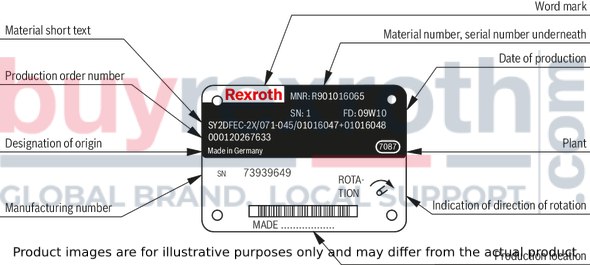
For enquiries regarding the control system, material number, production order number, serial number, and date of production are necessary.
Accessories |
Material number |
Data sheet |
Mating connector 12-pole for central connection X1 without cable (assembly kit) |
R900884671 |
08006 |
Mating connector 12-pole for central connection X1 with cable set 2 x 5 m |
R900032356 |
|
Mating connector 12-pole for central connection X1 with cable set 2 x 20 m |
R900860399 |
|
Pressure transducer HM 20-2X, measurement range 315 bar (4 ... 20 mA) |
R901342029 |
30272 |
Pressure transducer HM 20-2X, measurement range 315 bar (0.1 ... 10 V) |
R901342030 |
30272 |
Test device VT-PDFE-1-1X/V0/0 |
R900757051 |
29689-B |
Compact power supply unit VT-NE32-1X |
R90080049 |
29929 |
Converter USB serial for laptops without serial interface VT-ZKO-USB/S-1-1X/V0/0 |
R90106684 |
|
Converter USB/CAN Bus for the connection of a computer to a CAN Bus system |
R901071963 |
|
Cable for the connection of a Win-PED PC (RS232) at the interface X2, length 3 m |
R901156928 |
|
Cable for the connection of CAN bus/X3 at CAN bus converter (D-Sub) |
R901152127 |
|
T connector for the simultaneous connection of a WIN-PED PC (RS232) and use of the T connector for the simultaneous connection of a WIN-PED PC (RS232) and use of the pressure transducer at connector X2 |
R901117164 |
|
Mating connector for interface X3, M12, straight, can be connected independently, 5-pole, shielded, A coded, cable diameter 6 ... 8 mm |
R901076910 |
|
More accessories |
||
Accessories for through-drives |
See Accessories |
|
Torsionally flexible couplings for attachment to a standard electric motor |
See Accessories |
mechanic and hydraulic
Size |
18 | 28 | 45 | 71 | 100 | 140 | ||||
Displacement |
Vg max |
cm³ |
18 | 28 | 45 | 71 | 100 | 140 | ||
Speed 1) |
maximum at Vg max |
nnom |
rpm |
3300 | 3000 | 2600 | 2200 | 2000 | 1800 | |
maximum at Vg < Vg max |
nmax zul |
rpm |
3900 | 3600 | 3100 | 2600 | 2400 | 2100 | ||
Minimum speed |
nmin |
rpm |
50 | |||||||
Max. flow (displacement) |
at nnom and Vg max |
qV max |
l/min |
59.4 | 84 | 117 | 156 | 200 | 252 | |
with nE = 1500 rpm and Vg max |
qvE max |
l/min |
27 | 42 | 68 | 107 | 150 | 210 | ||
Max. power (Δp = 280 bar) |
at nnom and Vg max |
P max |
kW |
27.7 | 39 | 55 | 73 | 93 | 118 | |
with nE = 1500 rpm and Vg max |
PE max |
kW |
12.6 | 20 | 32 | 50 | 70 | 98 | ||
Max. torque (Δp = 280 bar) |
Tmax |
Nm |
80.1 | 125 | 200 | 316 | 445 | 623 | ||
Maximum permissible drive torque |
Fitting key |
Ttotal |
Nm |
88 | 137 | 200 | 439 | 857 | 1206 | |
Splined shaft S overall torque |
Ttotal |
Nm |
124 | - | 1104 | 1620 | ||||
Max. admissible through-drive torque |
TD |
Nm |
108 | - | 778 | 1266 | ||||
Splined shaft R overall torque |
Ttotal |
Nm |
- | 225 | 400 | 644 | - | |||
Max. admissible through-drive torque |
TD |
Nm |
- | 176 | 365 | 548 | - | |||
Drive shaft load |
![]() |
max. admissible axial force |
Fax max |
N |
700 | 1000 | 1500 | 2400 | 4000 | 4800 |
max. admissible radial force |
Fq |
N 2) |
350 | 1200 | 1500 | 1900 | 2300 | 2800 | ||
Weight |
Pump without through-drive incl. pilot valve |
m |
kg |
14 | 17 | 23 | 35 | 47 | 62 | |
in addition, preload valve |
m |
kg |
3.3 | 6.3 | ||||||
in addition, in case of external supply |
m |
kg |
2 | |||||||
Moment of inertia around drive axis |
kg·m² |
0.0009 | 0.0017 | 0.0033 | 0.0083 | 0.0167 | 0.0242 | |||
Filling quantity of the housing |
l |
0.4 | 0.7 | 1 | 1.6 | 2.2 | 3 | |||
Maximum admissible operating pressure 3) |
pmax |
bar |
280 | |||||||
Operating pressure, min. (without load) |
with preload valve |
pmin |
bar |
≥ 1 | ||||||
without preload valve |
pmin |
bar |
≥ 20 | |||||||
in case of external supply (20 bar) 4) |
pmin |
bar |
> 10 | |||||||
Admissible inlet pressure |
p |
bar |
0.8 ... 10 | |||||||
Hydraulic fluid |
Mineral oil (HL, HLP) to DIN 51524 | |||||||||
Hydraulic fluid temperature range |
ϑ |
°C |
-20 … +70 | |||||||
Maximum admissible degree of contamination of the hydraulic fluid according to ISO 4406 |
Class 18/16/13 (for particle size ≤ 4/6/14 μm) |
1) | The values are applicable at an absolute pressure of 1 bar at the suction opening S. With a reduction of the displacement or an increase in the inlet pressure, the speed can be increased according to the following characteristic curve. With a reduced inlet pressure, the speed is to be reduced. |
2) | In case of higher radial forces, please consult us |
3) | In case of higher pressures, please consult us |
4) | In continuous operation; in case of operation below 10 bar, observe the notes |
elektrisch
Operating voltage |
UB |
24 +40 % –5 % | ||
Operating range (short-time operation) |
Upper limit value |
UB(t)max |
V |
35 |
Lower limit value |
UB(t)min |
V |
21 | |
Current consumption (in static control operation) |
Rated current |
Inom |
A |
0.6 |
Maximum current |
Imax |
A |
1.25 | |
Inputs |
Actual pressure value input X1; |
U or I |
parameterizable: 0 ... 20 mA; 4 ... 20 mA; 0 ... 10 V; 0 … 5 V; 0.5 … 5 V; 0.1 ... 10 V; 1 ... 10 V | |
Analog current inputs, load 1) |
RB |
100 Ω | ||
Analog voltage inputs |
RE |
≥100 kΩ | ||
Digital inputs |
Logic 0 |
≤ 8 V | ||
Logic 1 |
≥ 14 V | |||
Outputs |
pactual / UOUT1 |
UO |
± 10 V | |
Imax |
2 mA | |||
αactual / UOUT2 |
UO |
± 10 V | ||
Imax |
2 mA | |||
Digital outputs |
Logic 0 |
Ua < 1 V | ||
Logic 1 |
Ua ≥ UB – 5 V; 10 mA (short-circuit-proof) | |||
Ambient temperature range at the pump |
ϑ |
°C |
0 … 50 | |
Storage temperature range (pump + electronics) |
ϑ |
°C |
0 … 70 | |
Electronics design |
Integrated in the pilot valve (OBE) | |||
Type of protection according to EN 60529 |
Pump incl. pilot valve |
IP65 with mounted and locked plug-in connectors |
1) | With configuration on current input: Maximum admissible input current 30 mA |
2) | With SYDFEC, SYDFEn and SYDFED, the outputs are parameterizable, for the condition as supplied, see electrical connection. |
Notice:
For information on the environment simulation testing for the areas of EMC (electro-magnetic compatibility), climate and mechanical load, see data sheet 30030-U.
Control loop quality
Notes:
The specified values are only valid when using the system-related components specified in this data sheet. At pressures < 20 bar, higher tolerances have to be anticipated due to lower actuating forces.
Swivel angle control |
Pressure control 1) |
|
Linearity tolerance |
≤ 1.0 % |
≤ 1.5 % (≤ 1.0 % 2)) |
Temperature error |
≤ 0.5 % / 10 K |
≤ 0.5 % / 10 K |
Hysteresis |
≤ 0.2 % |
≤ 0.2 % |
Repetition accuracy |
≤ 0.2 % |
≤ 0.2 % |
1) | Without considering the pump pulsation. |
2) | Using the integrated calibration function. |
For applications outside these parameters, please consult us!
Transition function with pressure command value step with spool design "A"
The specified curve shapes and control times refer to a drive speed of 1500 rpm and are only reached with an optimization of the pressure controller.
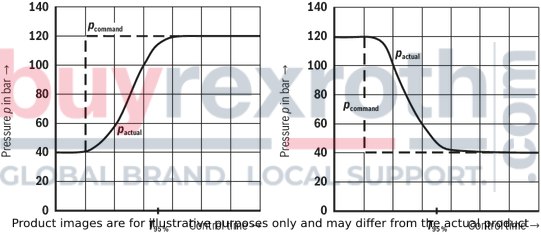
T 95% in ms with a connected hydraulic fluid volume (lines and actuators)
Hydraulic fluid volume in l |
T95% in ms |
< 5 |
150 |
5 ... 10 |
200 |
15 ... 15 |
250 |
Transition function with swivel angle command value step with spool design "A"
Size 18, 28, 45, 71 p = 20 bar

Size 18, 28, 45, 71 p = 50 bar

Size 100 p = 50 bar

Size 140 p = 50 bar

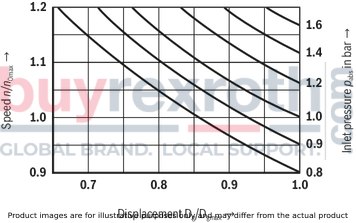
For pressures up to 40 bar, the values of the response times are greater.
Schematic diagram: Actuating system supplied internally

1) |
When using the pressure transducer HM 20 cable version: Installation in P (pump) or MP1 (preload valve) in connection with electronic version "Actual pressure value input F". When using an external pressure transducer: Installation in the P1 line (preferably close to the actuator) and electrical connection via the central connector. When using a preload valve, the pressure transducer is to be connected to P1 or MP1. |
Schematic diagram: Actuating system supplied externally
The representation shows an example with integrated electronics.
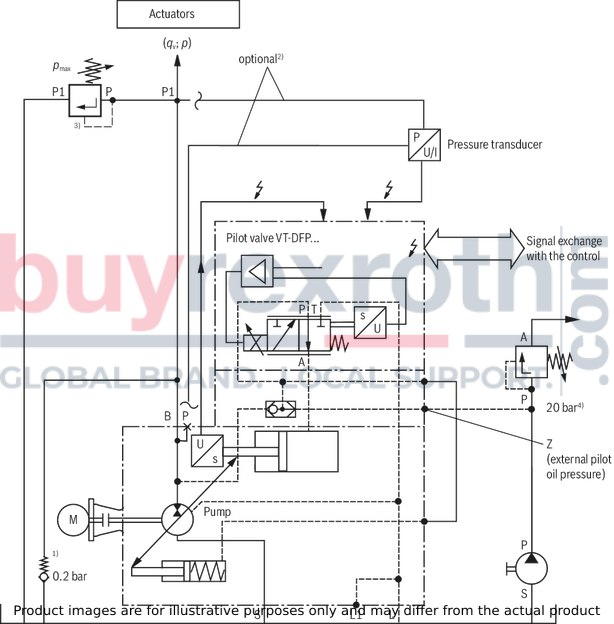
1) | The use of an anti-cavitation valve (check valve with 0.2 bar spring) is essential in order to prevent dry-running in the error case. |
2) |
Pressure transducer |
Mounting options |
Comment |
HM 20-2X/315-F-C13-0.5 (cable version) |
P |
Only in connection with actual pressure value input "F" |
|
HM 20-2X/...-.-K35 (connector version) |
P1 |
Preferably close to the actuator |
3) Maximum pressure limitation must be provided by the customer! | |
4) Observe upper limit for external pilot oil pressure! (see operating instructions), recommendation: 20 bar absolute. |
Important notes on external supply:
In the case of an actuating system with external supply, the pump adjustment will - in case of voltage failure - not switch to zero stroke but to the negative stop (displacement of 100 % flow from the system to the tank). With an active fault message, it is imperative that the machine control reacts (e. g. switching off the drive motor of the pump, interrupting the external supply of the actuating system). The command values for pressure and flow must always be greater than zero (pcommand ≥ 3 bar, αcommand ≥ 5 %) as due to drift or tolerances, there is no exact "zero" pressure or "zero" swivel angle. Under unfavorable conditions, smaller command value presettings can lead to cavitation. The actual pressure value must not be less than 10 bar for more than 10 minutes (lubrication).
Allocation of connector or mating connector and cable set
Pin |
Signal |
Description |
Signal direction |
Type of signal |
Allocation in the cable set (accessories) |
|
1 |
+ UB |
Voltage supply |
IN |
24 V DC |
1 |
Supply line 3 x 1.0 mm2 |
2 |
0 V = L0 |
Reference potential for the voltage supply |
– |
2 |
||
PE |
Earth |
Earthing connection for the electronics |
– |
green/yellow |
||
3 |
Fault |
Signals faults, e.g. cable break command / actual values, controller monitoring (logic 0 = error) |
OUT |
logic 24 V |
white |
Supply line 10 x 0.14 mm2 shielded (one end of the shield must be connected to the control!) |
4 |
M0 |
Reference potential for analog signals |
– |
yellow |
||
5 |
AI2 |
Analog input AI2 |
IN |
analog ±10 V |
green |
|
6 |
UOUT2 |
Analog output |
OUT |
analog ±10 V |
Violet |
|
7 |
AI1 |
Analog input AI1 |
IN |
analog 0...10 V |
pink |
|
8 |
UOUT1 |
Analog output |
OUT |
analog ±10 V |
red |
|
9 |
DI1 |
Digital input DI1 |
IN |
logic 24 V |
brown |
|
10 |
Actual pressure value H |
Actual pressure value input: Signal level depends on feature 14 of the ordering code |
IN |
analog |
black |
|
11 |
Actual pressure value L |
– |
analog |
blue |
||
n.c. |
gray |
X2: Serial interface RS232 and a switchable digital input/pressure transducer input for HM 20
HM 20-2X/315-F-C13-0,5 (cable version) (mating connector M12)
Pin |
Signal input |
Pin |
Signal CAN |
1 |
OUT, +UB |
2 |
RxD |
3 |
IN, digital IN2 (DI2) |
||
4 |
Analog input 0.5 ... 5 V for HM 20 or digital input 0 V low, 10 V high 1) Depending on additional function (feature 12 of the ordering code), Factory setting: ▶ Teach-in version: Digital input "Variable-speed operation on, S1" ▶ Real-time version: Input as analog input for pressure transducer HM 20 |
5 |
TxD |
1) | For valves with date of manufacture including 2013 max. 12 V. For valves after date of production 2014 max. UB. |
X3: CAN bus and digital input 2 (connector M12)
Pin |
Signal input |
Pin |
Signal CAN |
1 |
n.c. |
3 |
CAN GND |
2 |
IN, digital IN2 (DI2) Depending on additional function (feature 12 of the ordering code), Factory settings: ▶ Teach-in version: Start Teach-In, S2 ▶ Real-time version: Manual speed presetting active, speed is applied according to the real-time operation status and the setting of the R parameters. |
4 |
CAN-HIGH |
5 |
CAN-LOW |
installation orientation 0
The unit dimensions of the base pump (axial piston variable displacement pump A10VSO.../31) are contained in data sheet 92711.
Size 18 … 140
(Valve mounting direction "0"; shaft design "S”; without through-drive “N00”)
Dimensions in mm

(representation size 100)
Size |
Dimensions with base pump variant "0479" or "0487" |
Max. length |
|||||||||
A1 |
A3 1) |
A4 |
A5 |
A6 |
A6 I |
A6 II |
A8 I |
A8 II |
A8 III |
A9 |
|
mm |
mm |
mm |
mm |
mm |
mm |
mm |
mm |
mm |
mm |
mm |
|
18 | 120 | 198 | 158 | 63 | 178 | 63 | 115 | 233 | 125 | 100 | 170 |
28 | 128 | 208 | 158 | 63 | 195 | 80 | 115 | 243 | 135 | 115 | 194 |
45 | 134 | 218 | 158 | 63 | 205 | 90 | 115 | 253 | 145 | 125 | 219 |
71 | 146 | 232 | 158 | 63 | 254 | 104 | 150 | 267 | 159 | 150 | 257 |
100 | 151 | 237 | 158 | 63 | 247 | 100 | 147 | 272 | 164 | 150 | 317 |
140 | 162 | 250 | 143 | 78 | 257 | 110 | 147 | 285 | 182 | 150 | 317 |
1) | Dimension with base pump “0000” design |
installation orientation 2
Size 18 … 140
(Valve mounting direction "2"; shaft design "S”; without through-drive “N00”)
Dimensions in mm

(representation size 100)
Size |
Dimensions with base pump variant "0479" or "0487" |
Max. length |
|||||||||
A1 |
A3 |
A4 |
A5 |
A6 |
A6 I |
A6 II |
A8 I |
A8 II |
A8 III |
A9 |
|
mm |
mm |
mm |
mm |
mm |
mm |
mm |
mm |
mm |
mm |
mm |
|
18 | 100 | 116 | 158 | 63 | 178 | 63 | 115 | 151 | 125 | 100 | 253 |
28 | 108 | 127 | 158 | 63 | 195 | 80 | 115 | 162 | 135 | 115 | 263 |
45 | 114 | 137 | 158 | 63 | 205 | 90 | 115 | 172 | 145 | 125 | 278 |
71 | 126 | 151 | 158 | 63 | 254 | 104 | 150 | 186 | 159 | 150 | 306 |
100 | 131 | 156 | 158 | 63 | 247 | 100 | 147 | 191 | 164 | 150 | 373 |
140 | 142 | 180 | 143 | 78 | 257 | 110 | 147 | 215 | 182 | 150 | 373 |
Combination pumps

Attachment pump |
Main pump |
|||||||||||||||||||||||
A10VSO 18 |
A10VSO 28 |
A10VSO 45 |
A10VSO 71 |
A10VSO 100 |
A10VSO 140 |
|||||||||||||||||||
A1 |
A2 |
A3 |
A4 |
A1 |
A2 |
A3 |
A4 |
A1 |
A2 |
A3 |
A4 |
A1 |
A2 |
A3 |
A4 |
A1 |
A2 |
A3 |
A4 |
A1 |
A2 |
A3 |
A4 |
|
mm |
mm |
mm |
mm |
mm |
mm |
mm |
mm |
mm |
mm |
mm |
mm |
mm |
mm |
mm |
mm |
mm |
mm |
mm |
mm |
mm |
mm |
mm |
mm |
|
A10VSO 18 |
164 |
204 |
349 |
399 |
164 |
204 |
349 |
399 |
184 |
229 |
374 |
424 |
217 |
267 |
412 |
462 |
275 |
338 |
483 |
533 |
275 |
350 |
495 |
554 |
A10VSO 28 |
164 |
204 |
368.5 |
410 |
184 |
229 |
393.5 |
435 |
217 |
267 |
431.5 |
473 |
275 |
338 |
502.5 |
544 |
275 |
350 |
514 |
556 |
||||
A10VSO 45 |
184 |
229 |
413 |
453 |
217 |
267 |
451 |
491 |
275 |
338 |
522 |
562 |
275 |
350 |
534 |
574 |
||||||||
A10VSO 71 |
217 |
267 |
484 |
524 |
275 |
338 |
555 |
595 |
275 |
350 |
567 |
609 |
||||||||||||
A10VSO 100 |
275 |
338 |
613 |
664 |
275 |
350 |
625 |
679 |
||||||||||||||||
A10VSO 140 |
275 |
350 |
625 |
688 |
Ports
Size |
18 |
28 |
45 |
71 |
100 |
140 |
||
B: |
Working line (SAE J518) 1) |
|||||||
Size |
3/4" |
3/4" |
1" |
1" |
1 1/4" |
1 1/4" |
||
Mounting thread (DIN 13) |
M10 x 1.5; 17 deep |
M14 x 2; 19 deep |
||||||
Maximum pressure 2) |
bar |
350 |
||||||
S: |
Suction line (SAE J518) 1) |
|||||||
Size |
1" |
1 1/4" |
1 1/2" |
2" |
2 1/2" |
2 1/2" |
||
Mounting thread (DIN 13) |
M10 x 1.5; 17 deep |
M12 x 1.75; 20 deep |
M12 x 1.75; 17 deep |
|||||
Maximum pressure 2) |
bar |
10 |
1) | Dimensions according to SAE J518 only, metric mounting thread deviating from the standard. |
2) | Application-specific short-time pressure peaks may occur. Please observe when selecting measuring devices and fittings. Specified pressures are in bar absolute. |
Notes regarding size 71:
With pressure connection “B” of size 71, two SAE mounting connections rotated by 90° are available. SAE 1 1/4″ standard pressure series, 207 bar , for pressures up to 250 bar or SAE 1″ standard pressure series, 344 bar, for pressures up to 350 bar. For operating pressures exceeding 250 bar, the pressure flange SAE 1” must be used.Dimensions in mm

Hubs for through-drives
Hubs for the combination of single pumps or the combination of SYDFE with other pumps. Observe that the attachment pump has a splined shaft SAE J744 with the specified diameter.
The following conditions apply to the attachment pumps listed in the table:
SYDFE and A10VSO with shaft S or R Internal gear pump PGH with shaft R, flange U2, see data sheet 10223 Internal gear pump PGF3 with shaft J, flange U2, see data sheet 10213 External gear pump AZPF with shaft R, front cover R, see data sheet 10089Observe that the through-drive of the main pump and the flange of the attachment pump (see type key pump) are identical. Check in the current data sheet of the gear pump whether the shaft ends have the specified dimensions.
Main pump SYDFE or A10VSO... |
Attachment pump |
||||||
Size 18 |
Size 28 |
Size 45 |
Size 71 |
Size 100 |
Size 140 |
Ø shaft |
Pump type (examples) |
R902436099 |
R902436199 |
R902436100 |
R902436200 |
R902436201 |
R902436202 |
3/4" 19-4 (SAE A-B) |
SYDFE-2X, A10VSO..31 |
R902436098 |
R902436084 |
R902436083 |
R902436101 |
R902436102 |
7/8" 22-4 (SAE B) |
SYDFE-2X, A10VSO..31 |
|
R902436103 |
R902436104 |
R902436105 |
R902436204 |
1" 25-4 (SAE B-B) |
SYDFE-2X, A10VSO..31 |
||
R902436085 |
R902436105 |
R902436106 |
1 1/4" 32-4 (SAE C) |
SYDFE-2X, A10VSO..31 |
|||
R902436086 |
R910943555 |
1 1/2" 38-4 (SAE C-C) |
SYDFE-2X, A10VSO..31 |
||||
R910943565 |
R910932172 |
1 3/4" 44-4 (SAE D) |
SYDFE-2X, A10VSO..31 |
||||
R910943528 |
R910986299 |
R910943529 |
R91094345 |
R910943560 |
R910943551 |
5/8" 16-4 (SAE A) |
1PF2G2, PGF2, PGH2, PGH3, AZPF |
Through-drives
KD3
Flange ISO 100, 2-hole for the attachment of
SYDFE.-2X (size 28 and size 45, flange A) A10VSO..31 (size 28 and size 45, flange A, see data sheet 92711)
Sectional presentation with examples for hubs (order number for hubs see hubs for through-drives)
Dimensions in mm
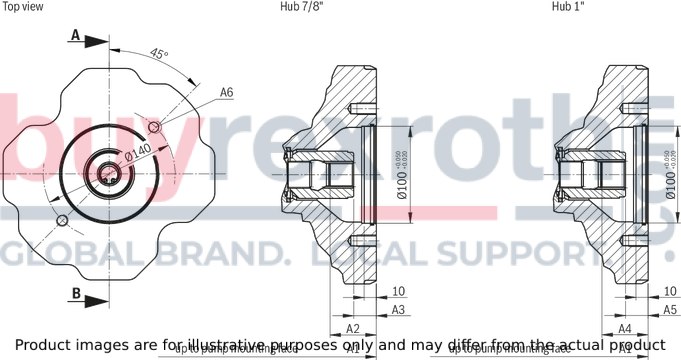
Size |
A1 |
A2 |
A3 |
A4 |
A5 |
A6 |
mm |
mm |
mm |
mm |
mm |
||
28 | 204 | 41.7 | 17.8 | - | - | M12; 15 right through |
45 | 229 | 41.7 | 17.9 | 46.7 | 18.4 | M12; 14 right through |
71 | 267 | 44.1 | 20.3 | 49.1 | 20.8 | M12; 20 deep |
100 | 338 | 41 | 17.6 | 45.9 | 18.2 | M12; 20 deep |
140 | 350 | 41.1 | 18 | 45.9 | 18.3 | M12; 20 deep |
KD5
Flange ISO 125, 2-hole for the attachment of
SYDFE.-2X (size 71 and size 100, flange A) A10VSO..31 (size 71 and size 100, flange A, see data sheet 92711)
Sectional presentation with examples for hubs (order number for hubs see hubs for through-drives)
Dimensions in mm

Size |
A1 |
A2 |
A3 |
A4 |
A5 |
A6 |
mm |
mm |
mm |
mm |
mm |
||
71 | 267 | 58.6 | 21.8 | - | - | M16; 20 right through |
100 | 338 | 56.4 | 19.5 | 63.9 | 7.9 | M16; 20 deep |
140 | 350 | 55.4 | 17.4 | 73.3 | 7.9 | M16; 20 deep |
KD7
Flange ISO 180, 4-hole for the attachment of
SYDFE.-2X (NG140, flange B) A10VSO..31 (NG140, flange B, see data sheet 92711)
Sectional presentation with examples for hubs (order number for hubs see hubs for through-drives)
Dimensions in mm

Size |
A1 |
A2 |
A3 |
A5 |
mm |
mm |
mm |
||
140 | 350 | 75 | 8 | M16; 22 right through |
KC1
Flange SAE 82-2 (SAE A, 2-hole) for the attachment of
SYDFE.-2X (size 18, flange C) A10VSO..31 (size 18, flange C, see data sheet 92711) PGF2 (shaft J, flange U2, see data sheet 10213) PGH2 and PGH3 (shaft R, flange U2, see data sheet 10223) AZPF (shaft R, front cover R, see data sheet 10089)
Sectional presentation with examples for hubs (order number for hubs see hubs for through-drives)
Dimensions in mm

Size |
A1 |
A2 |
A3 |
A4 |
mm |
mm |
mm |
||
18 | 182 | 40 | 43 | M10; 14.5 deep |
28 | 204 | 39 | 47 | M10; 16 deep |
45 | 229 | 40.5 | 53 | M10; 16 deep |
71 | 267 | 40 | 61 | M10; 20 deep |
100 | 338 | 40 | 65 | M10; 20 deep |
140 | 350 | 41 | 77 | M10; 17 deep |
KC3
Flange SAE 101-2 (SAE B, 2-hole) for the attachment of
SYDFE.-2X (size 28 and size 45, flange C) A10VO..31 (size 28 and size 45, flange C, see data sheet 92701) PGF3 (shaft J, flange U2, see data sheet 10213) PGH4 (shaft R, flange U2, see data sheet 10223)
Sectional presentation with examples for hubs (order number for hubs see hubs for through-drives)
Dimensions in mm
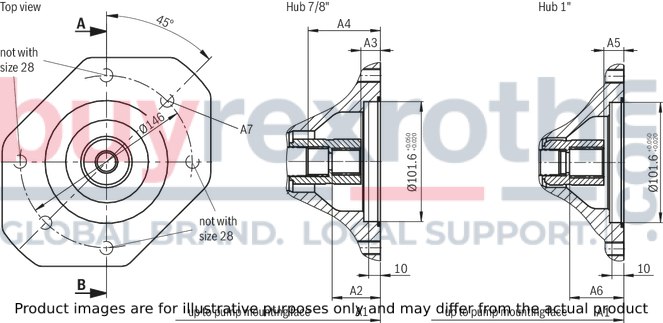
Size |
A1 |
A2 |
A3 |
A4 |
A5 |
A6 |
A7 |
mm |
mm |
mm |
mm |
mm |
mm |
||
28 | 204 | 43 | 16.5 | 47 | - | - | M12; 15 deep |
45 | 229 | 42 | 16.5 | 53 | 18.4 | 46.7 | M12; 18 deep |
71 | 267 | 43 | 16.5 | 61 | 20.8 | 49.1 | M12; 20 deep |
100 | 338 | 41 | 16.5 | 65 | 10.5 | 65 | M12; 20 deep |
140 | 350 | 44 | 16.5 | 77 | 18.3 | 45.9 | M12; 20 deep |
KC5
Flange SAE 127-2 (SAE C, 2-hole) for the attachment of
SYDFE.-2X (size 71 and size 100, flange C) A10VO..31 (size 71 and size 100, flange C, see data sheet 92701) PGH5 (shaft R, flange U2, see data sheet 10223)
Sectional presentation with examples for hubs (order number for hubs see hubs for through-drives)
Dimensions in mm
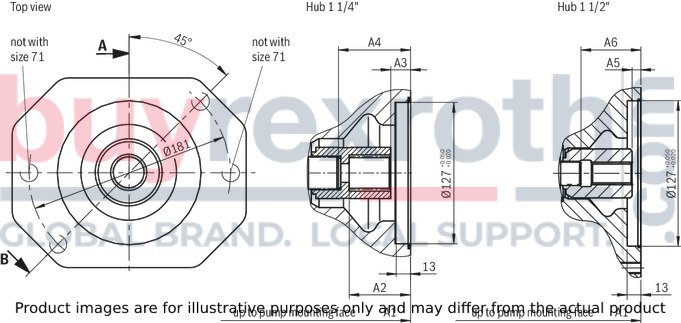
Size |
A1 |
A2 |
A3 |
A4 |
A5 |
A6 |
A7 |
mm |
mm |
mm |
mm |
mm |
mm |
||
71 | 267 | 55.5 | 17.9 | 61 | - | - | M16; 18 deep |
100 | 338 | 57 | 17.9 | 65 | 8 | 65 | M16; 25 deep |
140 | 350 | 60 | 17.9 | 77 | 9 | 77.3 | M16; 32 deep |
KC6
Flange SAE 152-4 (SAE D, 4-hole) for the attachment of
SYDFE.-2X (size 140, flange D) A10VO..31 (size 140, flange D, see data sheet 92701)
Sectional presentation with examples for hubs (order number for hubs see hubs for through-drives)
Dimensions in mm
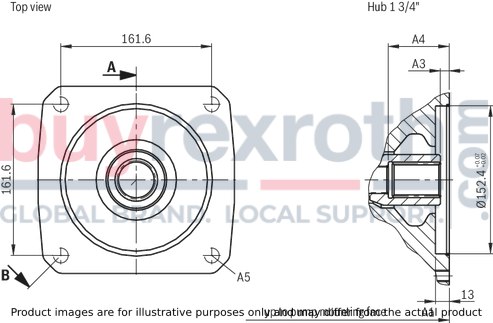
Size |
A1 |
A3 |
A4 |
A5 |
mm |
mm |
mm |
||
140 | 350 | 10.5 | 77 | M16; 24 deep |
Project planning information
Always shield command and actual value cables. The distance to aerial lines or radios must be at least 1 m. Do not lay signal lines close to power lines. For amending notes on the SYDFE control system, see the operating instructions (see section "More information about this control system").Torsionally flexible couplings for attachment to a standard electric motor
Motor |
SYDFE.-2X |
|||
Frame size/characteristic |
Shaft diameter |
NG18 Shaft S, 3/4” |
NG28 Shaft S or R, 7/8″ |
NG45 Shaft S or R, 1″ |
100/0 112/0 |
28 |
R901038012 |
R901038017 |
|
132/0 |
38 |
R900704699 |
R901012344 |
R900772898 |
160/0 |
42 |
R900726977 |
R900991864 |
R900994283 |
180/0 |
48 |
R900032918 |
R900062159 |
|
200/0 |
55 |
R901038026 |
R901038025 |
|
225/0 |
60 |
R900750847 |
R901066409 |
|
250/0 |
65 |
R900988348 |
Motor |
SYDFE.-2X |
|||
Frame size/characteristic |
Shaft diameter |
NG71 Shaft S or R, 1 1/4" |
NG100 Shaft S, 1 1/2" |
NG140 Shaft S, 1 3/4" |
160/0 |
42 |
R900228413 |
||
180/0 |
48 |
R900240468 |
R900242567 |
|
200/0 |
55 |
R901038021 |
R901104689 |
R901038048 |
225/0 |
60 |
R900228375 |
R901050508 |
R900988121 |
250/0 |
65 |
R900986404 |
R901046864 |
R900708084 |
280/0 |
75 |
R900218487 |
R901055216 |
R901052451 |
315/0 |
80 |
R9010468941) |
R9010468301) |
|
315/1 |
80 |
R901046885 |
1) | Up to 40 °C |
Accessories
Version 12/2014, enquire availability
Mating connectors for valves with round connector, 11-pole + PE
12P N11
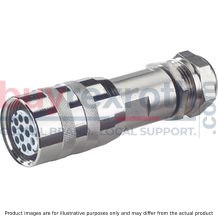
Mating connectors for valves with round connector, 11-pole + PE
12P N11
For valves with round connector according to EN 175201-804, 11-pole + PEData sheet
Spare parts & repair
Mating connectors for valves with round connector, 11-pole + PE, shielded, with assembled connection line
12P N11 +
Mating connectors for valves with round connector, 11-pole + PE, shielded, with assembled connection line
12P N11 +
For valves with round connector according to EN 175201-804, 11-pole + PEData sheet
Spare parts & repair
Related Products
R987097377
$7,895.00 USD
R978011794
$9,342.00 USD
R978056886
$11,700.00 USD
R901107129
$595.00 USD
R901017027
$68.00 USD