DIRECTIONAL SPOOL VALVE 4WE10Y5X/EG24N9K4/M
Manufacturer: Bosch Rexroth
Material #: R901278769
Model : 4WE10Y5X/EG24N9K4/M
***Disclaimer: The following summary contains information gathered from various sources such as product descriptions, technical specifications and catalogs. While efforts have been made to provide accurate details, inaccuracies may occur. It is advised to verify all information by contacting Bosch Rexroth directly.***
The Bosch Rexroth 4WE10Y5X/EG24N9K4/M (R901278769) is a high-performance industrial hydraulic valve designed for reliable control of oil flow direction in various applications. This direct-actuated spool valve features solenoid actuation with a maximum operating pressure capability and is equipped with a Size Y spool symbol for precise operation. The unit has an electrical connection conforming to EN standards, with a connector pole PE, ensuring secure and safe connections.
The valve is designed for subplate mounting and adheres to NFPA T3.5.1 R2 D03 size standards as well as CETOP D03 and ISO 4401 porting patterns, making it versatile for integration into different hydraulic systems. It operates with a supply voltage of 24 VDC and offers four switching positions, providing flexibility in controlling the flow paths.
With a weight of just , the 4WE10Y5X/EG24N9K4/M valve is relatively lightweight for its capabilities. It features NBR seals and is compatible with various hydraulic fluids including HL, HLP, HLPD, HVLP, HVLPD, and HFC types. The maximum flow rate supported by this valve ensures sufficient throughput for demanding applications.
Additionally, the Bosch Rexroth directional valve includes safety and efficiency features such as optional manual override functionality and considerations for energy-efficient operation when selecting models with detents that allow the control spool to be locked in position without continuous current application.
This product also meets CE conformity requirements according to the Low-Voltage Directive EC for specified electrical voltages and has UL approval (UL Recognized Component Mark) as well as optional CSA C22.2 No. approval, ensuring compliance with rigorous North American safety standards. The robust design of this solenoid-actuated directional spool valve ensures reliability in industrial settings where precise hydraulic control is essential.
$680.00 USD
Availability: 13 In Stock
Qty | Price | Savings |
---|---|---|
5-24 | $663.00 USD | $17.00 USD |
25+ | $646.00 USD | $34.00 USD |
Qty: Delivered as early as August 29, 2025 when ordered in
Qty: Delivered as early as September 22, 2025 when ordered in
This product is eligible for factory repair.
Size 10, symbol Y, solenoid-actuated, 24 V DC
Industrial hydraulic valve in a high performance range. Reliable switching of the oil flow direction according to hydraulic symbol.
Unpacked Weight: 3.998 kg
4/3-, 4/2- or 3/2-way version Porting pattern according to ISO 4401-05-04-0-05 High-power solenoid, optionally rotatable by 90° Electrical connection as individual or central connection Use optionally with PWM connector (fast switching amplifier, energy reduction) Optional auxiliary operating device CE conformity according to the Low-Voltage Directive 2006/95/EC for electrical voltages >50 VAC or > 75VDC Solenoid coil with UR approval UL 429 Approval according to CSA C22.2 no. 139-10, optional
The directional valve type WE is a solenoid-actuated directional spool valve that can be used as electro-magnetic component. It controls the start, stop and direction of a flow.
The directional valve basically consists of housing (1), one or two electronic solenoids (2), control spool (3), and the return springs (4).
In the de-energized condition, the control spool (3) is held in the central position or in the initial position by the return springs (4) (except for version "O").
If the wet-pin electronic solenoid (2) is energized, the control spool (3) moves out of its rest position into the required end position. In this way, the required direction of flow according to the selected symbol is released.
After the electronic solenoid (2) has been switched off, the control spool (3) is pushed back into its central position or into its initial position (except for valves with "OF" detent and valves without type "O" spring).
A manual override (6) allows for the manual switching of the valve without solenoid energization.
To ensure proper functioning, make sure that the pressure chamber of the solenoid is filled with oil.
For more functions, refer to the functional description.
Type .WE 10 E…
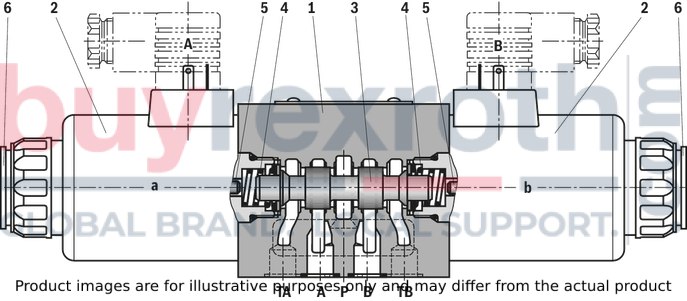
Throttle insert "B.."
Using a throttle insert (7) in channels P, A, B or T, the flow resistance at the valve can be increased. Its use is required when, due to prevailing operating conditions, flows occur during the switching processes, which exceed the performance limit of the valve.
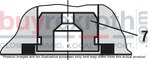
Without spring return “O” (only possible with symbols A, C and D)
This version is a directional valve with 2 spool positions and 2 electronic solenoids without detent. The valve without spring return at the control spool (3) does not have a defined basic position in the de-energized condition.
Without spring return with detent “OF” (only possible with symbols A, C and D)
This version is a directional valve with 2 spool positions and 2 electronic solenoids with detent. The detents are used to lock the control spool (3) in the relevant spool position. During operation, continuous application of current to the electronic solenoid can thus be omitted which contributes to energy-efficient operation.
Notice!
Pressure peaks in the tank line to two or several valves can result in unwanted movements of the control spool in the case of valves with detent! We therefore recommend that separate return lines be provided or a check valve installed in the tank line.
Type .WE 10 ../OF…

Spool valve |
Direct actuated |
Component series 5X |
Maximum flow 160 l/min |
Size 10 |
Maximum operating pressure 350 bar |
Data Sheet | Download Data Sheet |
3D CAD | Download 3D CAD |
Manual | Download Manual |
Manual | Download Manual |
Manual | Download Manual |
Manual | Download Manual |
Spool symbol | Symbol Y |
Max. pressure | 350 |
Electrical connection description | Connector 3-pole (2 + PE) according to EN 175301-803 |
Productgroup ID | 9,10,11,12,13,14 |
Number of ports | 4 |
Type of actuation | with solenoid actuation |
Size | 10 |
Electrical connector | Connector 3-pole (2 + PE) |
Max. flow | 90 |
Type of connection | Subplate mounting |
Connection diagram NFPA | NFPA T3.5.1 R2-2002 D05 |
Size_CETOP | D05 |
Connection diagram | ISO 4401-05-04-0-05 |
Supply voltage | 24 VDC |
Number of switching positions | 2 |
Weight | 3.998 |
Seals | NBR |
Hydraulic fluid | HL,HLP,HLPD,HVLP,HVLPD,HFC |
Hydraulic fluid | HL,HLP,HLPD,HVLP,HVLPD,HFC |
01 |
02 |
03 |
04 |
05 |
06 |
07 |
08 |
09 |
10 |
11 |
12 |
13 |
14 |
15 |
16 |
17 |
||
WE |
10 |
5X |
/ |
E |
/ |
* |
01 |
3 main ports |
3 |
||
4 main ports |
4 |
|||
02 |
Directional valve |
WE |
||
03 |
Size 10 |
10 |
||
04 |
Symbols e. g. C, E, EA, EB, etc.; for the possible version, see Symbols |
z. B. C |
||
05 |
Component series 50 … 59 (50 … 59: unchanged installation and connection dimensions) |
5X |
||
06 |
With spring return |
no code |
||
With reinforced compression spring |
D |
|||
Without spring return |
O |
|||
Without spring return with detent |
OF |
|||
07 |
High-power solenoid, wet-pin, with detachable coil |
E |
||
08 |
Direct voltage 12 V |
G12 |
||
Direct voltage 24 V |
G24 |
|||
Direct voltage 26 V |
G26 |
|||
Direct voltage 48 V |
G48 |
|||
Nominal voltage 96 V at DC solenoid in operation with AC voltage mains (AC voltage mains 100/110 V - 50/60 Hz with an admissible voltage tolerance of +/- 10 %) |
G96 |
|||
Direct voltage 110 V |
G1101) |
|||
Direct voltage 125 V |
G125 |
|||
Nominal voltage 180 V at DC solenoid in operation with AC voltage (AC voltage mains 200 V - 50/60 Hz with an admissible voltage tolerance of +/- 10 %) |
G180 |
|||
Nominal voltage 205 V at DC solenoid with operation with AC voltage mains (AC voltage mains 230 V – 50/60 Hz with an admissible voltage tolerance of +/- 10 %) |
G205 |
|||
Direct voltage 220 V |
G220 |
|||
Alternating voltage 100 V |
W100R1) |
|||
Alternating voltage 110 V |
W110R1) |
|||
Alternating voltage 120 V |
W120R1) |
|||
Alternating voltage 200 V |
W200R1) |
|||
Alternating voltage 230 V |
W230R1) |
|||
Connection to AC voltage mains via control with rectifier (see table Mating connectors) 2) |
||||
Electrical connections and available voltages see Technical data |
||||
09 |
Without manual override |
no code |
||
With concealed manual override (standard) |
N93) |
|||
With concealed manual override and protective cap 5) |
N83) |
|||
With lockable manual override "mushroom button" (large) |
N53; 4) |
|||
With manual override "mushroom button" (large), not lockable |
N63) |
|||
Corrosion resistance (outside) |
||||
10 |
None (valve housing primed) |
no code |
||
Improved corrosion protection (240 h salt spray test according to EN ISO 9227) (see also Technical data) |
J3 |
|||
Electrical connection |
||||
11 |
Individual connection |
|||
Without mating connector; connector DIN EN 175301-803 |
K46) |
|||
Without mating connector; connector DIN EN 175301-803 (coil with potted-in connector base and sealing element to valve housing (IP67)) |
K4K6) 7) |
|||
Without mating connector, 4-pole with connector M12 x 1 according to IEC 60947-5-2, integrated interference protection circuit and status LED |
K72L 6) |
|||
Without mating connector; connector AMP Junior-Timer |
C4Z6) |
|||
Central connection |
||||
Cable entry at the cover, with indicator light |
DL |
|||
Central plug-in connection at the cover, with indicator light (without mating connector); connector according to DIN EN 175201-804 |
DK6L |
|||
Without mating connector; threaded connection 1/2“-14 NPT |
DAL |
|||
Cable gland at the cover, with indicator light and cable bridge at the ground connection |
DJL |
|||
Mini-charge connector, 5-pole |
DK25L |
|||
For further electrical connections and available voltages, see Technical data |
||||
Switching time increase |
||||
12 |
Without switching time increase |
no code |
||
With switching time increase (only with symbol ".73"; not for version "D" with reinforced compression spring; more information upon request) |
A12 |
|||
13 |
Without throttle insert |
no code |
||
With throttle insert 8; 9); |
||||
Connection |
Throttle Ø in mm |
|||
0,8 mm |
1,0 mm |
1,2 mm |
||
P |
B08 |
B10 |
B12 |
|
A |
H08 |
H10 |
H12 |
|
B |
R08 |
R10 |
R12 |
|
A and B |
N08 |
N10 |
N12 |
|
T 10) |
X08 |
X10 |
X12 |
|
Further throttle insert diameters upon request. |
||||
Control spool play |
||||
14 |
Standard |
no code |
||
Minimum (to be selected in case of reduced leakage → higher level of oil cleanliness recommended) |
T06 |
|||
Increased (to be selected in case of a hydraulic fluid/environment temperature difference >25 K → increased internal leakage) |
T12 |
|||
Seal material |
||||
15 |
NBR seals |
M |
||
FKM seals |
V |
|||
Seals for HFC hydraulic fluids |
MH |
|||
Low-temperature version |
MT |
|||
Observe compatibility of seals with hydraulic fluid used. |
||||
16 |
Approval according to CSA C22.2 no. 139-10 |
CSA |
||
Porting pattern according to ANSI B93.9 (if solenoid "a" is energized, channel P is connected to A) |
AN |
|||
17 |
Further details in the plain text |
* |
1) Only for “central connection” version | |
2) Only for “individual connection” version | |
3) The manual override cannot be allocated a safety function. The manual override units may only be used up to a tank pressure of 50 bar. | |
4) With tank pressures above 50 bar, it cannot be guaranteed that the valve remains in the position switched by the manual override "N5". | |
5) Protective cap must be removed prior to actuation. | |
6) Mating connectors, separate order, see Mating connectors and data sheet 08006. | |
7) Recommended for mobile applications; with additional sealing between solenoid coil and pole tube. | |
8) When the admissible valve performance limit is exceeded, throttle inserts are to be installed (see Performance limits). | |
9) Not with low-temperature version "MT". | |
10) When throttle inserts are used in channel T, the pressure in the working ports and in case of connection to the tank chambers must not exceed 210 bar. |
Notice:
For directional spool valves NG10 with spool position monitoring, see data sheet 23352.
For applications outside these parameters, please consult us!
general
Size |
10 | 10 | ||||||||
Type |
Einzelanschluss | Zentralanschluss | Einzelanschluss | Zentralanschluss | Einzelanschluss | Zentralanschluss | ||||
Weight |
Valve with one solenoid |
kg |
3.9 | 4 | 3.9 | 4 | 3.9 | 4 | ||
Valve with two solenoids |
kg |
5.5 | 5.6 | 5.5 | 5.6 | 5.5 | 5.6 | |||
Installation position 1) |
any | any | ||||||||
Ambient temperature range |
NBR seals |
°C |
-20 … +70 | -20 … +70 | ||||||
FKM seals |
°C |
-15 … +70 | -15 … +70 | |||||||
HFC hydraulic fluid 2) |
°C |
-20 … +50 | -20 … +50 | |||||||
Low-temperature version |
°C |
-40 … +50 | -40 … +50 | |||||||
Storage temperature range |
°C |
-20 … +50 | -20 … +50 | |||||||
MTTFD values according to EN ISO 13849 3) |
Years |
300 | 300 |
1) | With suspended installation, higher sensitivity to contamination. Horizontal installation is recommended. |
2) | For the use at low temperatures, see Project planning information |
3) | For further details, see data sheet 08012 |
hydraulic
Size |
10 | ||
Maximum operating pressure |
Port P |
bar |
350 |
Port A |
bar |
350 | |
Port B |
bar |
350 | |
Port T 1) |
bar |
210 | |
Maximum flow |
l/min |
160 | |
Flow cross-section (spool position 0) |
Symbol Q |
approx. 6 % of nominal cross-section | |
Symbol W |
approx. 3 % of nominal cross-section | ||
Hydraulic fluid |
see table | ||
Hydraulic fluid temperature range 2) |
NBR seals |
°C |
-20 … +80 |
FKM seals |
°C |
-15 … +80 | |
HFC hydraulic fluid |
°C |
-20 … +50 | |
Low-temperature version |
°C |
-40 … +50 | |
Viscosity range |
mm²/s |
2.8 … 500 | |
Maximum admissible degree of contamination of the hydraulic fluid 3) |
Class 20/18/15 according to ISO 4406 (c) |
1) | With symbols A and B, port T must be used as leakage oil connection if the operating pressure exceeds the admissible tank pressure. |
2) | at the valve working ports of the valve |
3) | The cleanliness classes specified for the components must be adhered to in hydraulic systems. Effective filtration prevents faults and simultaneously increases the life cycle of the components. For the selection of the filters, see www.boschrexroth.com/filter. |
Hydraulic fluid |
Classification |
Suitable sealing materials |
Standards |
Data sheet |
|
Mineral oils |
HL, HLP, HLPD, HVLP, HVLPD |
NBR, FKM |
DIN 51524 |
90220 |
|
Bio-degradable |
Insoluble in water |
HETG |
NBR, FKM |
ISO 15380 |
90221 |
HEES |
FKM |
||||
Soluble in water |
HEPG |
FKM |
ISO 15380 |
||
Containing water |
Water-free |
HFDU, HFDR |
FKM |
ISO 12922 |
90222 |
Containing water |
HFC (Fuchs Hydrotherm 46M, Petrofer Ultra Safe 620 ) |
NBR |
ISO 12922 |
90223 |
|
Important information on hydraulic fluids: For further information and data on the use of other hydraulic fluids, please refer to the data sheets above or contact us. There may be limitations regarding the technical valve data (temperature, pressure range, life cycle, maintenance intervals, etc.). The ignition temperature of the hydraulic fluid used must be 40 K higher than the maximum solenoid surface temperature.Flame-resistant – containing water: Maximum pressure differential per control edge 50 bar. Pressure pre-loading at the tank port >20% of the pressure differential; otherwise, increased cavitation Life cycle compared to operation with mineral oil HL, HLP 50 to 100 %Bio-degradable and flame-resistant: When using hydraulic fluids that are simultaneously zinc-solving, zinc may accumulate (700 mg zinc per pole tube). |
electrical
Voltage type |
Direct voltage | AC voltage | Direct voltage | AC voltage | Direct voltage | AC voltage | ||||
Nominal voltage according to VDE 0580 |
V |
12 24 26 48 96 110 125 180 205 220 |
100 1) 110 1) 120 1) 200 1) 230 1) |
12 24 26 48 96 110 125 180 205 220 |
100 1) 110 1) 120 1) 200 1) 230 1) |
12 24 26 48 96 110 125 180 205 220 |
100 1) 110 1) 120 1) 200 1) 230 1) |
|||
Voltage tolerance (nominal voltage) |
% |
± 10 | ± 10 | |||||||
Nominal power according to VDE 0580 |
W |
40 2) | 40 | 40 2) | 40 | 40 2) | 40 | |||
Duty cycle |
% |
100 3) | 100 3) | |||||||
Switching time |
ON (pressure change 5 %) |
ms |
60 … 104 4) | 60 … 104 4) | ||||||
ON (pressure change 95 %) |
ms |
90 … 165 4) | 90 … 165 4) | |||||||
OFF (pressure change 5 %) |
ms |
12 … 50 5) | 230 … 330 5) | 12 … 50 5) | 230 … 330 5) | 12 … 50 5) | 230 … 330 5) | |||
OFF (pressure change 95 %) |
ms |
48 … 104 5) | 250 … 360 5) | 48 … 104 5) | 250 … 360 5) | 48 … 104 5) | 250 … 360 5) | |||
Switching time according to ISO 6403 |
ON |
ms |
45 … 60 6) | 45 … 60 6) | ||||||
OFF |
ms |
20 … 30 6) | 250 … 360 6) | 20 … 30 6) | 250 … 360 6) | 20 … 30 6) | 250 … 360 6) | |||
Maximum switching frequency |
1/h |
15000 | 7200 | 15000 | 7200 | 15000 | 7200 | |||
Maximum surface temperature of the coil |
°C |
140 7) | 140 7) | |||||||
Insulation class VDE 0580 |
F | F | ||||||||
Electrical fuse protection |
Every solenoid must be protected individually using a suitable fuse with tripping characteristics K (inductive loads). The valve must be installed on a surface that is included in the equipotential bonding. | Every solenoid must be protected individually using a suitable fuse with tripping characteristics K (inductive loads). The valve must be installed on a surface that is included in the equipotential bonding. | ||||||||
Protective earthing conductor and screening |
see connector pin assignment (CE-compliant installation) | see connector pin assignment (CE-compliant installation) | ||||||||
Conformity |
CE according to Low-Voltage Directive 2006/95/EC tested according to DIN EN 60204-1 (VDE0113-1): 2010-05 and DIN VDE 0580: 2000-07 | CE according to Low-Voltage Directive 2006/95/EC tested according to DIN EN 60204-1 (VDE0113-1): 2010-05 and DIN VDE 0580: 2000-07 |
1) | Possible with central connection or via rectifier. Mating connectors with rectifier (separate order). Rectifiers must comply with the relevant standards as well as the coil performance data! With a central connection, the rectifier is on the board. |
2) | Reduction of the nominal power by approx. 40 % when using a 24 V coil with connector switching amplifier type VT-SSBA1-PWM-1X/V002/5 (separate order, material no. R901265633, see data sheet 30362) |
3) | Operating mode according to VDE 0580 |
4) | Measured with flow, 80 % performance limit and horizontal installation position. Not with symbols A, B and .73. Reduction of the switching time by approx. 50 % when using a 12 V coil with connector switching amplifier type VT-SSBA1-PWM-1X/V001/5 (separate order, material no. R901265633, see data sheet 30362) |
5) | Measured with flow, 80% performance limit and horizontal installation position. |
6) | Measured without flow |
7) | Surface temperature > 50 °C, provide contact protection. |
Notices!
The solenoid coils must not be painted. Actuation of the manual override is only possible up to a tank pressure of approx. 50 bar. Avoid damage to the bore of the manual override! (Special tool for actuation, separate order, material no. R900024943). When the manual override is blocked, actuation of the opposite solenoid must be ruled out! The simultaneous actuation of 2 solenoids of one valve must be ruled out! Use cables that are approved for a working temperature above 105 °C. Valves with individual connection and a supply voltage of 12 V or 24 V can be operated with twice the voltage to reduce the switching time. For this purpose, the voltage has to be reduced to the nominal valve voltage after 100 ms by means of pulse width modulation. The maximum admissible switching frequency is 3 1 /s. Due to possible overload of the board, valves with central connection must not be operated with twice the voltage. If the standard environmental conditions according to VDE 0580 cannot be provided, the valve must be especially protected!
Electrical connections and available voltages |
||||||||||||||||||
Ordering code connector |
Ordering code |
Protection class according to DIN EN 60529 1) |
Protection class according to VDE 0580 |
|||||||||||||||
Direct voltage |
AC voltage |
|||||||||||||||||
G12 |
G24 |
G26 |
G48 |
G96 |
G110 |
G180 |
G205 |
G220 |
W100R |
W110R |
W120R |
W200R |
W230R |
|||||
Individual connection |
Without mating connector, individual connection with connector according to DIN EN 175301-803 |
K4 |
✔ |
✔ |
– |
✔ |
✔ |
– |
✔ |
✔ |
✔ 3) |
– |
– |
– |
– |
– |
IP65 |
| |
K4K2) |
✔ 3) |
✔ 3) |
✔ 3) |
– |
– |
– |
– |
– |
– |
– |
– |
– |
– |
– |
IP65, IP67 |
| |
||
Without mating connector, 4-pole with connector M12 x 1 according to IEC 60947-5-2, integrated interference protection circuit and status LED |
K72L |
– |
✔ 3) |
– |
– |
– |
– |
– |
– |
– |
– |
– |
– |
– |
– |
IP65 |
||| 5) |
|
Without mating connector; connector AMP Junior-Timer |
C4Z |
– |
– |
✔ 3) |
– |
– |
– |
✔ |
– |
– |
– |
– |
– |
– |
– |
IP66 |
||| 5) |
|
Central connection |
Without mating connector; threaded connection 1/2“-14 NPT |
DAL |
✔ |
✔ |
– |
– |
✔ |
– |
– |
✔ |
✔ |
✔ |
✔ |
✔ |
✔ |
✔ |
IP65 6) |
| |
Central plug-in connection at the cover, with indicator light (without mating connector); connector according to DIN EN 175201-804 |
DK6L7) |
✔ |
✔ |
– |
– |
✔ |
✔ |
– |
✔ |
✔ |
✔ |
✔ |
✔ |
✔ |
✔ |
IP65 |
| |
|
Cable gland at the cover, with indicator light (terminal area 6 … 12 mm) |
DL4) |
✔ |
✔ |
– |
– |
✔ |
✔ |
– |
✔ |
✔ |
✔ |
✔ |
✔ |
✔ |
✔ |
IP65 |
| |
|
Cable gland at the cover, with indicator light and cable bridge at the ground connection |
DJL4) |
– |
✔ |
– |
– |
– |
✔ |
– |
– |
– |
✔ |
✔ |
– |
✔ |
✔ |
IP65 |
| |
|
Mini-change connector, 5-pole according to ANSI/B93.55M-1981 |
DK25L7) |
– |
✔ |
– |
– |
✔ |
– |
– |
– |
– |
✔ |
✔ |
✔ |
✔ |
✔ |
IP65 |
| |
1) | Only with correctly mounted valve with a mating connector suitable for the protection class. |
2) | Recommended for mobile applications; with additional sealing between solenoid coil and pole tube. |
3) | Solenoid coils without "Recognized component" according to UL 429 |
4) | Possible with version “J3”. |
5) | With protection class III, a protective extra-low voltage with isolation transformer (PELV, SELV) is to be provided. |
6) | Only with professionally designed connection with appropriate sealing to the central connection. |
7) | Connector pin assignment see Electrical connections. |
In the electrical connection, the protective earthing conductor (PE, grounded) is to be connected in accordance with the stipulations.
Notices:
The plug-in connectors used are not intended to be plugged in or disconnected during normal operation under load. Operation of the valves only admissible with appropriate and locked mating connector.(measured with HLP46, ϑOil = 40 ±5 °C)
Δp-qV characteristic curves



Symbol |
Direction of flow |
|||
P –A |
P – B |
A – T |
B – T |
|
A; B |
6 |
6 |
– |
– |
A73, B73 |
23 |
23 |
– |
– |
C |
1 |
2 |
5 |
7 |
D |
2 |
2 |
5 |
7 |
D73 |
25 |
26 |
26 |
27 |
E |
17 |
16 |
19 |
21 |
E67 |
4 |
4 |
11 |
24 |
E73 |
17 |
18 |
21 |
21 |
F |
2 |
3 |
22 |
23 |
G |
4 |
4 |
24 |
24 |
G73 |
18 |
18 |
24 |
24 |
H |
14 |
14 |
20 |
21 |
H73 |
14 |
14 |
6 |
9 |
J |
3 |
3 |
9 |
11 |
J73 |
22 |
21 |
23 |
24 |
L |
3 |
3 |
9 |
9 |
L73 |
22 |
10 |
11 |
24 |
M |
14 |
14 |
6 |
8 |
P |
17 |
14 |
20 |
23 |
Q |
16 |
17 |
4 |
8 |
R |
18 |
21 |
18 |
24 |
R73 |
24 |
24 |
23 |
24 |
T |
18 |
4 |
10 |
24 |
U |
3 |
3 |
6 |
11 |
U10 |
upon request |
|||
U73 |
22 |
22 |
23 |
24 |
V |
17 |
17 |
18 |
20 |
W |
upon request |
|||
X7 |
upon request |
|||
X34 |
upon request |
|||
Y |
17 |
16 |
18 |
21 |
Y11 |
3 |
2 |
4 |
9 |
Y73 |
26 |
26 |
26 |
28 |
Central position: |
|||||
Symbol |
Direction of flow |
||||
P – A |
P – B |
B – T |
A – T |
P – T |
|
H |
12 |
12 |
13 |
13 |
15 |
Performance limits
(measured with HLP46, ϑOil = 40 ±5 °C)
Notice:
The specified performance limits are valid for use with two directions of flow (e. g. from P to A and simultaneous return flow from B to T).
Due to the flow forces acting within the valves, the admissible performance limit may be considerably lower with only one direction of flow (e. g. from P to A while port B is blocked)!
In such use cases, please consult us!
The performance limit was determined when the solenoids were at operating temperature, at 10 % undervoltage and without tank preloading.
Spring side

Characteristic curve |
Symbol |
1 |
L |
2 |
A |
3 |
B |
4 |
Y |
5 |
E73, Q |
6 |
F |
7 |
G73 |
8 |
M; V |
9 |
P |
10 |
A73 |
11 |
H73 |

Solenoid side
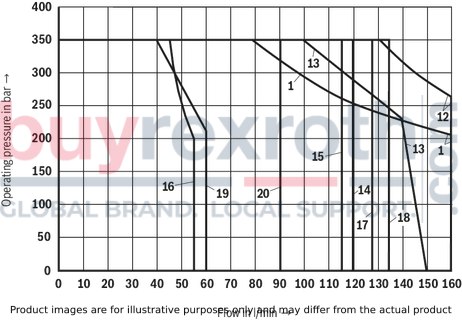
Characteristic curve |
Symbol |
1 |
L |
12 |
A/O |
13 |
J |
14 |
H |
15 |
D73 |
16 |
B73 |
17 |
Y11 |
18 |
C; D; E73 |
19 |
E67 |
20 |
G |
Performance limits
(measured with HLP46, ϑOil = 40 ±5 °C)
Notice:
The specified performance limits are valid for use with two directions of flow (e. g. from P to A and simultaneous return flow from B to T).
Due to the flow forces acting within the valves, the admissible performance limit may be considerably lower with only one direction of flow (e. g. from P to A while port B is blocked)!
In such use cases, please consult us!
The performance limit was determined when the solenoids were at operating temperature, at 10 % undervoltage and without tank preloading.
Solenoid side


Characteristic curve |
Symbol |
21 |
A; B |
22 |
G73 |
23 |
F; L73 |
24 |
E |
25 |
C/O; D/O |
26 |
J73 |
27 |
U |
Solenoid side

On solenoid side

Characteristic curve |
Symbol |
28 |
Q |
29 |
V |
30 |
P |
31 |
R |
32 |
R73 |
33 |
T |
34 |
U73 |
35 |
Y73 |

Notices!
Representation according to DIN ISO 1219-1.
Hydraulic interim positions are shown by dashes.

1) |
Example: ● Symbol E with spool position “a” ordering code ..EA.. ● Symbol E with spool position “b” ordering code ..EB.. |
2) | For the flow cross-section refer to the Technical data |
Notices!
Representation according to DIN ISO 1219-1.Hydraulic interim positions are shown by dashes.
Other symbols upon request.Over-current fuse and switch-off voltage peaks
Maximum admissible overvoltages according to DIN EN 60664-1:2008-01 (VDE 0110-1) (overvoltage category II): |
|||
Electrical connection 1) |
Nominal voltage in V |
Rated current in A |
Maximum switch-off overvoltage to be energized in V 2) |
K4, K4K, DAL, D6KL, DL |
12 |
3,72 |
500 |
K4, K4K, K72L, DAL, D6KL, DL, DJL, DK25L |
24 |
1,74 |
500 |
K4, C4Z |
26 |
1,70 |
500 |
K4 |
48 |
0,57 |
500 |
K4, DAL, D6KL, DL, DK25L |
96 |
0,47 |
500 |
D6KL, DL, DJL |
110 |
0,41 |
500 |
K4 |
125 |
0,22 |
500 |
K4, C4Z |
180 |
0,28 |
500 |
K4, DAL, D6KL, DL |
205 |
0,22 |
500 |
K4, DAL, D6KL, DL |
220 |
0,21 |
500 |
1) | Interference protection circuit integrated |
2) | To be ensured by user circuitry |
Notice!
When solenoid coils are switched off, voltage peaks result which may cause faults or damage in the connected control electronics. We therefore recommend limiting them to 2 x nominal voltage by means of an interference protection circuit. It must be noted that a diode switched in an antiparallel form extends the switching off time.
Assignment – individual connection
Electrical connections and coil connection combinations |
|||||
Ordering code connector |
Top view |
Circuit diagram |
Pin |
Connections, assignment |
|
3-pole connector (2+PE) according to DIN EN 175301-803 |
K4, K4K 2) |
![]() |
![]() |
1 |
Solenoid coil, polarity-independent |
2 |
|||||
Earthed |
Earthing |
||||
4-pole connector according to IEC 60947-5-2, M12x1 with suppressor diode, only 24 V DC, integrated interference protection circuit and status LED |
K72L |
![]() |
![]() |
1 |
Internal bridge |
2 |
|||||
3 |
Solenoid coil GND |
||||
4 |
Solenoid coil 24 VDC supply voltage |
||||
5 |
Without function |
||||
2-pole connector, type AMP Junior-Timer, rotated by 90° relative to valve axis |
C4Z |
![]() |
![]() |
1 |
Solenoid coil, polarity-independent |
2 |
1) | M3, tightening torque maximum MA max = 0.5 Nm |
2) | Coil with potted-in connector base and sealing element to valve housing (IP67) |
Assignment – central connection
Electrical connections and coil connection combinations |
|||||
Ordering code connector |
Top view |
Circuit diagram |
Pin |
Connections, assignment |
|
Cable gland at the cover, with indicator light (terminal area 6 … 12 mm) |
DL |
![]() |
![]() |
1+ |
Valve solenoid "a" 2) |
Cable gland at the cover, with indicator light and cable bridge at the ground connection (terminal area 6 … 12 mm) |
DJL |
2- |
|||
![]() |
![]() |
3+ |
Valve solenoid "b" 2) |
||
Without mating connector; threaded connection 1/2“-14 NPT (terminal area 6 … 12 mm) |
DAL |
4- |
|||
Earthed |
Earthing |
||||
Central connection at the cover, with indicator light (without mating connector) with connector according to DIN EN 175201-804 |
DK6L |
![]() |
![]() |
1 |
Valve solenoid "a" |
2 |
|||||
3 |
Valve solenoid "b" |
||||
4 |
|||||
5 |
Not assigned |
||||
6 |
|||||
Earthed |
Earthing |
||||
Mini-change connector, 5-pole according to ANSI/B93.55M-1981 |
DK25L |
![]() |
![]() |
1 |
Valve solenoid "a" |
5 |
|||||
2 |
Valve solenoid "b" |
||||
4 |
|||||
3 |
Earthing |
1) Bridge only for version “DJL"
2) Core marking:
+ → red
- → blue
3) Cable gland with NPT thread

Mating connectors according to DIN EN 175301-803
For details and more mating connectors see data sheet 08006 |
||||||
Connection |
Valve side |
Color |
Part number |
|||
Without circuitry |
With indicator light 12 ... 240 V |
With rectifier 12 ... 240 V |
With indicator light and Zener diode suppression circuit 24 V |
|||
M16 x 1,5 |
a |
gray |
R901017010 |
– |
– |
– |
a/b |
black |
R901017011 |
R901017022 |
R901017025 |
R901017026 |
|
1/2″ NPT |
a |
red/brown |
R900004823 |
– |
– |
– |
a/b |
black |
R900011039 |
R900057453 |
R900842566 |
– |
Energy savings and fast switching 1) |
|||
Details see data sheet 30362 |
|||
Part number |
|||
Type VT-SSBA1-PWM-1X/V001/5 as fast switching amplifier (switching time reduction by approx. 50 %) 2) |
Type VT-SSBA1-PWM-1X/V002/5 for energy reduction (energy saving by approx. 40 %) 3) |
||
a/b |
black |
R901265633 |
R901290194 |
1) | Groove with symbols C, D, E, E67, J, J2, Y and Y11; not for version reinforced compression spring “D” |
2) | Only for version “G12” and “K4/K4K” |
3) | Only for version “G24” and “K4/K4K” |
Cartridge with PWM connector according to data sheet 30362:
Depending on the control spool, increasing the performance limit is possible. With version "G24" (energy saving), the coil temperature is reduced by ≥ [si]30 °C[s/i][imp]86 °F[/imp] for 100 % duty cycle.Individual connection
Dimensions in mm
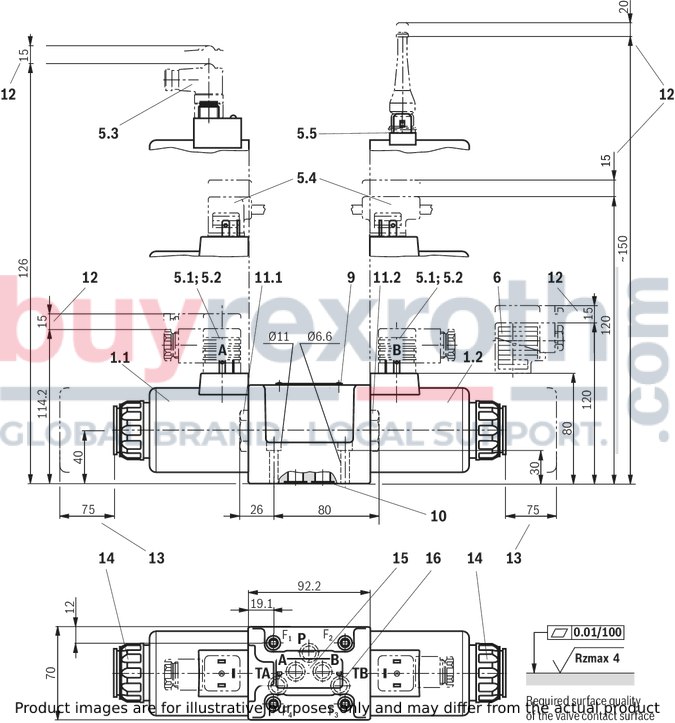
1.1 |
Solenoid “a” |
1.2 |
Solenoid “b” |
5.1 |
Mating connector without circuitry for connector "K4", separate order, see "Accessories" |
5.2 |
Mating connector without circuitry for connector "K4K" (separate order, see data sheet 08006) |
5.3 |
Mating connector angled with M12x1 plug-in connection and status LED for connector "K72L", separate order, see "Accessories" |
5.4 |
Double mating connector without/with circuitry for connector "K4" (separate order, see data sheet 08006) |
5.5 |
Mating connector (AMP Junior Timer) for connector "C4Z" (separate order, see data sheet 08006) |
6 |
Mating connector without circuitry for connector "K4", separate order, see "Accessories" |
9 |
Name plate |
10 |
Identical seal rings for ports A, B, P, TA, TB |
11.1 |
Plug screw for valves with one solenoid on B side |
11.2 |
Plug screw for valves with one solenoid on A side |
12 |
Space required to remove the mating connector/angled socket |
13 |
Space required to remove the coil |
14 |
Mounting nut, tightening torque MA = 14.5±1.5 Nm |
15 |
Porting pattern according to ISO 4401-05-04-0-05 |
16 |
Connection TB can only be used in connection with separately produced bore. |
Notes:
Deviating from ISO 4401, port T is referred to as TA and port T1 is referred to as TB in this data sheet. The dimensions are nominal dimensions which are subject to tolerances.Dimensions for manual overrides see manual overrides.
For item explanations, valve mounting screws and subplates see legend - dimensions.
Central connection
Dimensions in mm
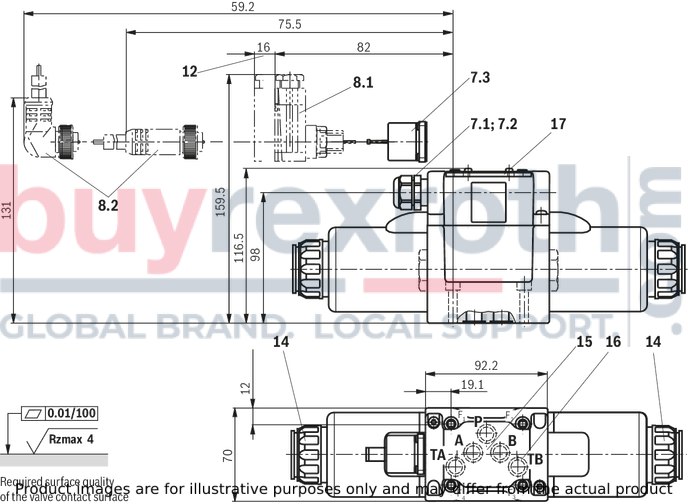
7.1 |
Cable gland Pg 16 "DL" (terminal area 6 … 12 mm); lock nut, tightening torque MA = 3.3 Nm±10 % |
7.2 |
Central connection box "DAL“ 1/2“ NPT, tightening torque MA = 5 Nm ± 10 %; sealing by sealant |
8.1 |
Mating connector for connector "DK6L” (separate order, material no. R900002803, see data sheet 08006) |
8.2 |
Mini-change connector, 5-pole for connector "DK25L" (separate order, material no. R900057631) |
12 |
Space required to remove the mating connector/angled socket |
14 |
Mounting nut, tightening torque MA = 14.5±1.5 Nm |
15 |
Porting pattern according to ISO 4401-05-04-0-05 |
16 |
Connection TB can only be used in connection with separately produced bore. |
17 |
CoverNotice: The valve may only be operated with properly mounted cover! Tightening torque of the cover screws MA = 1.0 Nm ± 10 %.Prior to opening the frame, it must be ensured that the valve has no voltage! |
Special points with version "DAL" and "DL"
Version "DL" is only suitable for permanently installed cables. Lines must be routed in a strain-relieved manner! Minimum line cross-section 0.75 mm2 (AWG 18) With a maximum line cross-section of 1.5 mm2 (AWG 16) and if wire end ferrules are used, wire end ferrules without flange must be crimped to a maximum cross-section of 1.5 x 2 mm (trapezoidal crimp) using an appropriate tool (e. g. “PZ 6/5”, co. Weidmüller) to ensure that they fit into the printed circuit board terminals. Before crimping, the wires have to be stripped to 9-1 mm. For the corresponding line cross-section, 1) wire end ferrules without flange (according to DIN 46228-1) with a length of 8 mm are to be used. For the grounding connection, ring cable lugs according to DIN 46234-4-1 are to be used, tightening torque MA = 1.75 Nm ± 10 %Notice:
The lines must be finely stranded.
Dimensions for manual overrides see manual overrides.
For item explanations, valve mounting screws and subplates see legend - dimensions.
Notice:
The dimensions are nominal dimensions which are subject to tolerances.
Manual override
Dimensions in mm
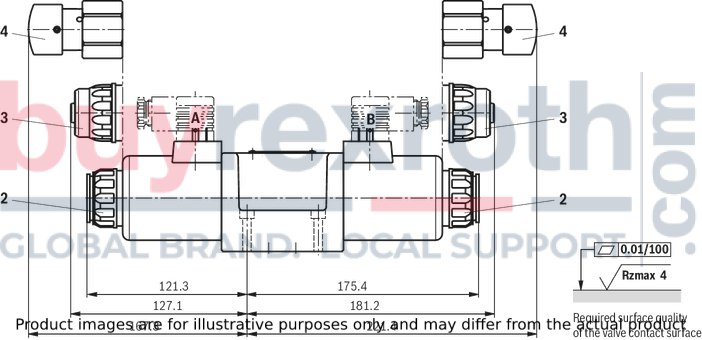
2 |
Version without and with concealed manual override "N9" (standard) |
3 |
Version with concealed manual override and protective cap "N8". (The protective cap must be removed prior to actuation.) |
4 |
Version with manual override "N5" and “N6” |
For item explanations, valve mounting screws and subplates refer to the legend - dimensions.
Notice:
The dimensions are nominal dimensions which are subject to tolerances.
Subplates according to data sheet 45054 (separate order)
G 66/01 (G3/8)
G 67/01 (G1/2)
G 534/01 (G3/4)
G 66/12 (SAE-6; 9/16-18)1)
G 67/12 (SAE-8; 3/4-16)1)
G 534/12 (SAE-12; 1-1/16-12)1)
1) Upon request
Valve mounting screws (separate order)
4 hexagon socket head cap screws, metric
ISO 4762 - M6 x 40 - 10.9-flZn-240h-L
(friction coefficient μtotal = 0.09 to 0.14);
tightening torque MA = 12.5 Nm ± 10 %,
material no. R913000058
or
4 hexagon socket head cap screws
ISO 4762 - M6 x 40 - 10.9 (self procurement)
(friction coefficient μtotal = 0.12 to 0.17);
tightening torque MA = 15.5 Nm ± 10 %
4 hexagon socket head cap screws UNC
1/4-20 UNC x 1-1/2″ ASTM-A574
(friction coefficientμtotal = 0.19 to 0.24);
Tightening torque MA = 25 Nm ± 15 %,
(friction coefficient μtotal = 0.12 to 0.17);
tightening torque MA = 19 Nm ± 10 %,
material no. R978800710
With different friction coefficients, the tightening torques are to be adjusted accordingly!
Temperature range and maximum operating pressure in case of use at low temperatures
Connection |
Pressure |
Temperature range in °C |
– P, A, B, T |
static 100 bar |
–40 … –35 |
– P, A, B |
dynamic from 100 bar to 350 barin linear form as a function of the temperature |
–35 … –30 |
– T |
dynamic from 100 bar to 210 bar in linear form as a function of the temperature |
–35 … –30 |
– P, A, B, T |
Maximum operating pressure |
–30 … +50 |
Mating connectors for valves with connector “K4”, without circuitry, standard
3P Z4
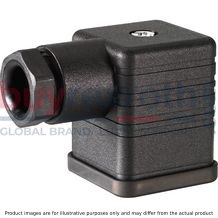
Mating connectors for valves with connector “K4”, without circuitry, standard
3P Z4
For valves with connector “K4” according to EN 175301-803 and ISO 4400, 2-pole + PE, “large cubic connector” Mating connectors for valves with one or two solenoids (individual connection)Data sheet
Spare parts & repair
Mating connectors for valves with connector “K4”, without circuitry, standard
3P Z45
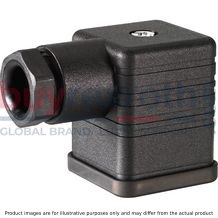
Mating connectors for valves with connector “K4”, without circuitry, standard
3P Z45
For valves with connector “K4” according to EN 175301-803 and ISO 4400, 2-pole + PE, “large cubic connector” Mating connectors for valves with one or two solenoids (individual connection)Data sheet
Spare parts & repair
Mating connectors for valves with connector “K4”, with indicator light
3P Z5L
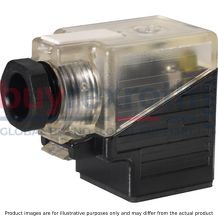
Mating connectors for valves with connector “K4”, with indicator light
3P Z5L
For valves with connector “K4” according to EN 175301-803 and ISO 4400, 2-pole + PE, “large cubic connector” Mating connectors for valves with one or two solenoids (individual connection)Data sheet
Spare parts & repair
Mating connectors for valves with connector “K4”, with indicator light
3P Z55L
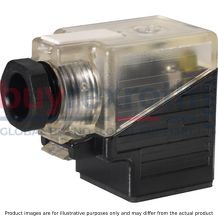
Mating connectors for valves with connector “K4”, with indicator light
3P Z55L
For valves with connector “K4” according to EN 175301-803 and ISO 4400, 2-pole + PE, “large cubic connector” Mating connectors for valves with one or two solenoids (individual connection)Data sheet
Spare parts & repair
Mating connectors for valves with connector “K4”, with indicator light and Zener diode suppression circuit
3P Z5L1
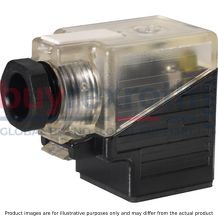
Mating connectors for valves with connector “K4”, with indicator light and Zener diode suppression circuit
3P Z5L1
For valves with connector “K4” according to EN 175301-803 and ISO 4400, 2-pole + PE, “large cubic connector” Mating connectors for valves with one or two solenoids (individual connection)Data sheet
Spare parts & repair
Mating connectors for valves with connector “K4”, with rectifier
3P RZ5
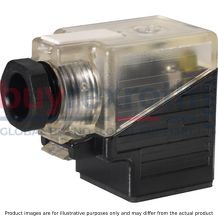
Mating connectors for valves with connector “K4”, with rectifier
3P RZ5
For valves with connector “K4” according to EN 175301-803 and ISO 4400, 2-pole + PE, “large cubic connector” Mating connectors for valves with one or two solenoids (individual connection)Data sheet
Spare parts & repair
Mating connectors for valves with connector “K4”, with rectifier
3P RZ55
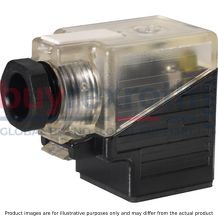
Mating connectors for valves with connector “K4”, with rectifier
3P RZ55
For valves with connector “K4” according to EN 175301-803 and ISO 4400, 2-pole + PE, “large cubic connector” Mating connectors for valves with one or two solenoids (individual connection)Data sheet
Spare parts & repair
Related Products
R978035519
$495.00 USD
R978894119
$593.00 USD
R900455015
$834.00 USD
R978028325
$410.00 USD
R900927610
$1,866.00 USD