PRESSURE RELIEF VALVE DBW30B1N5X/315-6EG24N9K4
Manufacturer: Bosch Rexroth
Material #: R900939239
Model : DBW30B1N5X/315-6EG24N9K4
***Disclaimer: The following summary contains information gathered from various sources such as product descriptions, technical specifications and catalogs. While efforts have been made to provide accurate details, inaccuracies may occur. It is advised to verify all information by contacting Bosch Rexroth directly.***
The Bosch Rexroth DBW30B1N5X/315-6EG24N9K4 (R900939239) is an industrial hydraulic valve designed for high-performance applications, featuring reliable pressure limitation up to the setting value and solenoid unloading via a built-on directional spool valve. This pilot-operated pressure relief valve includes a main valve with a main spool insert and a pilot control valve with an adjustable pressure range of up to 315 bar. It also incorporates an integrated directional spool valve for managing the unloading process.
The DBW30B1N5X/315-6EG24N9K4 is equipped with NBR seals and is compatible with various hydraulic fluids including HL, HLP, HLPD, HVLP, HVLPD, and HFC. It offers mechanical actuation and comes with a 4-pole PE electrical connector according to EN 175301-803 standards. This model has subplate mounting capabilities conforming to ISO patterns NG6, NG10, and NG16.
With a maximum operating pressure of 315 bar and a maximum flow rate of 30 l/min, this valve ensures efficient operation in demanding environments. The unit's size is indicated by its model code, while its component series X signifies its robust design. The number of switching positions it supports is two, indicating its versatility in system integration.
Additional features include an optional switching shock damping system that mitigates pressure peaks and acoustic decompression shocks in the return line by delaying the opening from port B to B. Various adjustment types are available for precise pressure settings such as rotary knobs or sleeves with hexagons.
The Bosch Rexroth DBW30B1N5X/315-6EG24N9K4 is thus ideal for applications requiring precise control over operating pressures with the added benefit of solenoid actuated unloading capabilities for enhanced operational flexibility.
$1,437.00 USD
More are expected on December 8, 2025
Qty | Price | Savings |
---|---|---|
5-24 | $1,401.07 USD | $35.93 USD |
25+ | $1,365.15 USD | $71.85 USD |
Status: This product is temporarily out of stock.
Qty: Delivered as early as December 8, 2025 when ordered in
This product is eligible for factory repair.
Size 32, P → T, mechanical, 24 V DC
Industrial hydraulic valve in a high performance range. Reliable pressure limitation to setting value
Unpacked Weight: 6.520 kg
For subplate mounting Porting pattern according to ISO 6264-06-09 (NG10), ISO 6264-08-13 (NG25) and ISO 6264-10-17 (NG32) For threaded connection As screw-in cartridge valve (cartridge) 4 adjustment types for pressure adjustment, optionally
• Rotary knob
• Sleeve with hexagon and protective cap
• Lockable rotary knob with scale
• Rotary knob with scale 5 pressure ratings Solenoid-operated unloading via built-on directional spool valve or directional poppet valve High-power solenoid Switching shock damping, optional
The pressure valve type DBW is a pilot-operated pressure relief valve.
They are used for limiting and solenoid-actuated unloading the operating pressure.
The valve basically consists of the main valve (1) with main spool insert (3) and pilot control valve (2) with pressure adjustment element and one integrated directional spool valve (16).
The function of this valve is basically the same as that of valve type DB. The unloading of the main spool (3) is, however, achieved by controlling the mounted directional spool valve (16).
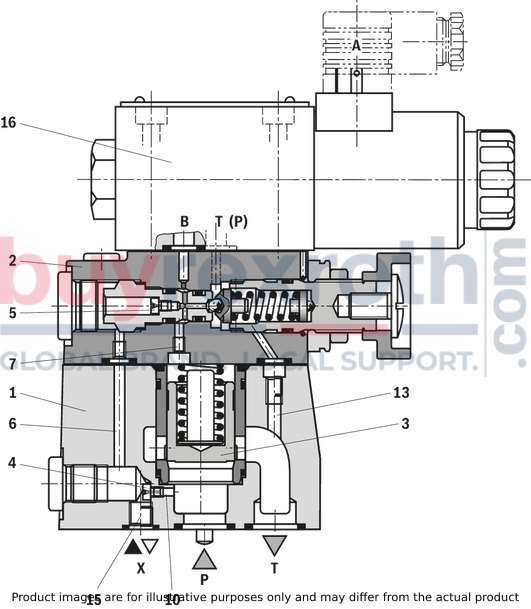
Pressure relief valve with switching shock damping (sandwich plate), version "DBW.../..S6...R12"
The opening of the connection from B2 to B1 is delayed by means of the switching shock damping valve (17). Pressure peaks and acoustic decompression shocks in the return line are thus avoided. It is installed between the pilot control valve (2) and the directional valve (16).
The degree of damping (decompression shock) is determined by the size of the nozzle (18). Nozzle Ø1.2 mm (ordering code "R12") is recommended.
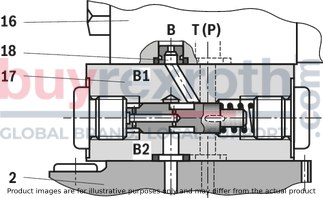
Data Sheet | Download Data Sheet |
Manual | Download Manual |
Manual | Download Manual |
Manual | Download Manual |
Manual | Download Manual |
Manual | Download Manual |
Max. pressure | 350 |
Electrical connection description | Connector 3-pole (2 + PE) according to EN 175301-803 |
Productgroup ID | 9,10,11,12,13,14 |
Number of ports | 2 |
Type of actuation | with manual actuation |
Size | 32 |
Electrical connector | Connector 3-pole (2 + PE) |
Max. flow | 650 |
Type of connection | Subplate mounting |
Connection diagram | ISO 6264-10-17 |
Supply voltage | 24 VDC |
Number of switching positions | 2 |
Weight | 6.520 |
Seals | NBR |
Hydraulic fluid | HL,HLP,HLPD,HVLP,HVLPD,HFC (Fuchs: Hydrotherm 46M, Renosafe 500; Petrofer: Ultra Safe 620; Houghton: Safe 620; Union: Carbide HP5046) |
Hydraulic fluid | HL,HLP,HLPD,HVLP,HVLPD,HFC |
01 |
02 |
03 |
04 |
05 |
06 |
07 |
08 |
09 |
10 |
11 |
12 |
13 |
14 |
15 |
16 |
17 |
18 |
19 |
20 |
21 |
22 |
|
DB |
W |
5X |
/ |
K4 |
* |
01 |
Pressure relief valve |
DB |
02 |
With attached directional valve |
W |
03 |
Pilot-operated valve (complete) |
no code |
Pilot control valve without main spool insert (do not enter any size) |
C |
|
Pilot control valve with main spool insert (enter size 10 or 30) |
C |
|
Pilot control valve without main spool insert for subplate mounting (do not enter any size) |
T 1) |
|
04 |
Size 10 |
|
Subplate mounting "no code" |
10 |
|
Threaded connection "G" |
10 (G1/2) |
|
Size 16 |
||
Threaded connection "G" |
15 (G3/4) |
|
Size 25 |
||
Subplate mounting "no code" |
20 |
|
Threaded connection "G" |
20 (G1) |
|
Threaded connection "G" |
25 (G1 1/4) |
|
Size 32 |
||
Subplate mounting "no code" |
30 |
|
Threaded connection "G" |
30 (G1 1/2) |
|
05 |
Normally closed |
A |
Normally open |
B |
|
Type of connection |
||
06 |
Subplate mounting or cartridge valve |
no code |
For threaded connection |
G |
|
Adjustment type for pressure adjustment |
||
07 |
Rotary knob (not for version "C" and "T") |
1 |
Sleeve with hexagon and protective cap |
2 |
|
Lockable rotary knob with scale |
3 2) |
|
Rotary knob with scale |
7 |
|
08 |
Main spool Ø24 mm (all sizes) |
– |
Main spool Ø28 mm (only for NG32) |
N |
|
09 |
Component series 50 … 59 (50 … 59: unchanged installation and connection dimensions) |
5X |
10 |
Set pressure up to 50 bar |
50 |
Set pressure up to 100 bar |
100 |
|
Set pressure up to 200 bar |
200 |
|
Set pressure up to 315 bar |
315 |
|
Set pressure up to 350 bar |
350 |
|
Pilot oil flow |
||
11 |
External pilot oil supply, internal pilot oil return |
X 3) |
Internal pilot oil supply, external pilot oil return |
Y |
|
Pilot oil supply and pilot oil return external |
XY 3) |
|
12 |
Standard version |
no code |
Valve for minimum cracking pressure (not for versions "without main spool insert" and not suitable for mutual relief) |
U 4) |
|
13 |
Without switching shock damping |
no code |
With switching shock damping |
S |
|
14 |
With directional spool valve (data sheet 23178) |
6E |
With directional seat valve (data sheet 22058) |
6SM |
|
15 |
Direct voltage 24 V |
G24 |
Alternating voltage 230 V, 50/60 Hz |
W230 |
|
16 |
Without manual override |
no code |
With concealed manual override |
N9 |
|
With manual override |
N |
|
Electrical connection |
||
17 |
Connector DIN EN 175301-803 |
K4 5) |
18 |
Nozzle Ø1,2 mm in channel B of the directional spool valve (version "6E") |
R12 6) |
Nozzle Ø1,2 mm in channel P of the directional seat valve (version "6SM") |
B12 6) |
|
Corrosion resistance |
||
19 |
None |
no code |
Seal material |
||
20 |
NBR seals |
no code |
FKM seals |
V |
|
Observe compatibility of seals with hydraulic fluid used. (Other seals upon request) |
||
Equipment Directive |
||
21 |
Without type-examination procedure |
no code |
Type-examination tested safety valve according to Pressure Equipment Directive 2014/68/EU |
E |
|
22 |
Further details in the plain text |
* |
1) | DBT corresponds to DBC, however with closed central bore |
2) | H-Key with material no. R900008158 is included in the scope of delivery. |
3) | Not with version "DBC" |
4) | Only possible up to pressure rating 315 bar |
5) | Mating connectors, separate order, see "Accessories" |
6) | Ordering code only necessary with version with attached directional valve and switching shock damping ("S") |
Type-examination tested safety valves type DBW…E
(Component series 5X according to Pressure Equipment Directive 2014/68/EU)
NG |
Type designation |
Component marking |
Maximum flow qVmax in l/min with pilot oil return |
Set response overpressurep in bar |
|
external "Y" |
internal "–" |
||||
10 |
![]() |
TÜV.SV.▢ – 851.12.F.G.p |
170 230 230 230 |
130 200 200 200 |
30 ... 60 61 ... 110 111 ... 210 211 ... 350 |
25 |
![]() |
TÜV.SV.▢ – 852.22.F.G.p |
250 270 420 450 |
180 210 320 400 |
30 ... 60 61 ... 110 111 ... 210 211 ... 350 |
32 |
![]() |
TÜV.SV.▢ – 853.32.F.G.p |
600 600 650 700 |
225 340 540 580 |
30 ... 60 61 ... 110 111 ... 210 211 ... 350 |
1 |
Directional valve, normally closed |
A |
Directional valve, normally open |
B |
|
2 |
For subplate mounting |
no code |
For threaded connection |
G |
|
Adjustment type for pressure adjustment |
||
3 |
Hand wheel (pressure adjustment sealed, unloading or setting of a lower response pressure possible!) |
1 |
With sealed protective cap (no adjustment/unloading possible) |
2 |
|
Pressure |
||
4 |
To be entered by the customer, e.g. pressure adjustment ≥ 30 bar and possible in 5 bar steps. |
e.g. 150 |
Pilot oil flow |
||
5 |
Pilot oil supply internal, pilot oil return internal |
no code |
Pilot oil supply internal, pilot oil return external (Recommendation) |
Y 1) |
|
Electrical specifications |
||
6 |
see Type code above |
e.g. EG24N9K4 |
7 |
NBR seals |
no code |
FKM seals |
V |
|
▢ |
Value entered at the factory |
1) | Pilot oil supply external "X" not possible |
general
Size |
10 | 16 | 25 | 32 | ||||
DB.. 15 | DB.. 20 | DB.. 25 | ||||||
Weight |
Subplate mounting |
DBW... |
kg |
4.05 | - | 4.95 | - | 5.85 |
DBWC... |
kg |
2.65 | ||||||
DBWC 10 or 30 ... |
kg |
2.95 | ||||||
Threaded connection |
DBW...G |
kg |
6.75 | 6.65 | 6.55 | 6.45 | 6.25 | |
Installation position |
any | |||||||
Ambient temperature range |
NBR seals |
°C |
-30 … +50 | |||||
FKM seals |
°C |
-15 … +50 | ||||||
Minimum stability of the housing materials |
with subplate mounting and version "DBWC" |
Housing materials are to be selected so that there is sufficient safety for all imaginable operating conditions (e.g. with regard to pressure resistance, thread stripping strengths and tightening torques). |
hydraulic
Size |
10 | 16 | 25 | 25 | 32 | ||
Maximum operating pressure |
Port P |
bar |
350 | ||||
Port X |
bar |
350 | |||||
Port T |
bar |
315 | |||||
Maximum counter pressure |
Port Y (DC solenoid) |
bar |
210 | ||||
Port Y (AC solenoid) |
bar |
160 | |||||
Port T (DC solenoid) |
bar |
210 | |||||
Port T (AC solenoid) |
bar |
160 | |||||
Minimum set pressure |
flow-dependent, see characteristic curves | ||||||
Maximum set pressure |
bar |
50 100 200 315 350 |
|||||
Maximum flow |
Subplate mounting |
l/min |
250 | - | 500 | - | 650 |
Threaded connection |
l/min |
250 | 500 | 650 | |||
Hydraulic fluid |
see table | ||||||
Hydraulic fluid temperature range |
NBR seals |
°C |
-30 … +80 | ||||
FKM seals |
°C |
-15 … +80 | |||||
Viscosity range |
mm²/s |
10 … 800 | |||||
Maximum admissible degree of contamination of the hydraulic fluid 1) |
Class 20/18/15 according to ISO 4406 (c) |
1) | The cleanliness classes specified for the components must be adhered to in hydraulic systems. Effective filtration prevents faults and simultaneously increases the life cycle of the components. For the selection of the filters, see www.boschrexroth.com/filter. |
Notes:
Tank preloading adds to the minimum set pressure (ports T and Y) Technical data for directional seat valve see data sheet 22058, for directional spool valve data sheet 23178.
Hydraulic fluid |
Classification |
Suitable sealing materials |
Standards |
Data sheet |
|
Mineral oils |
HL, HLP |
NBR, FKM |
DIN 51524 |
90220 |
|
Bio-degradable 1) |
Insoluble in water |
HETG |
FKM |
ISO 15380 |
90221 |
HEES |
FKM |
||||
Soluble in water |
HEPG |
FKM |
ISO 15380 |
||
Flame-resistant |
Water-free |
HFDU (glycol base) |
FKM |
ISO 12922 |
90222 |
HFDU (ester base) 1) |
FKM |
||||
Important information on hydraulic fluids: For further information and data on the use of other hydraulic fluids, please refer to the data sheets above or contact us. There may be limitations regarding the technical valve data (temperature, pressure range, life cycle, maintenance intervals, etc.). The ignition temperature of the hydraulic fluid used must be 50 K higher than the maximum solenoid surface temperature. Flame-resistant – containing water: Maximum operating pressure 210 bar Life cycle as compared to operation with mineral oil HL, HLP 30 … 100 % Maximum hydraulic fluid temperature 60 °C Bio-degradable and flame-resistant: If this hydraulic fluid is used, small amounts of dissolved zinc may get into the hydraulic system. |
1) | Not recommended for corrosion-protected version “J3” |
Deviating technical data: Type-examination tested safety valves type DBW…E
(Component series 5X according to Pressure Equipment Directive 2014/68/EU)
hydraulic
Version |
Pilot oil flow "no code" | Pilot oil flow "Y" | ||
Maximum counter pressure |
Port Y |
bar |
- | 0 |
Port T |
See characteristic curves and explanatory notes for maximum counter pressure | PT < 15 | ||
Maximum flow |
See ordering code, safety instructions and characteristic curves "Type-examination tested safety valve" | |||
Hydraulic fluid |
Mineral oil (HL, HLP) according to DIN 51524 and DIN 51524-1 | |||
Viscosity range |
mm²/s |
12 … 230 |
For applications outside these parameters, please consult us!
(measured with HLP46, ϑOil = 40 ±5 °C)
Standard version
Minimum set pressure and circulation pressure dependent on the flow 1)

1) | The characteristic curves apply to an output pressure pT =0 bar in the entire flow range. |
Version “U”
Minimum set pressure and circulation pressure dependent on the flow 1)

Inlet pressure dependent on the flow

Notice:
The characteristic curves were measured with external, depressurized pilot oil return.
Due to the internal pilot oil return, the inlet pressure increases by the output pressure present in port T.
Pilot flow

Type-examination tested safety valves
(Component series 5X, according to Pressure Equipment Directive 2014/68/EU)
Counter pressure in the discharge line
Basically, the valve should be operated without counter pressure in the discharge line, if possible. With counter pressure in the discharge line, the maximum flow possible is reduced. There is a relation between the maximum counter pressure pT in the discharge line and flow qV, which can be seen from the following characteristic curves. Characteristic curves for intermediate values of the response pressure which are not listed must be determined by means of interpolation.
With a flow approaching zero, the maximum counter pressure pT is in each case 10 % of the response pressure. With increasing flow, the maximum counter pressure pT is reduced.
Interpolation of intermediate values from the diagram
At the pT axis, mark 1/10 of the value of pA. Determine the next lower and the next higher characteristic curve for this point. The point marked at pT divides the section between lower and higher characteristic curve on the pT axis with a certain percentage. At the qVmax axis, divide the section between next lower and next higher characteristic curve in the same percentage as the section at the pT axis. From the zerocrossing on the qVmax axis determined in that way, draw a straight line to the value on the pT axis marked before. Mark the system flow to be secured at the qVmax axis. Read off the maximum counter pressure for this value using the line at the pT axis drawn before.
Determination of the maximum counter pressure
Example 1 (with already existing characteristic curve):
Flow of the system / accumulator to be secured:qVmax = [si]300 l/min[/si][imp]79.3 USgpm[/imp Safety valve set to: pA = [si]80 bar[/si][imp]1150 psi[/imp]. Read off the maximum counter pressure pT of approx. [si]12 bar[/si][imp]175 psi[/imp] from the diagram (see arrows, dashed line " ").
Example 2 (with interpolated characteristic curve):
Flow of the system / accumulator to be secured: qVmax = [si]300 l/min[/si][imp]79.3 USgpm[/imp Safety valve set to: pA = [si]80 bar[/si][imp]1150 psi[/imp] Value to be marked at the axis referred to as pT: 1/10 x [si]80 bar[/si][imp]1150 psi[/imp] = [si]8 bar[/si][imp]115 psi[/imp]. Read off the maximum counter pressure pT of approx. [si]1 bar[/si][imp]15 psi[/imp] from the diagram (see arrows, dashed/dotted line " ").
Size 10
Diagram for determining the maximum counter pressure pT in the discharge line at port T of the valve dependent on the flow qVmax for valves type DB(W)...E with different response pressures pA.Intermediate values may be determined by means of interpolation. Regarding the procedure for interpolation refer to "Interpolation of intermediate values from the diagram".

Size 20
Diagram for determining the maximum counter pressure pT in the discharge line at port T of the valve dependent on the flow qVmax for valves type DB(W)...E with different response pressures pA.Intermediate values may be determined by means of interpolation. Regarding the procedure for interpolation refer to "Interpolation of intermediate values from the diagram".

Size 30
Diagram for determining the maximum counter pressure pT in the discharge line at port T of the valve dependent on the flow qVmax for valves type DB(W)...E with different response pressures pA.Intermediate values may be determined by means of interpolation. Regarding the procedure for interpolation refer to "Interpolation of intermediate values from the diagram".

pA |
Response pressure in bar |
pT |
Maximum counter pressure in the discharge line (port T) in bar (sum of all possible counter pressures; also see AD2000 data sheet - A2) |
pT max |
10% x pA (with qV=0 l/min) according to Pressure Equipment Directive 2014/68/EU |
qV max |
Maximum flow in l/min |
Type DBW…S6E...R12
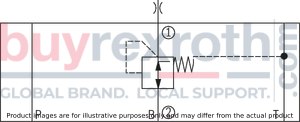
Threaded connection "G"
Dimensions in mm

1 |
Name plate |
2 |
X port for pilot oil supply, external |
3 |
Y port for pilot oil return, external |
4 |
Adjustment type "1" |
5 |
Adjustment type "2" |
6 |
Adjustment type "3" |
7 |
Adjustment type "7" |
8 |
Hexagon SW10 |
9 |
Space required to remove the key |
11 |
Valve mounting bores |
19 |
Omitted with internal pilot oil return |
Version |
D1 |
ØD2 |
T1 |
mm |
mm |
||
"DB 10 G" | G1/2 | 34 | 14 |
"DB 15 G" | G3/4 | 42 | 16 |
"DB 20 G" | G1 | 47 | 18 |
"DB 25 G" | G1 1/4 | 58 | 20 |
"DB 30 G" | G1 1/2 | 65 | 22 |
Dimensions for attached directional valve see "Subplate mounting"
Subplate mounting with directional spool valve "6E"

1 |
Name plate |
2 |
X port for pilot oil supply, external |
3 |
Y port for pilot oil return, external |
4 |
Adjustment type "1" |
5 |
Adjustment type "2" |
6 |
Adjustment type "3" |
7 |
Adjustment type "7" |
8 |
Hexagon SW10 |
9 |
Space required to remove the key |
10 |
Locking pin |
11 |
Valve mounting bores |
12.1 |
Directional spool valve NG6 |
13 |
Solenoid “a” |
14 |
Dimension for valve without manual override |
15 |
Mating connector without circuitry (separate order) |
16 |
Mating connector with circuitry (separate order) |
17 |
Switching shock damping valve, optional |
18 |
Space required to remove the mating connector |
19 |
Omitted with internal pilot oil return |
30 |
Dimension for solenoid with manual override “N” |
31 |
Dimension ( ) for valve with AC solenoid |
32 |
Dimension for valve with DC solenoid |
33 |
Space required to remove the solenoid coil |
34 |
Dimension for valve with concealed manual override "N9" |
35 |
Lock nut SW17, tightening torque MA = 10+5 Nm |
Version |
L1 |
L2 |
L3 |
L4 |
L5 |
L6 |
L7 |
L8 |
L9 |
B1 |
B2 |
ØD1 |
mm |
mm |
mm |
mm |
mm |
mm |
mm |
mm |
mm |
mm |
mm |
mm |
|
"DB 10" | 91 | 53.8 | 22.1 | 27.5 | 22.1 | 47.5 | 0 | 25.5 | 2 | 78 | 53.8 | 14 |
"DB 20" | 116 | 66.7 | 33.4 | 33.3 | 11.1 | 55.6 | 23.8 | 22.8 | 10.5 | 100 | 70 | 18 |
"DB 30" | 147.5 | 88.9 | 44.5 | 41 | 12.7 | 76.2 | 31.8 | 20 | 21 | 115 | 82.6 | 20 |
Subplate mounting with directional seat valve "6SM"
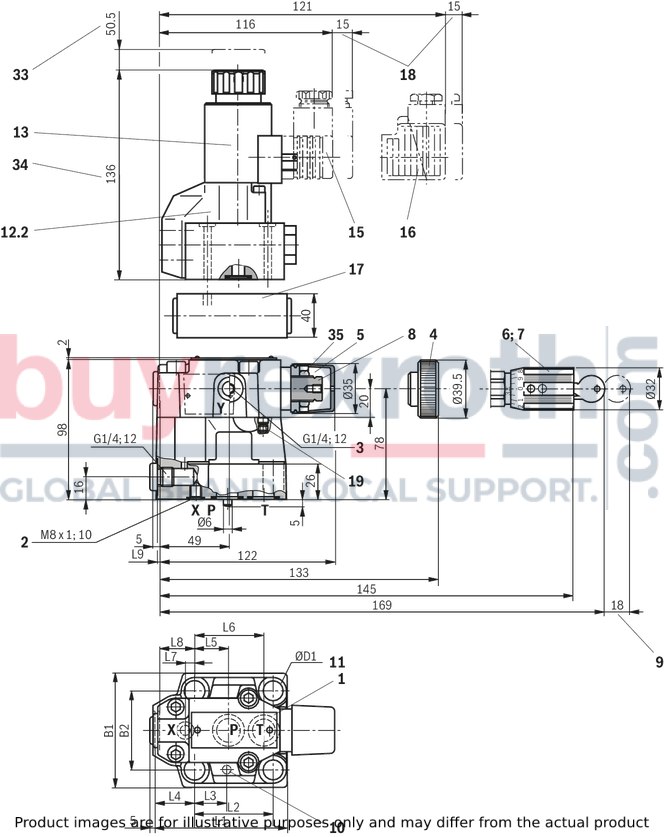
1 |
Name plate |
2 |
X port for pilot oil supply, external |
3 |
Y port for pilot oil return, external |
4 |
Adjustment type "1" |
5 |
Adjustment type "2" |
6 |
Adjustment type "3" |
7 |
Adjustment type "7" |
8 |
Hexagon SW10 |
9 |
Space required to remove the key |
10 |
Locking pin |
11 |
Valve mounting bores |
12.2 |
Directional seat valve NG6 |
13 |
Solenoid “a” |
14 |
Dimension for valve without manual override |
15 |
Mating connector without circuitry (separate order) |
16 |
Mating connector with circuitry (separate order) |
17 |
Switching shock damping valve, optional |
18 |
Space required to remove the mating connector |
19 |
Omitted with internal pilot oil return |
30 |
Dimension for solenoid with manual override “N” |
31 |
Dimension ( ) for valve with AC solenoid |
32 |
Dimension for valve with DC solenoid |
33 |
Space required to remove the solenoid coil |
34 |
Dimension for valve with concealed manual override "N9" |
35 |
Lock nut SW17, tightening torque MA = 10+5 Nm |
Pilot control valve with ("DBWC 10 or 30") or without main spool insert ("DBWC, DBWT")
Dimensions in mm

Dimensions for attached directional valve see "Subplate mounting"
Installation bore
Dimensions in mm

1 |
Name plate |
3 |
Y port for pilot oil return, external |
5 |
Adjustment type "2" |
6 |
Adjustment type "3" |
7 |
Adjustment type "7" |
8 |
Hexagon SW10 |
9 |
Space required to remove the key |
11 |
Valve mounting bores |
20 |
Seal ring |
21 |
Main spool insert |
22 |
Bore Ø32 mm can cut Ø45 mm at any point. However, it must be observed that the connection bore X and the mounting bore are not damaged! |
23 |
Support ring and seal ring are to be inserted into this bore before assembly of the main spool. |
24 |
Nozzle (separate order; recommended nozzle Ø1.0 mm) |
25 |
Seal ring |
26 |
Seal ring |
27 |
Seal ring |
28 |
Support ring |
29 |
Support ring |
35 |
Lock nut SW17, tightening torque MA = 10+5 Nm |
Valve mounting screws (separate order)
For reasons of stability, exclusively the following valve mounting screws may be used:
Version "DB 10"4 x ISO 4762 - M12 x 50 - 10.9-flZn/nc/480h/C
with friction coefficient μtotal = 0.09 … 0.14
tightening torque MA = 75 Nm ±10%
material no. R913015611 Version "DB 20"
4 x ISO 4762 - M16 x 50 - 10.9-flZn/nc/480h/C
with friction coefficient μtotal = 0.09 … 0.14
tightening torque MA = 185 Nm ±10%
material no. R913015664 Version "DB 30"
4 x DIN 912 - M18 x 50 - 10.9-flZn/nc/480h/C
with friction coefficient μtotal = 0.09 … 0.14
tightening torque MA = 248 Nm ±10%
material no. R913015903 Version "DBC", "DBC 10", "DBC 30" and "DBT"
4 x ISO 4762 - M8 x 40 - 10.9-flZn/nc/480h/C
with friction coefficient μtotal = 0.09 … 0.14
tightening torque MA = 31 Nm ±10%
material no. R913015798
Notice:
The tightening torques stated are guidelines when using screws with the specified friction coefficients and when using a manual torque wrench (tolerance ±10%).
![]() |
Required surface quality of the valve contact surface |
Safety instructions: Type-examination tested safety valves type DB…E
(Component series 5X according to Pressure Equipment Directive 2014/68/EU)
Before ordering a type-examination tested safety valve, it must be observed that for the desired response overpressure p, the maximum admissible flow qV max of the safety valve must be larger than the maximum possible flow of the system. According to Pressure Equipment Directive 2014/68/EU , the increase of the system pressure by the flow must not be higher than 10 % of the set response pressure (see component marking). Discharge lines (ports T and Y) of safety valves must end in a risk-free manner. The accumulation of fluids in the discharge lines must not be possible (AD 2000 data sheet A 2). If a lead seal at the safety valve is removed, the approval according to the PED! Basically, the requirements of the Pressure Equipment Directive 2014/68/EU and of data sheet AD 2000 A 2 have to be observed.
It is imperative to observe the application notes!
In the plant, the response pressure specified in the component marking is set at a flow of 2 l/min.
The maximum admissible flow stated in the component marking (= numerical value instead of the character "G" in the component marking, see ordering code, type-examination tested safety valves) must not be exceeded.
It applies to:
Pilot oil return “external” (= Y in the ordering key) without counter pressure in the discharge line Y, admissible counter pressure in the discharge line (port T) < 15 bar Pilot oil return “internal” (= no code in the ordering key). The maximum admissible flow is only admissible without counter pressure in the discharge line (port T).With internal pilot oil return, the system pressure increases by the counter pressure in the discharge line (port T) with increasing flow (observe AD2000 - data sheet A2 - item 6.3!).
To ensure that this increase in system pressure caused by the flow does not exceed the value of 10% of the set response pressure, the admissible flow has to be reduced dependent on the counter pressure in the discharge line (port T) (see diagrams (Safety instructions, Type-examination tested safety valves)).
It is imperative to observe the application notes!
In the plant, the response pressure specified in the component marking is set with a flow of 11 l/min. The maximum admissible flow stated in the component marking (= numerical value instead of the character "G" in the component marking, see ordering code, type-examination tested safety valves) must not be exceeded.It applies to: Pilot oil return external ("Y") without counter pressure in the discharge line Y; admissible counter pressure in the discharge line (port T) < 15 bar Pilot oil return internal ("no code"). The maximum flow is only admissible without counter pressure in the discharge line (port T).
With internal pilot oil return, the system pressure increases by the counter pressure in the discharge line (port T) due to the increasing flow (observe AD2000 - data sheet; A2, item 6.3!)
To ensure that this increase in system pressure caused by the flow does not exceed 10% of the set response pressure, the admissible flow has to be reduced dependent on the counter pressure in the discharge line (port T) (see diagrams (Safety instructions, Type-examination tested safety valves)).
Notice:
Possible unloading via the directional valve must not be applied for safety-relevant functions! If unloading is required for safety-relevant functions, an additional unloading valve must be installed.
General information
The unloading function (directional valve function with version "DBW") must not be used for safety functions! With version "B", the lowest adjustable pressure (circulation pressure) is set in case of power failure or cable break. With version "A", the pressure limiting function is set in case of power failure or cable break. Hydraulic counter pressures in port T with internal pilot oil return and/or port Y with external pilot oil return add 1:1 to the response pressure of the valve set at the pilot control.Example: Pressure adjustment of the valve by spring preload (item 9 "Product description") in the pilot control valve/adjustment type pspring = 200 bar Hydraulic counter pressure in port T with internal pilot oil return phydraulic = 50 bar => Response pressure = pspring + phydraulic = 250 bar
Mating connectors for valves with connector “K4”, without circuitry, standard
3P Z4
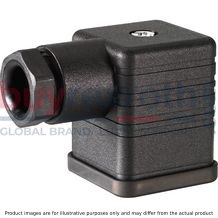
Mating connectors for valves with connector “K4”, without circuitry, standard
3P Z4
For valves with connector “K4” according to EN 175301-803 and ISO 4400, 2-pole + PE, “large cubic connector” Mating connectors for valves with one or two solenoids (individual connection)Data sheet
Spare parts & repair
Mating connectors for valves with connector “K4”, without circuitry, standard
3P Z45
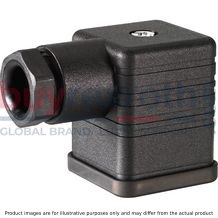
Mating connectors for valves with connector “K4”, without circuitry, standard
3P Z45
For valves with connector “K4” according to EN 175301-803 and ISO 4400, 2-pole + PE, “large cubic connector” Mating connectors for valves with one or two solenoids (individual connection)Data sheet
Spare parts & repair
Mating connectors for valves with connector “K4”, with indicator light
3P Z5L
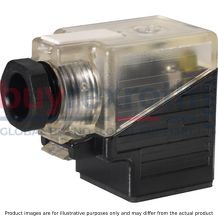
Mating connectors for valves with connector “K4”, with indicator light
3P Z5L
For valves with connector “K4” according to EN 175301-803 and ISO 4400, 2-pole + PE, “large cubic connector” Mating connectors for valves with one or two solenoids (individual connection)Data sheet
Spare parts & repair
Mating connectors for valves with connector “K4”, with indicator light and Zener diode suppression circuit
3P Z5L1
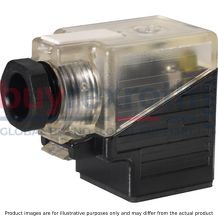
Mating connectors for valves with connector “K4”, with indicator light and Zener diode suppression circuit
3P Z5L1
For valves with connector “K4” according to EN 175301-803 and ISO 4400, 2-pole + PE, “large cubic connector” Mating connectors for valves with one or two solenoids (individual connection)Data sheet
Spare parts & repair
Mating connectors for valves with connector “K4”, with rectifier
3P RZ5
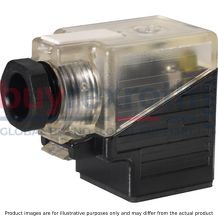
Mating connectors for valves with connector “K4”, with rectifier
3P RZ5
For valves with connector “K4” according to EN 175301-803 and ISO 4400, 2-pole + PE, “large cubic connector” Mating connectors for valves with one or two solenoids (individual connection)Data sheet
Spare parts & repair
Ordering code: Type-examination tested safety valves type DBW…E, component series 5X according to Pressure Equipment Directive 97/23/EC
NG |
Type designation |
Component marking |
Maximum flow qVmax in l/min with pilot oil return |
Set response overpressurep in bar |
|
external "Y" |
internal "–" |
||||
10 |
1 2 3 4 5 * 6 DBW 10 ▢▢▢–5X//▢▢6▢▢E |
TÜV.SV.▢ – 851.12.F.G.p |
170 230 230 230 |
130 200 200 200 |
30 ... 60 61 ... 110 111 ... 210 211 ... 350 |
25 |
1 2 3 4 5 * 6 DBW 20 ▢▢▢–5X//▢▢6▢▢E |
TÜV.SV.▢ – 852.22.F.G.p |
250 270 420 450 |
180 210 320 400 |
30 ... 60 61 ... 110 111 ... 210 211 ... 350 |
32 |
1 2 3 4 5 * 6 DBW 30 ▢▢▢–5X//▢▢6▢▢E |
TÜV.SV.▢ – 853.32.F.G.p |
600 600 650 700 |
225 340 540 580 |
30 ... 60 61 ... 110 111 ... 210 211 ... 350 |
1 ▢ |
Directional valve, normally closed |
A |
Directional valve, normally open |
B |
|
2 ▢ |
For subplate mounting |
no code |
For threaded connection |
G |
|
3 ▢ |
Hand wheel (pressure adjustment sealed, unloading or setting of a lower response pressure possible!) |
1 |
With sealed protective cap (no adjustment/unloading possible) |
2 |
|
4 ▢ |
Pressure in the designation is to be entered by the customer, e.g. pressure adjustment ≥ [si]50 bar[/si][imp]725 psi[/imp] and possible in [si]5 bar[/si] [/imp]75 psi[/imp] steps. |
150 |
5 ▢ |
Pilot oil supply and return, internal |
– 1;2) |
Pilot oil supply internal, pilot oil return external (Recommendation) |
Y 2) |
|
* ▢ |
Ordering code of the electric data e.g. |
EG24N9K4 |
6 ▢ |
NBR seals |
no code |
FKM seals |
V |
|
Value entered at the factory |
1) Dash “–” only necessary with version with attached directional valve (DBW) | |
2) External pilot oil supply “X” not possible! |
Related Products
R978910395
$1,418.00 USD
R978913196
$2,477.00 USD
R900340153
$644.00 USD
R900752414
$622.00 USD
R901034647
$4,703.00 USD