ZSF32 F0-1-1X/M/01D00
Manufacturer: Bosch Rexroth
Material #: R900574729
Model : ZSF32 F0-1-1X/M/01D00
***Disclaimer: The following summary contains information gathered from various sources such as product descriptions, technical specifications and catalogs. While efforts have been made to provide accurate details, inaccuracies may occur. It is advised to verify all information by contacting Bosch Rexroth directly.***
The Bosch Rexroth ZSF32F0-1-1X/M/01 (R900574729) is a pilot-operated check valve in a sandwich plate design, tailored for integration into hydraulic systems requiring precise flow control and directional valve setup. This model falls under the Type ZSF NG category, which is known for its robust performance in managing fluid dynamics within hydraulic circuits. It features an integrated throttle check valve that ensures stable operation across various applications.
This specific valve is designed to accommodate a high-pressure connection NG and can handle a maximum operating pressure of up to bar, while facilitating a maximum flow rate of l/min. It's important to note that when integrating this valve into a system, it is mandatory to order the appropriate nozzle separately for channel P of the upstream directional valve. The diameter of this nozzle must be carefully selected based on the prefill valve size as indicated in the schematics provided by Bosch Rexroth.
Failure to comply with this requirement may result in increased dynamic loads, which could adversely affect the operating time and longevity of the valve. The component series X and X are indicative of its generation or version, ensuring that it matches with other compatible components within the same series for seamless operation.
With its precise engineering and reliable performance, the Bosch Rexroth ZSF32F0-1-1X/M/01 check valve is an essential component in hydraulic systems where controlled flow and backflow prevention are critical for optimal machinery function.
$1,395.00 USD
More are expected on October 30, 2025
Qty | Price | Savings |
---|---|---|
5+ | $1,360.12 USD | $34.88 USD |
Status: This product is temporarily out of stock.
Qty: Delivered as early as October 30, 2025 when ordered in
This product is eligible for factory repair.
Pilot operated check valve in sandwich plate design Directional valve set-up, optional High-pressure connection (NG32 … 160) Integrated throttle check valve (NG50, 63, 80 and 200)
Notice:
With size 32, 40, 100, 125, 160 a nozzle (separate order) must imperatively be provided in channel P of the upstream directional valve. The nozzle diameter is to be designed according to the prefill valve size (see "Schematics").
In case of non-compliance, increased dynamic loads may occur having detrimental effects on the operating time.
Type ZSF… (NG32, 40, 100, 125, 160)
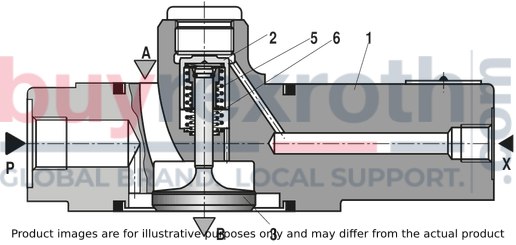
Type ZSF… (NG200)
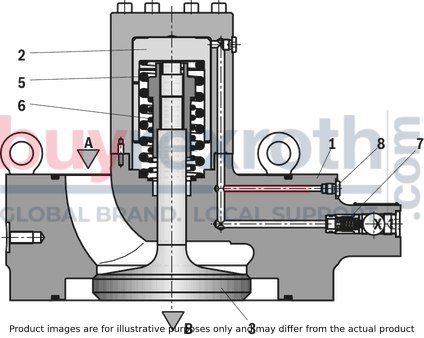
01 |
02 |
03 |
04 |
05 |
06 |
07 |
08 |
09 |
10 |
||||
ZSF |
F |
0 |
– |
1 |
– |
/ |
M |
/ |
01 |
* |
01 |
Prefill valve, sandwich plate design |
ZSF |
02 |
Size 32 |
32 |
Size 40 |
40 |
|
Size 50 |
50 |
|
Size 63 |
63 |
|
Size 80 |
80 |
|
Size 100 |
100 |
|
Size 125 |
125 |
|
Size 160 |
160 |
|
Size 200 |
200 |
|
Type of connection |
||
03 |
Flange connection |
F |
04 |
Without pre-decompression (With pre-decompression on request) |
0 |
Cracking pressure main poppet |
||
05 |
pÖ ≈ 0,12 bar |
1 |
06 |
Component series 10 ... 19 (10 ... 19: unchanged installation and connection dimensions) (NG32 … 100 and NG160) |
1X |
Component series 20 ... 29 (20 ... 29: unchanged installation and connection dimensions) (Size 125 1) and 200) |
2X |
|
Seal material |
||
07 |
NBR seals |
M |
FKM seals |
V |
|
Observe compatibility of seals with hydraulic fluid used. |
||
Connection version |
||
08 |
Mounting cavities with pipe thread according to ISO 228, DIN EN 3852-part 2 |
01 |
Pipe thread “UNF/UN” according to ANSI/ASME B 1.1 |
12 |
|
Nozzle bore |
||
09 |
NG32, 40, 100, 125, 160 (without throttle check valve) |
no code |
NG50, 63, 80 (Possibility to include a throttle check valve, not fitted) |
D00 |
|
NG50, 63 (throttle check valve Ø0,8 mm) |
D08 |
|
NG80 (throttle check valve Ø1 mm) |
D10 |
|
NG200 (throttle check valve Ø4 mm) |
D40 |
|
10 |
Further details in the plain text |
* |
1) Compatible with series 1X |
general
Size |
32 | 40 | 50 | 63 | 80 | 100 | 125 | 160 | 200 | |
Weight |
kg |
3.5 | 4.2 | 5.5 | 7 | 10 | 15 | 26 | 47 | 150 |
Installation position 1) |
any | |||||||||
Ambient temperature range |
°C |
-30 … +80 |
1) | Working direction of the control spool |
hydraulic
Size |
32 | 40 | 50 | 63 | 80 | 100 | 125 | 160 | 200 | ||
Maximum operating pressure |
Port P |
bar |
350 | ||||||||
Anschluss A |
bar |
16 | |||||||||
Port B |
bar |
350 | |||||||||
Anschluss X |
bar |
150 | |||||||||
Cracking pressure 1) |
bar |
≈ 0.12 | |||||||||
Flow (Δp = 0.3 bar) |
Depending on the case of application, see below | ||||||||||
Druckflüssigkeit |
see table | ||||||||||
Hydraulic fluid temperature range |
°C |
-30 … +70 | |||||||||
Viscosity range |
mm²/s |
10 … 800 | |||||||||
Maximum admissible degree of contamination of the hydraulic fluid 2) |
Class 20/18/15 according to ISO 4406 (c) |
1) | Pressure differential at the main poppet for overcoming the spring force |
2) | The cleanliness classes specified for the components must be adhered to in hydraulic systems. Effective filtration prevents faults and simultaneously increases the life cycle of the components. For the selection of the filters, see www.boschrexroth.com/filter. |
Hydraulic fluid |
Classification |
Suitable sealing materials |
Standards |
Data sheet |
|
Mineral oils |
HL, HLP, HLPD, HVLP, HVLPD |
NBR, FKM |
DIN 51524 |
90220 |
|
Bio-degradable |
Insoluble in water |
HETG |
FKM |
ISO 15380 |
90221 |
HEES |
FKM |
||||
Soluble in water |
HEPG |
FKM |
ISO 15380 |
||
Flame-resistant |
Water-free |
HFDU (glycol base) |
FKM |
ISO 12922 |
90222 |
HFDU (ester base) |
FKM |
||||
HFDR |
FKM |
||||
Containing water |
HFC (Fuchs Hydrotherm 46M, Petrofer Ultra Safe 620) |
NBR |
ISO 12922 |
90223 |
|
Important information on hydraulic fluids: For further information and data on the use of other hydraulic fluids, please refer to the data sheets above or contact us. There may be limitations regarding the technical valve data (temperature, pressure range, life cycle, maintenance intervals, etc.). The ignition temperature of the hydraulic fluid used must be 50 K higher than the maximum surface temperature. Flame-resistant – containing water: Maximum pressure differential 210 bar, otherwise, increased cavitation erosion Life cycle as compared to operation with mineral oil HL, HLP 30 … 100% Maximum hydraulic fluid temperature 60 °C Bio-degradable and flame-resistant: If this hydraulic fluid is used, small amounts of dissolved zinc may get into the hydraulic system. |
Flow qV in l/min (A to B) for different cases of application (Δp = 0,3 bar)
Size |
32 | 40 | 50 | 63 | 80 | 100 | 125 | 160 | 200 | |
Case of application 1 |
l/min |
200 | 300 | 500 | 800 | 1200 | 1900 | 3000 | 4200 | 7000 |
Case of application 2 |
l/min |
170 | 250 | 400 | 650 | 1000 | 1600 | 2600 | 3900 | 6510 |
Case of application 3 |
l/min |
140 | 220 | 360 | 560 | 900 | 1400 | 2200 | 3400 | 5670 |
Case of application 4 |
l/min |
100 | 150 | 240 | 380 | 620 | 950 | 1500 | 2300 | 3850 |
Case of application 5 |
l/min |
70 | 110 | 170 | 280 | 450 | 700 | 1100 | 1690 | 2800 |
Case of application 1
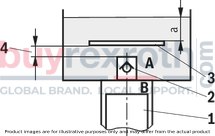
Case of application 2
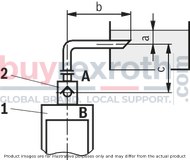
Case of application 3
Size of the filling tank at least 1.5 x cylinder content
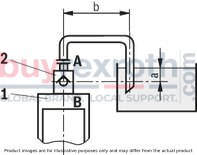
Case of application 4
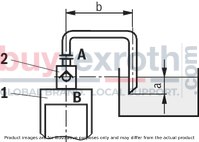
Case of application 5
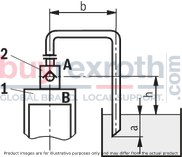
Information on case of application 2 to 5
For limit areas, please contact us. It is often enough, to select a pipeline which is one size larger.
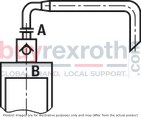
Note:
Wrong dimensioning of prefill valve and suction line may cause cavitation and consequential damage.
1 |
Cylinders |
2 |
Prefill valve |
3 |
This sheet is not included in the scope of delivery. With smaller tank dimensions and minimum hydraulic fluid level (a), it prevents the formation of tunnels. |
4 |
Observe the supply cross-section |
a |
at least 300 mm with extended cylinder |
b |
up to 1000 mm with the specified maximum flows |
c |
h ≤ 500 mm |
h |
300 mm ≤ h < 500 mm |
For applications outside these parameters, please consult us!
(measured with HLP46, ϑOil = 40 ±5 °C)
Size 32, 40, and 50
Pressure differential Δp between ports A and B dependent on the flow qV (A to B).

Size 63, 80 and 100
Pressure differential Δp between ports A and B dependent on the flow qV (A to B).

Size 125, 160, and 200
Pressure differential Δp between ports A and B dependent on the flow qV (A to B).

Without throttle check valve, NG32, 40, 100, 125, 160
Separate, external nozzle fitting required (see "Dimensions - Nozzle fitting")
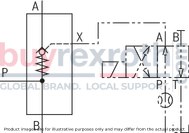
With throttle check valve, NG50, 63, 80
Throttle check valve installed at the factory; no nozzle required

NG200
Throttle check valve installed at the factory; no nozzle required
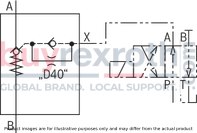
NG32 … 160
Dimensions in mm
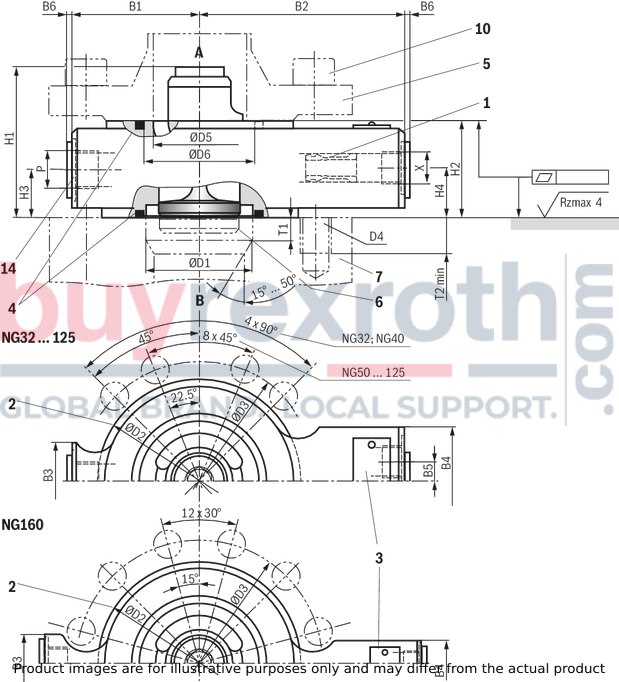
![]() |
Required surface quality of the valve contact surface |
1 |
Throttle check valve (only NG50, 63, 80, 200) |
2 |
Centering diameter |
3 |
Name plate |
4 |
Seal rings |
5 |
Counterflange (separate order, see "dimensional proposal for counterflange") |
6 |
Stroke of main poppet (see "Poppet geometry and determination of the minimum pilot pressure") |
7 |
Note: Valve contact face (e.g. pressing cylinders, bearing structures, etc.) must be sufficiently rigid. The prefill valve must not be loaded by bending. |
9 |
Space required to remove the mating connector |
10 |
Valve mounting screws (separate order) |
11 |
Threads for transport device (ring bolts), evenly distributed to circumference |
12 |
Measuring point, tightening torque MA = 30 Nm ±10% |
13 |
Damping nozzle M8 x 1 |
14 |
Additional pressure port; if not used, seal in a hydraulically tight way by means of suitable plug screws. |
NG |
B1 |
B2 |
B3 |
B4 |
B5 |
B6 |
ØD1 |
ØD2 |
ØD3 |
D4 |
ØD5 |
ØD6 |
H1 |
H2 |
H3 |
H4 |
P |
T1 |
T2 |
X |
|
mm |
mm |
mm |
mm |
mm |
max. mm |
mm |
mm |
mm |
mm |
mm |
mm |
mm |
mm |
mm |
mm |
mm |
min. mm |
||||
32 | 65 | 110 | 40 | 55 | 7.5 | 1.5 | 46 | 93 | 110 | ± 0.2 | M16 | 42 | 49.5 | 77 | 50 | 26.5 | 26.5 | G1/2 | 8 | 30 | G1/4 |
40 | 70 | 115 | 40 | 55 | 7.5 | 1.5 | 58 | 108 | 125 | ± 0.2 | M16 | 52 | 61.5 | 80 | 50 | 26.5 | 26.5 | G1/2 | 10 | 35 | G1/4 |
50 | 110 | 140 | 40 | 55 | 7.5 | 1.5 | 71 | 128 | 145 | ± 0.2 | M16 | 70 | 75.7 | 97 | 50 | 26.5 | 26.5 | G1/2 | 12 | 30 | G1/4 |
63 | 115 | 145 | 45 | 55 | 7.5 | 1.5 | 90 | 143 | 160 | ± 0.2 | M16 | 83 | 97.7 | 110 | 55 | 27.5 | 27.5 | G3/4 | 14 | 35 | G1/4 |
80 | 125 | 160 | 45 | 55 | 7.5 | 1.5 | 107 | 169 | 190 | ± 0.2 | M20 | 100 | 112 | 123 | 60 | 30 | 30 | G3/4 | 16 | 30 | G1/4 |
100 | 140 | 190 | 55 | 55 | 7.5 | 1.5 | 132 | 212 | 240 | ± 0.2 | M27 | 124 | 138.5 | 145 | 65 | 32.5 | 40 | G1 | 25 | 55 | G3/8 |
125 | 180 | 210 | 65 | 60 | 0 | 1.5 | 170 | 248 | 280 | ± 0.2 | M30 | 148 | 176 | 215 | 75 | 37.5 | 50 | G1 | 33 | 50 | G3/8 |
160 | 220 | 255 | 70 | 60 | 0 | 1.5 | 220 | 310 | 345 | ± 0.2 | M33 | 200 | 233 | 279 | 95 | 48.5 | 68 | G1 1/4 | 55 | 50 | G1/2 |
200 | - | - | - | - | - | - | - | - | - | - | - | - | - | - | - | - | - | - | - | - | - |
NG200
Dimensions in mm
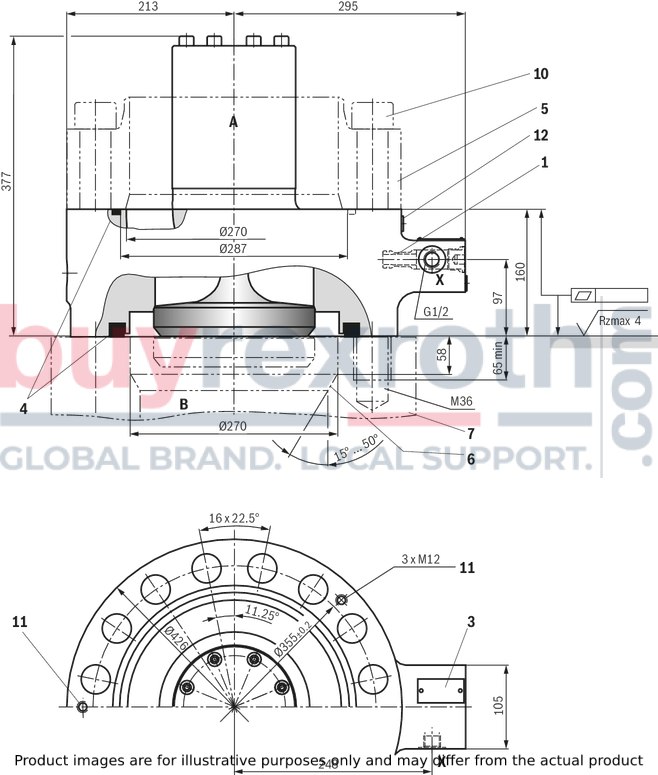
![]() |
Required surface quality of the valve contact surface |
1 |
Throttle check valve (only NG50, 63, 80, 200) |
3 |
Name plate |
4 |
Seal rings |
5 |
Counterflange (separate order, see "dimensional proposal for counterflange") |
6 |
Stroke of main poppet (see "Poppet geometry and determination of the minimum pilot pressure") |
7 |
Note: Valve contact face (e.g. pressing cylinders, bearing structures, etc.) must be sufficiently rigid. The prefill valve must not be loaded by bending. |
10 |
Valve mounting screws (separate order) |
11 |
Threads for transport device (ring bolts), evenly distributed to circumference |
12 |
Measuring point, tightening torque MA = 30 Nm ±10% |
Dimensional proposal for counterflange (pos. 5)
Dimensions in mm

![]() |
Required surface quality of the valve contact surface |
Size |
32 | 40 | 50 | 63 | 80 | 100 | 125 | 160 | 200 | |
Maximum operating pressure pmax 1) |
350 bar | |||||||||
Recommended flange material |
C22 | S355J2G3 |
1) | When using other counterflanges than the ones specified here, it may be necessary to reduce the operating pressure. |
Form of the welding gap (15):
Standard version s ≤ 16 gap form 22 DIN 2559 s > 16 gap form 3 DIN 2559 special version see DIN 2559
NG |
Flange |
Neck |
Raised face |
||||||||||
Ød1 |
Ød2 |
ØD |
ØD5+2 |
b |
Øk |
h1 |
Ød3 |
s |
r |
h2 |
Ød4 |
f |
|
mm 1) |
mm |
mm |
mm |
mm |
mm |
mm |
mm |
mm 1) |
mm |
mm |
mm |
mm |
|
32 | 48.3 | 18 | 150 | 42 | 22 | 110 | 49 | 64 | 3.2 | 6 | 7 | 88 | 3 |
40 | 60.3 | 18 | 165 | 52 | 29 | 125 | 57 | 75 | 3.6 | 6 | 8 | 102 | 3 |
50 | 76.1 | 18 | 185 | 70 | 34 | 145 | 64 | 90 | 3.6 | 6 | 10 | 122 | 3 |
63 | 88.9 | 18 | 200 | 83 | 43 | 160 | 77 | 105 | 3.6 | 8 | 12 | 138 | 3 |
80 | 114.3 | 22 | 235 | 100 | 51 | 190 | 95 | 134 | 3.6 | 8 | 12 | 162 | 3 |
100 | 139.7 | 30 | 295 | 124 | 62 | 240 | 116 | 168 | 4 | 8 | 12 | 188 | 3 |
125 | 168.3 | 33 | 345 | 148 | 79 | 280 | 138 | 202 | 4.5 | 10 | 12 | 218 | 3 |
160 | 219.1 | 36 | 415 | 200 | 118 | 345 | 186 | 256 | 5.9 | 10 | 16 | 285 | 3 |
200 | 273 | 39 | 420 | 270 | 100 | 355 | 140 | 292 | 6.5 | 6 | 16 | - | - |
1) | For seamless steel pipes, wall thickness 16 according to DIN EN 10220 |
Valve mounting screws, counterflange (separate order)
Hexagon socket head cap screw ISO 4762 - 10.9-flZn (or DIN 912 - 10.9-flZn) |
Counterflange |
||||
Size |
Dimensions |
Quantity |
Tightening torque MA in Nm (±5 %) 1) |
Material number |
Material number |
32 |
M16 x 100 |
4 |
240 |
R913015640 |
R900842693 |
40 |
M16 x 110 |
4 |
240 |
R913015642 |
R900825610 |
50 |
M16 x 110 |
8 |
240 |
R913015642 |
R900826441 |
63 |
M16 x 130 |
8 |
240 |
R913014713 |
R900849622 |
80 |
M20 x 140 |
8 |
460 |
R913015675 |
R900862915 |
100 |
M27 x 180 |
8 |
1150 |
R913059494 |
R900834583 |
125 |
M30 x 200 |
8 |
1600 |
R913015753 |
R900861508 |
160 |
M33 x 260 |
12 |
2200 |
R913001904 |
R900846478 |
200 |
M36 x 320 |
16 |
2600 |
R913050473 |
R901205467 |
1) | Friction coefficient μtotal = 0.09 … 0.14; please adjust in case of changed surfaces; use a manual torque wrench. |
Notice:
The information on the hexagon socket head cap screws (type, length, tightening torque) refers exclusively to the use with the counterflanges listed above.
Poppet geometry and determination of the minimum pilot pressure
Dimensions in mm
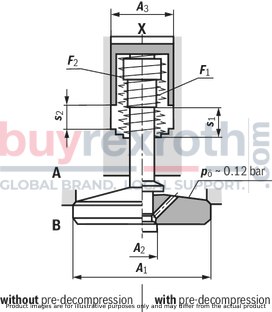
A1 |
Effective area of the main poppet |
A2 |
Effective area of the pilot poppet |
A3 |
Effective area of the control spool |
s1 |
Stroke of the main poppet |
s2 |
Stroke of the control spool |
F1 |
Spring force of the valve spring |
F2 |
Spring force of the compression spring of the control spool |
Vst |
Pilot volume for opening the valve |
pÖ |
Cracking pressure (pressure differential at the main poppet for overcoming the spring force F1) |
pSt |
Pilot pressure at port X |
pB |
System pressure at port B |
NG |
A1 |
A2 1) |
A3 |
s1 |
s2 |
F1 |
F2 |
VstX |
Unchecking ratio |
|
cm² |
cm² |
cm² |
mm |
mm |
N |
N |
cm³ |
Without pre-decompression |
With pre-decompression 2) |
|
32 | 8.04 | 0.5 | 2.01 | 8.5 | 6.5 | 9 … 22 | 58 … 109 | 1.3 | 4 | 0.3 |
40 | 13.52 | 0.79 | 3.14 | 10 | 7 | 14 … 29 | 93 … 162 | 2.2 | 4.3 | 0.3 |
50 | 21.24 | 1.13 | 4.71 | 12.5 | 9 | 23 … 49 | 149 … 261 | 4.2 | 4.5 | 0.3 |
63 | 32.67 | 1.77 | 7.07 | 14.5 | 11 | 35 … 63 | 206 … 348 | 7.8 | 4.6 | 0.3 |
80 | 49.02 | 2.54 | 10.18 | 17 | 13 | 57 … 127 | 310 … 579 | 13.2 | 4.8 | 0.3 |
100 | 73.13 | 3.8 | 15.9 | 22 | 15 | 81 … 193 | 476 … 952 | 25.5 | 4.6 | 0.2 |
125 | 120.76 | 5.72 | 28.27 | 30 | 22.5 | 135 … 319 | 878 … 1,667 | 59.4 | 4.3 | 0.2 |
160 | 196.07 | 9.08 | 45.36 | 40 | 27 | 241 … 516 | 1,335 … 2,395 | 122 | 4.3 | 0.2 |
200 | 314.16 | - | 78.54 | 48 | 34 | 425 … 850 | 2,389 … 3,822 | 267 | 4 | - |
1) | Is omitted for version "without pre-decompression" (ZSF...0...) |
2) | Upon request |

Example: Type ZSF32...
pB = 30 bar ;
pSt = 4.0 x 30 bar = 120 bar
Nozzle fitting
Size |
32 | 40 | 50 | 63 | 80 | 100 | 125 | 160 | 200 | |
Nozzle Ø |
mm |
0.8 | 0.8 1) | 1 1) | 1 | 1.2 | 1.5 | 4 1) |
1) | Throttle check valve installed at the factory (not version “00”); no nozzle required |
Related Products
R900411314
$696.00 USD
R900904559
$465.00 USD
R900955777
$2,015.00 USD
R900228860
$3,042.00 USD
R978017583
$1,723.00 USD